Volume 7 - Year 2024- Pages 84-91
DOI: 10.11159/ijci.2024.009
Comparative Analysis of Pre and Post Mix Methods for Nano Silica Incorporation in Concrete: A Study on Mechanical Property Enhancement
Haard Shukla1, Harshit Dubey2, Devindar Singh3, Abhiraj Jadeja4 , Naimish Bhatt5*
1Pandit Deendayal Energy University
Knowledge Corridor, Raisan, Gandhinagar, Gujarat, India
Haard.scv20@sot.pdpu.ac.in ; Harshit.dcv20@sot.pdpu.ac.in
2Pandit Deendayal Energy University
Knowledge Corridor, Raisan, Gandhinagar, Gujarat, India
Abstract - In the paper, the integration of nanoparticles, particularly nano-silica, has emerged as a transformative force in enhancing material properties. This paper presents a detailed investigation that scrutinizes the impact of nano-silica on cement paste when introduced before or after the mixing process. By taking advantage of the filler effect of nano-sized particles, nano-silica has shown remarkable potential in increasing the compressive strength of cement paste, mortar, and concrete, leading to the development of denser and more resilient products. The results obtained from both pre-mix and post-mix samples reveal a trend of increasing strength up to a certain percentage of nano-silica incorporation, beyond which a slight decrease is observed. The study demonstrates that a nano-silica percentage of 3.5% yields optimal strength, with a subsequent decline in strength at higher incorporation levels. Moreover, the investigation highlights the superiority of post-mix samples in terms of strength gain, with notable improvements observed at 7, 14, and 28 days. The findings underscore the critical importance of the incorporation technique employed, with post-mix techniques showing enhanced strength gains compared to pre-mix methods. By studying the relationship between tiny particles of silica (called nano-silica) and materials used in cement production (called cementitious matrices), research aim to better understand how these materials interact and how they can be used to make stronger and more durable concrete structures, this study paves the way for innovative advancements in construction materials. It offers a compelling case for the strategic utilization of nano-silica to elevate the quality and durability of infrastructure projects.
Keywords: Nano-silica, Cement paste, Compressive strength, Pre-mix technique, post-mix technique, Concrete properties, Nanoparticles, Material composition Construction industry Infrastructure durability
© Copyright 2024 Authors - This is an Open Access article published under the Creative Commons Attribution License terms. Unrestricted use, distribution, and reproduction in any medium are permitted, provided the original work is properly cited.
Date Received: 2023-10-11
Date Revised: 2024-05-29
Date Accepted: 2024-06-04
Date Published: 2024-07-15
1. Introduction
Over the recent years, the utilization of nanoparticles has significantly contributed to the improvement of cement and concrete properties. Among the nanoparticles that have been implemented in cement research, nano-silica stands out as the most widely used, building upon the successful application of silica fume in cement products. The introduction of nano-silica has shown remarkable potential in enhancing the compressive strength of cement paste, mortar, and concrete by using the filler effect of nano-size particles, resulting in denser products. Various research scholars have conducted extensive studies on the complex challenges associated with nano-silica. However, there are only a few reports on the mixing of cement-based materials with nano-silica, making it crucial to examine the effect of adding nano-silica either before or after mixing cement paste. In this paper, we present the results of a comprehensive study that investigates the effect of nano-silica on cement paste when added before or after mixing.
