Volume 6 - Year 2023- Pages 01-07
DOI: 10.11159/ijci.2023.001
Proof-of-Concept Laboratory-Scale Production of ‘Sand-like’ Material using Clayey Soil
J. W. Koh1, S. Subramanian1, S. H. Chew1, K. E. Low1, Y. C. Tan2, C. S. Teo2, J. M. J. Lee2, M. Y. C. Koh2
1National University of Singapore, Department of Civil and Environmental Engineering
21 Lower Kent Ridge Road, Singapore 119077
ceekohj@nus.edu.sg; subramanian@nus.edu.sg
2Housing & Development Board, Building & Infrastructure
HDB Hub, 480 Lorong 6 Toa Payoh, Singapore 310480
Abstract - Sand is always the ideal infilling material for a land reclamation project due to its ease in placement, can be compacted easily in-situ, high strength and good drainage properties. However, there is a general shortage of sand. Hence, an alternate material that possesses “sand-like properties” is needed. Converting soft clayey soils into material with “sand-like” properties via “sintering” technology can be an alternative. It is a thermal process of converting fine loose particles in the soft clayey soil into a solid and coherent product via mineral and chemical change. A few processes are involved in this “sintering technology” to produce sand-like material. This research focuses on the laboratory-scale study on the effect of various operating conditions of these processes to produce this “sand-like” material. The effect of the high-temperature sintering schedule (e.g. sintering temperature, ramp-up rate, duration of sintering process) on the properties of the sintered clay product was studied. It was found that a controlled raw clay particle size limited to 3 – 5 mm, a sintering temperature at 900 °C, and a dwelling duration of more than one hour is needed to produce an almost complete sintered product. The dry loose bulk density of this sintered product is in the range of 1139–1187 kg/m3. It was found to have a mean compressive strength of 11 MPa and 3.7 MPa in the longitudinal and transverse direction, respectively, and a friction angle (about 35 – 37°) that falls within the category of medium dense sand. Moreover, the permeability of this “sand-like” material was found to be about 1×10-3 m/s, which is in the range of the gravel-sand mixtures category. The results suggest that the soft soil can be transformed into “sand-like” material by using the proposed sintering technology.
Keywords: Sand-like properties, Clayey soils, Sintering technology, Sintered clay product.
© Copyright 2023 Authors - This is an Open Access article published under the Creative Commons Attribution License terms. Unrestricted use, distribution, and reproduction in any medium are permitted, provided the original work is properly cited.
Date Received: 2022-11-26
Date Revised: 2023-01-03
Date Accepted: 2023-01-15
Date Published: 2023-04-14
1. Introduction
Singapore’s land scarcity and continued population and economic growth drive its need for land reclamation. Since the 1960s, Singapore’s land area has increased by about 20 – 25 % via many land reclamation projects over the years [1]. A traditional reclamation project requires a tremendous amount of sand as the infilling material. Unfortunately, the sand shortage has become a worldwide problem [2]. Thus, there is an urgent need to find an alternative infilling material.
In recent years, soft clayey soil generated from excavation works, basement construction and deep tunnelling works has become an alternative fill material in Singapore’s land reclamation project. It is found that the excavated soft clayey soil possesses a low permeability and low bearing capacity characteristic. Hence, further soil improvement is needed to enhance the stability of the ground when this excavated soft clayey soil is used as the infilling material. Using excavated clayey soil greatly reduced the reliance on the sand, yet there are areas when sand material is still needed. Hence, a further improvement is to convert this clayey soil into “sand-like” material. .
Therefore, this research studies the feasibility of transforming the excavated soft clayey soil into a “sand-like” material using “sintering” technology. The “sintering technology” involves multiple processes, including filtering, dewatering, granulating, and high-temperature sintering. The high-temperature sintering process is a thermal process of converting fine loose particles of clayey soil into a solid and coherent product of a more stable mineral and chemical composition. The heterogeneous nature of the excavated soft clayey soil, due to the different locations of the excavation works across Singapore, will make manufacturing “sand-like” infilling material more feasible than turning them into other ceramic products, such as pottery and semiconductor products.
This paper discusses the multiple processes involved in the production of the “sand-like” infilling material, including filtering, dewatering, granulating, sintering, and cooling. It was then followed by an investigation of the engineering properties of the sintered products through a series of properties tests. The effect of the high-temperature sintering schedule (e.g. sintering temperature, ramp-up rate, duration of sintering process) on the properties of the sintered clay product was studied. The test results were compared with the actual sand fill’s engineering properties to assess the sintered product’s feasibility as infilling material for land reclamation.