2. Literature Review
[1] explored using nano-waste ceramic (NWC) and nano silica (NS) to enhance Portland cement concrete performance. The study evaluated NS and NWC replacement levels, including a hybrid mix of both, which could revolutionize the construction industry. The results showed that pre-soaking recycled coarse aggregates in NS solution improved the recycled aggregate concrete's compressive strength by 5% compared to direct NS mixing. The volume of large capillary pores in the matrix adjacent to RCA is increased when NS is directly mixed but reduced when RCA is pre-soaked in NS solution. The microstructure of the matrix adjacent to pre-soaked RCA is more compact than that of the direct mixing method. The findings of this study provide valuable insights into the use of demolition waste to create sustainable building materials . Using NS and NWC in concrete has the potential to significantly reduce the environmental impact of the construction industry.[2] explores the use of demolition waste to create sustainable building materials, focusing on enhancing concrete production using nano-waste ceramic (NWC) and nano silica (NS). The research shows that adding up to 6% NWC content in concrete improves its strength and outperforms traditional methods. The study also found that even when using up to 10% NWC content, the strength of the concrete is still impressive. The utilization of NS and NWC in concrete improves its internal structure, decreases porosity, and enhances the density of the cement matrix. The study highlights the potential of substituting cement with NS and NWC, demonstrating their positive impact on the mechanical properties of the concrete. [3] (nS) can enhance ultra-high-performance concrete (UHPC) by improving its strength, flowability, and transport properties. It can also reduce capillary pores, resulting in a finer pore structure, and improve interfacial transition zone, leading to increased durability. Replacing 3 wt.% of cement with nS can improve concrete durability, and it can resist chloride penetration and water permeability. The transport properties of concrete are influenced by its pore structure, including total porosity, pore size, pore connectivity, and pore saturation. Adding nS to UHPC has a significant impact on its overall performance. [4] Investigated the correlation between the fractal dimension of concrete and its pore structure, strength, and permeability when incorporating silica fume. Various tests were conducted to evaluate the mechanical properties and microstructure, and the results showed that silica fume improves the homogenization and refinement of the pore structure, while meso and coarse porosities have opposing effects on strength. [6] Investigated the effects of various nanoparticles on high-performance concrete (HPC). The study found that the optimal improvement in HPC could be achieved by replacing 4% of cementitious materials with nano fly ash and nano silica fume. These nanoparticles demonstrated a significant enhancement in the mechanical properties of HPC. Moreover, the study discovered that nano clay and TiO2 nanoparticles had an impact on the mechanical properties and microstructure of cement mortars. Finally, the study identified superplasticizer as a useful component in producing high-quality concrete mix with high strength.
3. Materials and Method
Effective selection of materials along with proper mixing and incorporation of nano materials helps in attaining the desired results. Moreover, the obtained result is widely varied based on the incorporation technique employed. Different materials were used in the current study to evaluate the effect of pre mixing and post mixing of nano silica in concrete mix. In the present study the Ordinary Portland cement (OPC 53) produced by Ultratech Pvt. Ltd. confirming to international quality standards ISO 9001 was used. Graded fine (sieve no. 4 = 4.75 mm) and coarse aggregate were purchased from Sand Sure Enterprise, Gandhinagar, India. The silicon dioxide nano material (SiO2) was supplied by Fibrezone India. Different methods of incorporation of nano silica involved:
3.1 Method of Incorporation Pre mixing
The pre-mixing or dry mixing method is a widely-used technique in the construction industry for preparing concrete. This method involves mixing the materials in a dry state before adding water and superplasticizers. The dry mixing process allows for better control over the mixing process and helps achieve a consistent mix. Additionally, it reduces the amount of water required to make the concrete, leading to a stronger and more durable final product. The use of superplasticizers further enhances the workability of the concrete. The figure provided below illustrates the dry mixing process employed in the present study, providing a visual representation of the various stages involved.
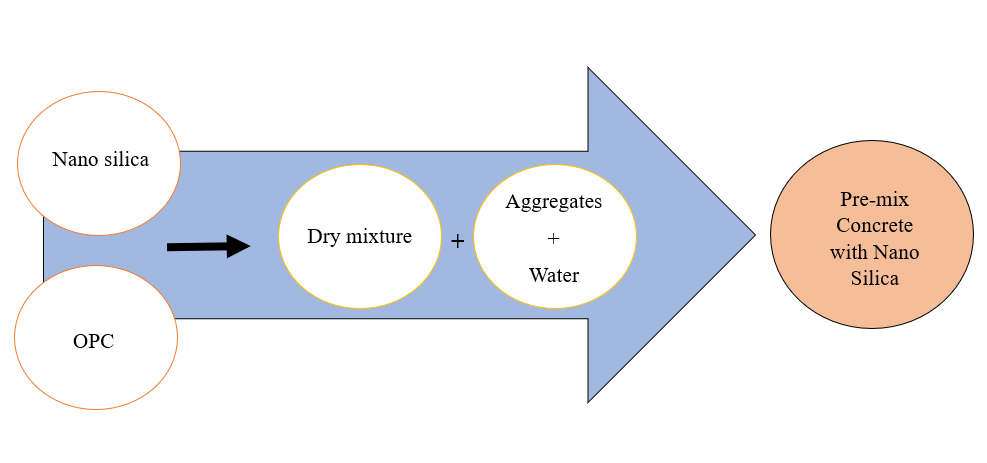
[4] had employed the premixing technique for incorporation of supplementary material to cement. This method involves firstly mixing the required amount of nano silica with weighed cement in a dry state. Next this dry mixture is poured in mixer with aggregates in dry states and is mixed for 4-5 minutes, after that a required amount of water is added to obtain the concrete mix. The sample prepared are depicted in the table below.
Table 1: Pre mix specimens
Sample no. |
Symbol |
Nano-silica (%) by wt. |
1 |
CDS1 |
0 % |
2 |
CDS2 |
1% |
3 |
CDS3 |
2% |
4 |
CDS4 |
2.5% |
5 |
CDS5 |
3% |
6 |
CDS6 |
3.5% |
7 |
CDS7 |
4% |
The prepared mixture of concrete was the poured in the molds. However, to ease the comparison of the samples similar number of cubes of size 15 x 15 x 15 cm were prepared.
Post mixing
Post mixing or the wet mixing method is a technique used widely by for material incorporations. In this methos the nano material is not directly used, rather it is initially mixed with a liquid (water or superplasticizer) to prepare a paste. This prepared paste is then used in concrete sample for incorporation of nano materials. The post mixing method employed is depicted in below figure.
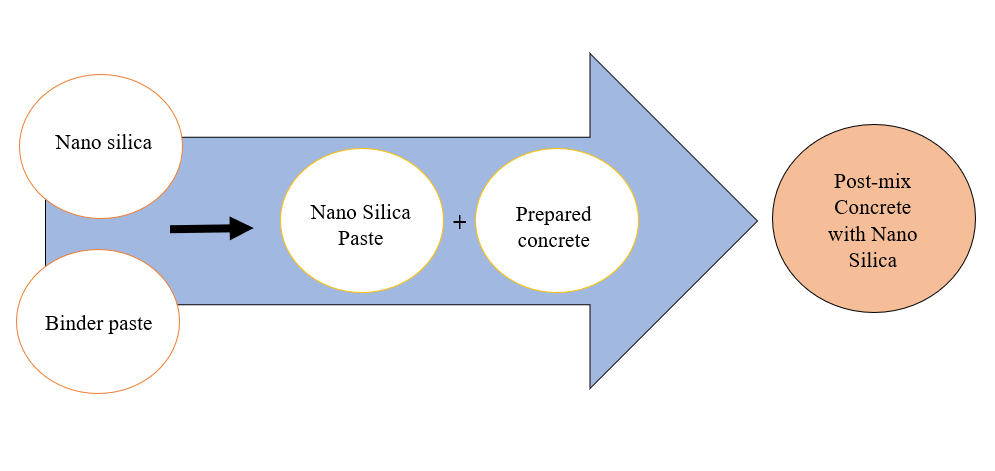
Different researchers have used the post mixing technique to incorporate nano materials in concrete. [2], [3]. This method follows a certain step including firstly making a paste of nano material with water, the adding this prepared paste into the concrete mix. Thus, resulting in concrete with incorporated nano materials. The samples prepared in post mix technique is tabulated below.
Table 2: Post mix specimens
Sample no. |
Symbol |
Nano-silica (%) by wt. |
1 |
CWS1 |
0 % |
2 |
CWS2 |
1% |
3 |
CWS3 |
2% |
4 |
CWS4 |
2.5% |
5 |
CWS5 |
3% |
6 |
CWS6 |
3.5% |
7 |
CWS7 |
4% |
Prepared concrete from the pre and post mix method with different nano silica percentage of 0%, 1%, 2%, 2.5%, 3%, 3.5%, 4% is poured in mold of size 15 x 15 x 15 cm and was cured using conventional methos. The material composition of the concrete mix show in the table below.