2. Mineral Changes in Sintering Process
The main components of the un-fired granules are clay minerals that have the phyllosilicates’ structure. In Singapore Marine clay, is dominated by mineral kaolinite, Al4[Si4 O10](OH)8. Other than kaolinite, clay also contains other minerals like quartz, SiO2 and feldspar. After the high-temperature sintering process, the kaolinite-quartz-feldspar mixes would transform into a solid and coherent product. Kaolinite undergoes dehydroxylation (loses structural water) and turns into Metakaolinite at about 500 − 600 ° [3]–[5]. A highly viscous Silica and Alumina (Al2 O2)-rich liquid appear in between the particles at 800 °C; this liquid created capillary forces that densify the particles and increase the cohesion of the particles at elevated temperature [5]. This formation of liquid phase sintering is also called vitrification, where this process shrinks the particles and increases their strength [6]. At a higher temperature (i.e. ≥ 1000 °C), metakaolinite transform into high-strength crystalline mullite and amorphous silica [3], [4], [6]–[8].
3. Excavated Soft Clayey Soil
The excavated soft clayey soil is grey in colour and contains a small amount of gravel and sand. The water content of the excavated soft clayey soil is in the range of 70 – 80 %; its liquid limit is about 75 – 80 %, and its plastic limit is around 33 – 38 %. The particle size distribution of a few random soil samples is shown in Table 1. Based on the unified soil classification system (USCS), the soil type is classified as inorganic clays of high plasticity, fat clays (CH).
Table 1: Particle size distribution of the soft clayey soil.
Gravel (%) |
Sand (%) |
Silt (%) |
Clay (%) |
1 – 3 |
2 – 18 |
31 – 43 |
36 – 56 |
4. Methodology
The excavated soft clayey soil was first filtered to remove gravel and sand, as gravel and sand are inert in the sintering process, which would result in the wastage of heat energy. The filtered soil was transferred into a 105 °C oven to reduce the moisture content, which resulted in low adhesion. The low adhesion of soil would ease the mechanical operation of the granulating process. Based on experience, a high moisture content soft soil repeatedly stuck to the metal parts of the granulation machine. The higher adhesion value between the clay and metal surface will lead to a higher force needed to separate the soil away from the metal surface. Adhesion between clayey soils and other surfaces is partially caused by the surface tension of water in the soil’s void, which is related to the moisture content of the soil. A study showed that this adhesion could be expressed as a “friction force” acting on the interface and depends on the soil moisture content [9]. It revealed that soil-metal friction force (i.e., adhesion) increased with increasing moisture content for sandy and clayey soil to a certain moisture content value. Beyond some “optimum” moisture content value, the adhesion would significantly decrease when the soil’s moisture content increased. This phenomenon can be classified into three phases: friction, adhesion, and lubrication [10]. The friction phase occurs when the soil has little moisture; the adhesion coefficient is the smallest in this phase. In the adhesion phase, the increment in moisture causes the moisture layer between the soil and metal to expand and increases the adhesive forces. In the lubrication phase, the increase in moisture is so high that it reduces the adhesive force at the interface. The soil’s moisture layer expanded so much that free water is present on the soil metal surface at this final stage.
Based on the conditions described in the three phases above, the required moisture content of the soft clayey soil considered “ideal” for the granulation process should fall within the later stage of the friction phase and the early stage of the adhesion phase. Therefore, determining the range of ideal moisture content for the granulation process is essential. In general, the peak adhesion would lie between the liquid limit and the plastic limit of the clay. Few studies narrowed the range by stating that the maximum adhesion value is near the plastic limit [11], [12]. From these studies, it can be concluded that the ideal moisture content of soft clayey soil for the granulation process is near (or slightly lower than) the plastic limit. In this study, the original clayey soil was placed into an oven at 105 °C to reduce the moisture content to around 30 – 35 %, which is within the plastic limit of Singapore marine clay. This dryer soil paste is then ready for the granulating process, which makes the clayey soils into small diameter balls.
The dryer soil paste was granulated into 3-5 mm in lengths and 3 mm in diameter of cylindrical shape unfired ‘green’ granules. Currently, the particle size of 3 mm is the upper limit; the actual production of the sand-like material in the future will include some smaller particles. Figure 1 shows the ‘green’ granules in this study. The ‘green’ granules were air-dried for a day before proceeding to the high-temperature sintering process.