Table 3: Material composition in concrete mix
MATERIALS |
OPC |
Fine aggregate |
Coarse aggregate |
Water |
WEIGHT (g) |
17045 |
32000 |
63500 |
7500 |
The prepared cubes were tested for 7days, 14 days and 28 days under the compression testing machine. The average reading of three cubes for one sample were noted as mean compressive strength of the cube. The characteristic compressive strength was attained subtracting the standard deviation from the mean value.
4. Result and Discussion
The results obtained in both pre-mix and post-mix samples shown the trend of increasing strength to a fixed percentage of nano silica. After a certain percentage the strength shown a little increase and then started to decrease. The obtained result shows the increase in strength to a percentage of 3.5% of nano silica incorporated in concrete, the 4% incorporation showed a trend of a minute decrease in both techniques. The individual result obtained is presented below.
4.1 Pre-Mix Method
Figure 3 provides a comprehensive overview of the compressive strength results obtained from the pre-mix samples across the 7, 14, and 28-day testing periods. Among these samples, CDS6 emerged as the standout performer, showcasing the highest strength with a nano silica percentage of 3.5%. However, a slight reduction in strength was observed in sample CDS7, where 4% nano silica replaced a portion of the concrete mass. Notably, when compared to their post-mix counterparts, these pre-mix samples consistently exhibited lower strength levels.
Delving deeper into the strength increments relative to the reference sample CDS1, which lacked any nano silica incorporation, reveals intriguing insights. Samples CDS2 through CDS7 demonstrated incremental strength gains of 1.03%, 3.25%, 4.81%, 8.42%, 11.92%, and 8.71% respectively. Of particular significance is the notable peak observed at 3.5% nano silica incorporation, where a substantial 11.92% increase in strength was achieved at the 28-day mark. These findings underscore the nuanced relationship between nano silica content and concrete strength, suggesting an optimal range for maximum performance enhancement over various durations.
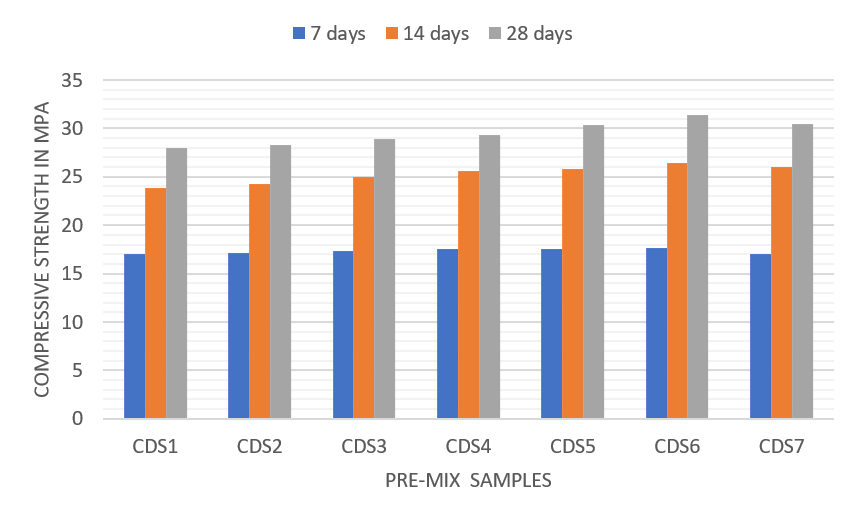
4.2 Post-Mix Method
Figure 4 provides a visual representation of the compressive strength results for the post-mix samples over the duration of 7, 14, and 28 days. Among these samples, CWS6 demonstrated the highest strength, attributed to its nano silica percentage of 3.5%. However, a slight decrease in strength was observed in sample CWS7, containing 4% nano silica replacing a portion of the concrete mass. Despite this minor reduction, the post-mix samples showcased superior strength compared to their pre-mix counterparts.
Notably, the post-mix samples exhibited an increase in strength gain, with percentages of 12.85, 13.83, and 16.02 for 7, 14, and 28 days respectively, aligning closely with results reported in previous studies [6]. This indicates a promising consistency in strength development over time, affirming the efficacy of the post-mix approach in enhancing concrete performance.