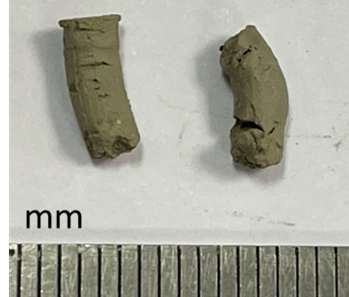
The critical process of the sintering technology is the high-temperature sintering process, with a specific firing schedule. The firing schedule is usually set based on the requirement of the end product. It would require a few rounds of sintering trial to confirm the final firing schedule. In conventional clay ceramic production, the minimum clay ceramic sintering temperature is around 900-950 °C in order to achieve the desired bond between particles [13]. Finally, the sintered clay product is completed after it cooled down to room temperature.
In order to identify the suitable sintering temperature, Thermogravimetric analysis (TGA) testing was conducted on the clayey soil to investigate the correct sintering temperature that is required to form metakaolinite. The TGA analysis plot of the clayey soil is illustrated in Figure 2. A rapid weight loss occurred from 400 °C to around 700 °C, and a peak in the derivative of weight loss indicates that decomposition occurred at approximately 500°C. This change in mass is attributed to the dehydroxylation process where kaolinite decomposed into Metakaolinite. Eventually, the reduction in mass stabilized at 800 – 900 °C, demonstrating the completion of the dehydroxylation process. The range of dehydroxylation process required temperature obtained in this TGA analysis is aligned with other research reports [3]–[5].
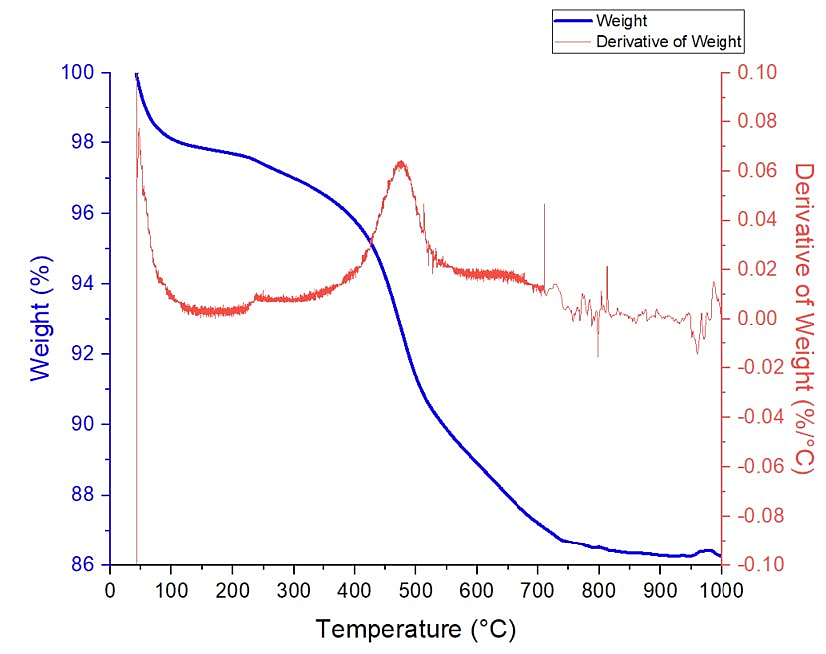
In this study, the ‘green’ granules were placed into a laboratory Muffle Furnace to sinter at four firing schedules. Table 2 shows the firing schedules; it has two variable operation parameters: the target sintering temperature and the dwelling duration. In this study, the temperature ramping rate was fixed at 300 °C/hr for all the tests. This slow temperature ramping rate is needed to prevent a drastic change in temperature experienced by the granules because a drastic change in temperature within a very short time resulted in an explosion effect on the granules during the sintering process [14]. The explosion is due to the moisture within the granule turning into steam and trying to escape from it.
Test SL-1 and SL-2 adopted the same target sintering temperature of 900 °C. This sintering temperature was chosen based on the TGA analysis and literature reviews. Under this temperature, vitrification is expected to occur at this firing schedule and form a strong particle.
Test SL-1 had a dwelling duration of one (1) hour, while the dwelling duration of Test SL-2 was half an hour. The comparison between Test SL-1 and Test SL-2 shows the effect of dwelling duration on the sintered product’s characteristics.
A lower target sintering temperature of 500 °C and a longer dwelling duration of one (1) hour and two (2) hours were employed in Test SL-3 and Test SL-4, respectively. Metakaolinite would appear at the sintering temperature of 500 °C; hence, the result of Test SL-3 and SL-4 provide further insights into the properties of the end product that possesses metakaolinite (not going through the vitrification process) and with dissimilar dwelling duration. After the sintering process, the end sintered products were cooled down to room temperature.