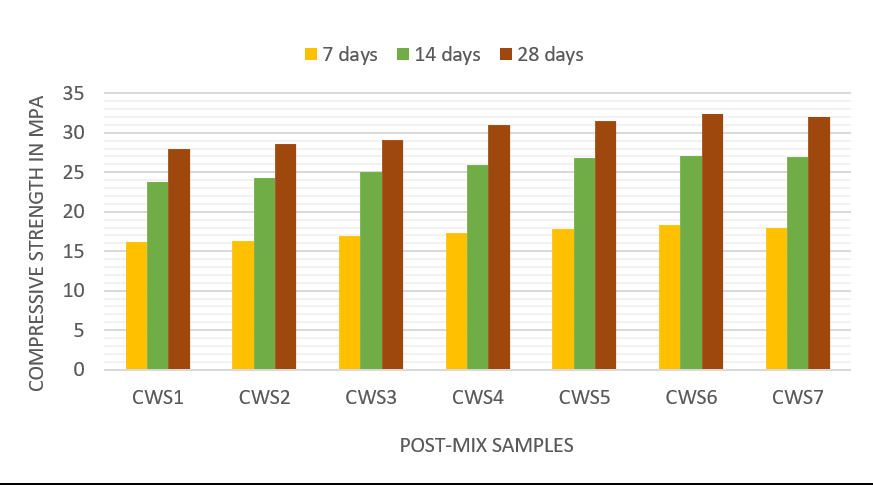
Figure 5 illustrates the individual comparison of strength between post and pre-mix samples over 7, 14, and 28 days. Notably, the pre-mix samples consistently exhibited decreased strength across all three test periods, prompting examination into potential causes for this trend. One contributing factor could be the generation of deficiencies within the mixture, leading to the formation of weak zones [2]. These deficiencies may arise from the non-uniform distribution of nano silica within the pre-mix samples. The heightened surface area of nano silica tends to escalate water demand, consequently diminishing the workability of the mixture, a phenomenon particularly prominent in pre-mix samples
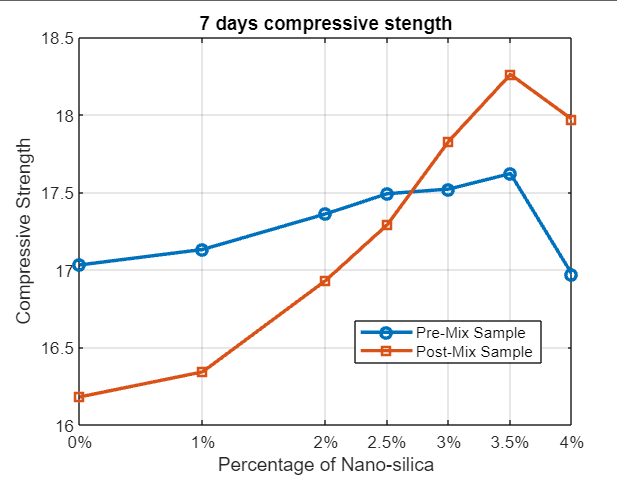
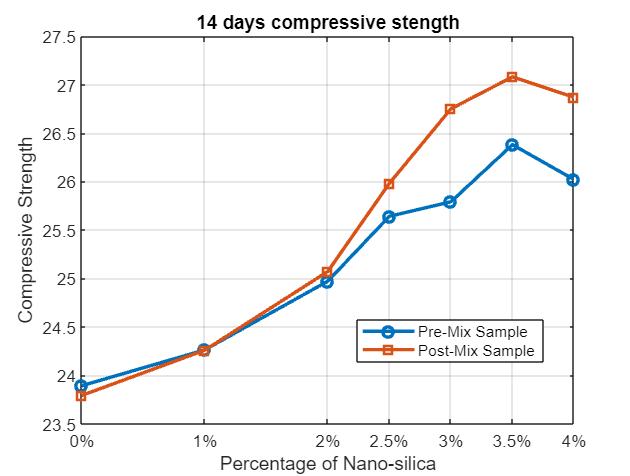
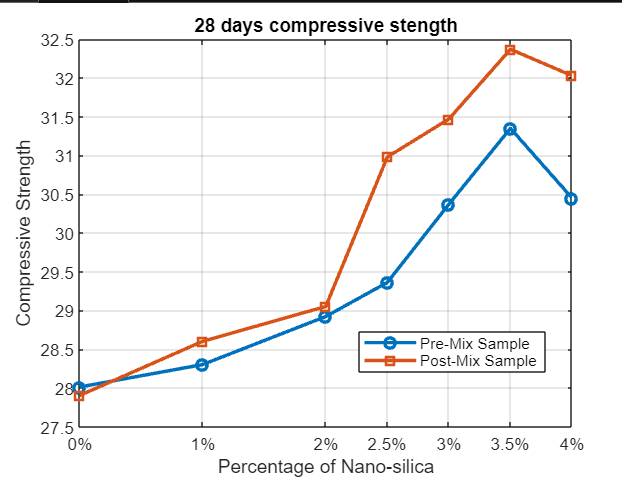
The decline in strength observed in samples CDS7 and CWS7, containing 4% nano silica, can be attributed to the escalating presence of nano materials. As the proportion of nanoparticles increases, they begin to disrupt the hydration process [5]. These nanoparticles possess an elevated affinity for liberated lime, exceeding the required stoichiometry and leading to the leaching of unbound silica. Consequently, this unbound silica disperses within the cementitious matrix, compromising the overall strength of the mixture without contributing to its reinforcement.
On the other hand, the initial spike in strength observed in pre-mix samples at 7 days can be traced back to the inherent strength of the initial cube samples, which naturally boasted higher values. Moreover, the observed strength increment associated with the initial percentage, particularly noticeable in samples CDS2 and CWS2 for pre-mix and post-mix, respectively, was less pronounced during the initial days. This trend underscores the complex dynamics at play in concrete strength development, suggesting that factors beyond mere nano silica content influence the performance of concrete mixtures over time.
5. Future Scope of Work
The following study is based on incorporation of nano silica and results obtain by varying the method employed . The Future scope of work can include the following aspects :