Table 2: Firing schedules of the sand-like materials.
Tests |
Target Sintering Temperature (°C) |
Dwelling Duration (hr) |
SL-1 |
900 |
1 |
SL-2 |
900 |
0.5 |
SL-3 |
500 |
1 |
SL-4 |
500 |
2 |
5. Characterization of “Sand-like” Material
All the sintered products were left to cool down at room temperature for at least a day before proceeding to the visual inspection to check the sintered percentage within the sintered specimen. Furthermore, engineering properties tests, such as the bulk density test, static compression test, consolidated drained triaxial shear test and constant head permeability test, were conducted to determine the dry loose bulk density, ultimate compressive strength, friction angle and permeability, respectively.
5.1. Sintered Percentage
Five samples from each test were randomly chosen to be crushed open. Observations have been made on the sintered area of the core of the sintered product, judging based on the colour composition within, where the orange-coloured areas are those sintered and the dark grey-coloured areas are those of non-sintered (original colour of the soft soil is dark grey due to presence of iron oxide in the marine clay). The final appearance of the iron oxide-rich soil after thermal treatment is dark orange[15]. Figure 3(a) and (b) show examples of a not-fully sintered and a fully sintered crushed sintered clay, respectively.
The approximated percentage of the sintered area of a specimen can be calculated based on the sintered area at the centre of the product over the total area at the centre of the product. This approximation method might not be precisely accurate, but it was good enough for this preliminary study. Figure 4 illustrates the approximate sintered percentage of the tests.
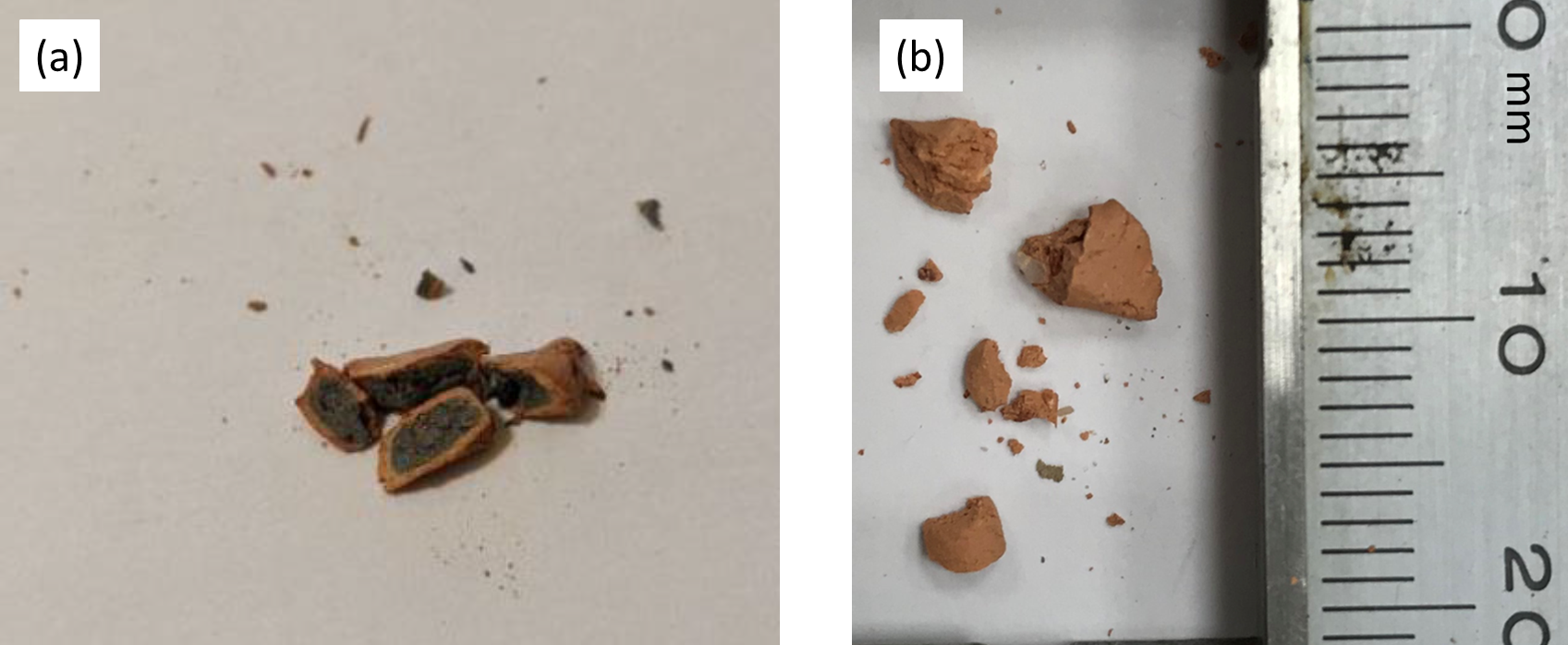
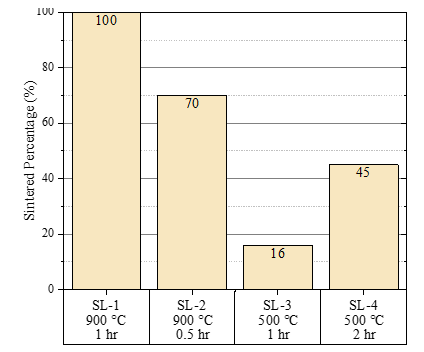
It is found that the sintered product that underwent sintering at 900 °C has a larger sintered area than that sintered at 500 °C. This result suggests that 500 °C is far below the required temperature to transform the ‘green’ granule into a coherent product. The comparison between the sintered product that underwent sintering at different dwelling durations but the same temperature (i.e., between Test SL-1 versus Test SL-2, and Test SL-3 versus Test SL-4) shows that the tests that had a longer dwelling duration achieved a larger sintered area than those with a shorter dwelling duration. A conclusion that can be drawn is that a longer dwelling duration allows more heat to travel into the granule, hence allowing complete sintering.
5.2. Engineering Properties of “Sand-like” Material
The sintered products were then subjected to a series of standard geotechnical laboratory tests to ascertain that they were similar to the sand material, hence justifying the name “sand-like” material.
5.2.1. Dry Loose Bulk Density
The dry loose bulk density of the “sand-like” material is found to be in the range of 1139–1187 kg/m3, which is slightly lower than a typical dry loose uniformly graded sand density (1400 kg/m3) [16].
5.2.2. Compressive Strength
A compression testing machine with a maximum testing load of 100 kN was used in this study to obtain the ultimate unconfined compressive strength. Forty-two (42) randomly chosen samples from each of the four (4) test series were subjected to the compression test with a strain rate of 1 mm/min, where twenty-one (21) specimens were tested on the longitudinal axis and the other half of specimens tested on the transverse axis. In the longitudinal axis, the specimen was standing ‘vertically’ up, with the flat surfaces of the cylindrical sample in contact with the top and bottom platen of the compression machine. While for the transverse face, the flat surfaces were perpendicular to the top and bottom platen. Figure 5 illustrates a single specimen position when subjected to the compression test until failure occurs. The compressive strength value of the longitudinal direction can be derived by dividing the yield force by the cross-section area of the specimen. In comparison, the derivation of the strength value at the transverse direction would require the Hertzian contact stress theory[17].
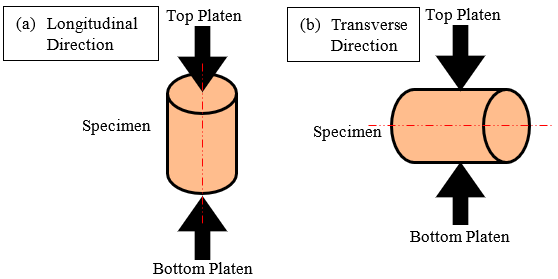
It should, however, remember that the individual specimen is not in a perfect cylindrical shape. The imperfect shape of the specimen would reduce the accuracy of test results. Thus, as many as twenty-one (21) specimens were tested in each direction to get the most accurate mean compressive strength.
The mean compressive strength of the “sand-like” material in the longitudinal and transverse directions can be found in Figure 6. As shown, the strength of the “sand-like” material when tested along the longitudinal direction is higher than that along the transverse direction. In addition, most of the “sand-like” material that underwent sintering at a higher temperature and a longer dwelling duration possessed higher compressive strength, except that the transverse direction compressive strength of Test SL-1 and SL-2 was almost the same.
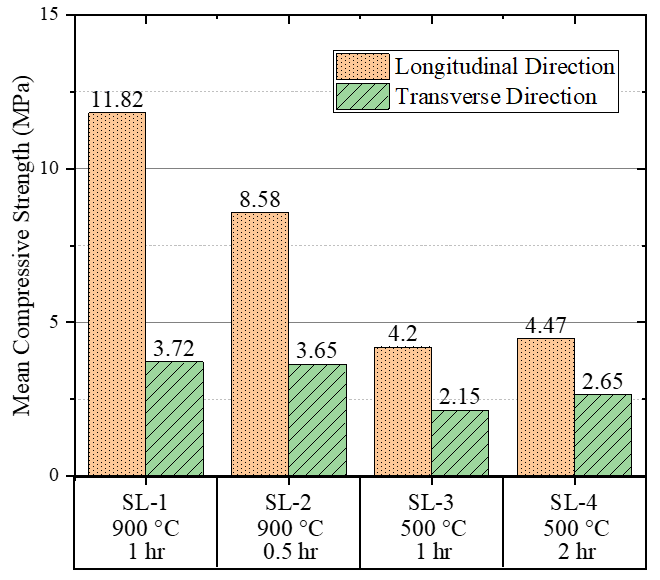
5.2.3. Friction Angle
The friction angle of the sintered product was determined using the consolidated drained triaxial test. Only the material produced in Test SL-1 and SL-2 was sent for the triaxial test because of the large amount of incomplete sintered clay produced observed in Test SL-3 and SL-4. Figure 7 shows the value of the friction angle for Test SL-1 and Test SL-2. It can be concluded that sintered product with a higher percentage of sintered area and strength, Test SL-1, would possess a higher friction angle than that of Test SL-2. The friction angle values obtained were compared with the typical sands available. Typical loose sands’ friction angle is between 27° to 32°; medium dense sands’ is between 32° to 37°; while higher than 37° is those dense sands and very dense sands [16]. It shows that the friction angle of SL-1 (34.7°) falls in the category of medium-dense sands. In contrast, SL-2 can be categorized as loose sands based on the friction angle of 29.4°. This result is promising as this indicates that this sintered product is granular in nature that has high friction angle. The particles can effectively interlock and form a stable ground if used as an infilling material in a land reclamation project – indeed, a “sand-like” behaviour.
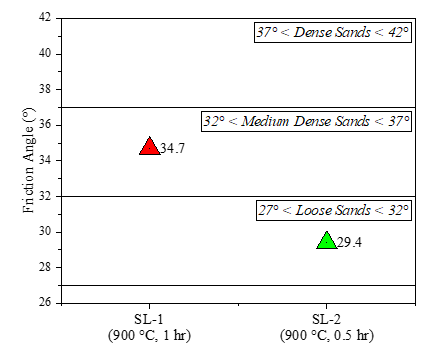
5.2.4. Permeability
A series of constant head permeability tests were conducted for the sintered product from Test SL-1. The permeability value is essential in the land reclamation project, as the infilling material required a high drainage characteristic to consolidate in the fastest time to expedite the construction period. The mean permeability value of the sintered product is determined to be 1.14×10-3 m/s, which falls in the category of gravel-sand mixtures [16]. This high permeability value of the sintered product again proved that this material is truly “sand-like” and is very suitable to be used as an alternative infilling material for future land reclamation projects.
6. Conclusion
The feasibility of transforming the clay-rich excavated soft soil into material that has “sand-like” properties using the sintering technology was studied. The multiple processes were discussed, starting from the original state of the excavated soil until the end product, including filtering, dewatering, granulating, sintering and cooling. A filtering process is needed to exclude the coarse particles. Next, dewatering is a process to reduce the moisture content of the clayey soil for ease of granulation, which turns them into small granules. After granulation, the unfired ‘green’ granules were sent for the high-temperature sintering process. Finally, the sintered granules were left to cool down to room temperature.
The effect of the sintering temperature and the dwelling duration on the quality of the sintered product was examined. A higher sintering temperature (900 °C versus 500 °C) and longer dwelling duration (1 hr versus 0.5 hr; 2 hr versus 1 hr) produced a more complete sintered product based on the sintered area percentage.
The sintered product was tested for its engineering properties and compared with the sand material. The dry loose bulk density of the sintered product is slightly lower than the typical dry loose sand. A more complete sintered product possessed a stronger compressive strength, a higher friction angle, and high permeability. All these proved that the sintered products have very close properties to sandy material; hence, it is considered a “sand-like” material. The “sand-like” material from Test SL-1, with a 900 °C sintering temperature and 1 hr of dwelling duration, can be categorized as medium-dense sands based on its friction angle. The highly permeable characteristic (10-3 m/s) of the sand-like material is similar to the gravel-sand mixtures.
This laboratory-scale study concluded that the excavated soft clayey soil could be recycled, transformed into “sand-like” material, and used as the alternative infilling material for the land reclamation project.
Nevertheless, subsequent research on more cost-efficient sintering schedules and technology using a rotary kiln, where the heating mechanism is different from the static furnace, was also studied. Furthermore, the potential environmental impact due to the sintering process would also be the focus of future works.
Acknowledgements
This research is supported by the National Research Foundation, Singapore, and Ministry of National Development, Singapore, under its Cities of Tomorrow R&D Programme (CoT Award No. COT-V3-2019-2). Any opinions, findings, conclusions, or recommendations expressed in this material are those of the author(s) and do not reflect the views of National Research Foundation, Singapore, and Ministry of National Development, Singapore.
References
[1] S. H. Lim, "Seascape the Landscape of Singapore, Repurposing Land in a Land Scarce Nation," Lect. Notes Civ. Eng., vol. 41, pp. 385-410, 2020, doi: 10.1007/978-981-13-8743-2_22. View Article
[2] S. Gibbs, "Sand Shortage: Myth or Reality?," Mod. Cast., vol. 101, no. 7, pp. 28-31, 2011.
[3] K. Srikrishna, G. Thomas, R. Martinez, M. P. Corral, and J. S. Moya, "Kaolinite-mullite reaction series: a TEM study," J. Mater. Sci., vol. 25, pp. 607-612, 1990.
View Article
[4] S. Lee, Y. J. Kim, and H. S. Moon, "Phase transformation sequence from kaolinite to mullite investigated by an energy-filtering transmission electron microscope," J. Am. Ceram. Soc., vol. 82, no. 10, pp. 2841-2848, 1999, doi: 10.1111/J.1151-2916.1999.TB02165.X.
View Article
[5] R. Pampuch, An Introduction to Ceramics. 2012.
[6] Y. F. Chen, M. C. Wang, and M. H. Hon, "Transformation kinetics for mullite in kaolin-Al2O3 ceramics," J. Mater. Res., vol. 18, no. 6, pp. 1355-1362, 2003, doi: 10.1557/JMR.2003.0186.
View Article
[7] F. Chargui, M. Hamidouche, H. Belhouchet, Y. Jorand, R. Doufnoune, and G. Fantozzi, "Mullite fabrication from natural kaolin and aluminium slag," Bol. la Soc. Esp. Ceram. y Vidr., vol. 57, no. 4, pp. 169-177, 2018, doi: 10.1016/j.bsecv.2018.01.001.
View Article
[8] L. Carbajal, F. Rubio-Marcos, M. A. Bengochea, and J. F. Fernandez, "Properties related phase evolution in porcelain ceramics," J. Eur. Ceram. Soc., vol. 27, no. 13-15, pp. 4065-4069, 2007, doi: 10.1016/j.jeurceramsoc.2007.02.096.
View Article
[9] W. B. Haines, "Studies in the physical properties of soils: I. Mechanical properties concerned in cultivation," J. Agric. Sci., vol. 15, no. 2, pp. 178-200, 1925, doi: 10.1017/S0021859600005669.
View Article
[10] Ajit K. Srivastava, Carroll E. Goering, Roger P. Rohrbach, and Dennis R. Buckmaster, "Chapter 8 Soil Tillage," in Engineering Principles of Agricultural Machines, Second Edition, St. Joseph, MI: American Society of Agricultural and Biological Engineers, 2006, pp. 169-230.
View Article
[11] Y. Yusu and Z. Dechao, "Investigation of the relationship between soil-metal friction and sliding speed," J. Terramechanics, vol. 27, no. 4, pp. 283-290, 1990.
View Article
[12] A. Kooistra, P.; Verhoef, W.; Broere, D.; Ngan-Tillard, and F. Van Tol, "Appraisal of stickiness of natural clays from laboratory tests," Engineering Geology and Infrastructure, pp. 101-113, 1998.
[13] S. N. Monteiro and C. M. F. Vieira, "Solid state sintering of red ceramics at lower temperatures," Ceramics International., vol. 30, no. 3, pp. 381-387, 2004, doi: 10.1016/S0272-8842(03)00120-2.
View Article
[14] P. Ren, T. C. Ling, and K. H. Mo, "Recent advances in artificial aggregate production," Journal of Cleaner Production., vol. 291, 2021, doi: 10.1016/j.jclepro.2020.125215.
View Article
[15] P. Koutník, A. Soukup, P. Bezucha, J. Šafář, P. Hájková, and J. Čmelík, "Comparison of kaolin and kaolinitic claystones as raw materials for preparing metakaolinite-based geopolymers," Ceramics-Silikáty, vol. 63, no. 1, pp. 110-123, 2019, doi: 10.13168/cs.2019.0003.
View Article
[16] B. G. Look, Handbook of Geotechnical Investigation and Design Tables. 2007.
View Article
[17] University of Utah, "Contact Stresses and Deformations," 2006. (accessed Dec. 02, 2021).
View Article
[1] S. H. Lim, "Seascape the Landscape of Singapore, Repurposing Land in a Land Scarce Nation," Lect. Notes Civ. Eng., vol. 41, pp. 385-410, 2020, doi: 10.1007/978-981-13-8743-2_22. View Article
[2] S. Gibbs, "Sand Shortage: Myth or Reality?," Mod. Cast., vol. 101, no. 7, pp. 28-31, 2011.
[3] K. Srikrishna, G. Thomas, R. Martinez, M. P. Corral, and J. S. Moya, "Kaolinite-mullite reaction series: a TEM study," J. Mater. Sci., vol. 25, pp. 607-612, 1990. View Article
[4] S. Lee, Y. J. Kim, and H. S. Moon, "Phase transformation sequence from kaolinite to mullite investigated by an energy-filtering transmission electron microscope," J. Am. Ceram. Soc., vol. 82, no. 10, pp. 2841-2848, 1999, doi: 10.1111/J.1151-2916.1999.TB02165.X. View Article
[5] R. Pampuch, An Introduction to Ceramics. 2012.
[6] Y. F. Chen, M. C. Wang, and M. H. Hon, "Transformation kinetics for mullite in kaolin-Al2O3 ceramics," J. Mater. Res., vol. 18, no. 6, pp. 1355-1362, 2003, doi: 10.1557/JMR.2003.0186. View Article
[7] F. Chargui, M. Hamidouche, H. Belhouchet, Y. Jorand, R. Doufnoune, and G. Fantozzi, "Mullite fabrication from natural kaolin and aluminium slag," Bol. la Soc. Esp. Ceram. y Vidr., vol. 57, no. 4, pp. 169-177, 2018, doi: 10.1016/j.bsecv.2018.01.001. View Article
[8] L. Carbajal, F. Rubio-Marcos, M. A. Bengochea, and J. F. Fernandez, "Properties related phase evolution in porcelain ceramics," J. Eur. Ceram. Soc., vol. 27, no. 13-15, pp. 4065-4069, 2007, doi: 10.1016/j.jeurceramsoc.2007.02.096. View Article
[9] W. B. Haines, "Studies in the physical properties of soils: I. Mechanical properties concerned in cultivation," J. Agric. Sci., vol. 15, no. 2, pp. 178-200, 1925, doi: 10.1017/S0021859600005669. View Article
[10] Ajit K. Srivastava, Carroll E. Goering, Roger P. Rohrbach, and Dennis R. Buckmaster, "Chapter 8 Soil Tillage," in Engineering Principles of Agricultural Machines, Second Edition, St. Joseph, MI: American Society of Agricultural and Biological Engineers, 2006, pp. 169-230. View Article
[11] Y. Yusu and Z. Dechao, "Investigation of the relationship between soil-metal friction and sliding speed," J. Terramechanics, vol. 27, no. 4, pp. 283-290, 1990. View Article
[12] A. Kooistra, P.; Verhoef, W.; Broere, D.; Ngan-Tillard, and F. Van Tol, "Appraisal of stickiness of natural clays from laboratory tests," Engineering Geology and Infrastructure, pp. 101-113, 1998.
[13] S. N. Monteiro and C. M. F. Vieira, "Solid state sintering of red ceramics at lower temperatures," Ceramics International., vol. 30, no. 3, pp. 381-387, 2004, doi: 10.1016/S0272-8842(03)00120-2. View Article
[14] P. Ren, T. C. Ling, and K. H. Mo, "Recent advances in artificial aggregate production," Journal of Cleaner Production., vol. 291, 2021, doi: 10.1016/j.jclepro.2020.125215. View Article
[15] P. Koutník, A. Soukup, P. Bezucha, J. Šafář, P. Hájková, and J. Čmelík, "Comparison of kaolin and kaolinitic claystones as raw materials for preparing metakaolinite-based geopolymers," Ceramics-Silikáty, vol. 63, no. 1, pp. 110-123, 2019, doi: 10.13168/cs.2019.0003. View Article
[16] B. G. Look, Handbook of Geotechnical Investigation and Design Tables. 2007. View Article
[17] University of Utah, "Contact Stresses and Deformations," 2006. (accessed Dec. 02, 2021). View Article