- To ensure optimal mix analysis when altering the silica percentage in cement, adjusting the water-cement ratio is imperative. This adjustment compensates for any deficiencies arising from increased water demand in pre-mix sample. A step in similar direction can be taken to accommodate the varying the water cement ratio .
- Silica, functioning as a supplementary material, can be optimized in concrete formation through the incorporation of other additives. Additionally, we should focus on the choice of materials utilized in the mixture which can be instrumental in enhancing other properties such as tensile strength.
6. Conclusion
The following study evaluate the comparative results of pre-mix and post-mix concrete sample incorporated with nano silica. Based on results obtained following conclusions can be drawn:
- The present study aimed to investigate the influence of incorporating nano silica on the strength of pre-mix and post-mix concrete samples. The study revealed that the addition of 3.5% nano silica to both pre-mix and post-mix samples resulted in a significant increase in strength. However, it was observed that further addition of nano silica led to a decrease in strength for both types of samples.
- In addition, the study highlighted that non-uniform distribution of nano silica in pre-mix samples resulted in weak zones, thereby leading to lower strength as compared to post-mix samples. Furthermore, the researchers found that the strength increment of post-mix samples was higher than that of pre-mix samples. Specifically, post-mix samples showed a strength increase of 12.85%, 13.83%, and 16.02% for 7, 14, and 28 days, respectively. In contrast, pre-mix samples had a narrow range of strength increase, ranging from 3.47% to 11.93% for the same period.
- Based on the findings, it is recommended to use the post-mix method for incorporating nano materials in concrete mixtures to achieve the desired strength. The study provides meaningful insights into the effects of nano silica on the strength of concrete, which can help improve the quality of concrete structures and ensure their durability.
References
[1]. Shaikh, F., Chavda, V., Minhaj, N. & Arel, H.S., 2018. Effect of mixing methods of nano silica on properties of recycled aggregate concrete. Structural Concrete, 19(2), pp.387-399.
View Article
[2]. Tawfik, T.A., Abd EL-Aziz, M.A., Abd El-Aleem, S. & Serag Faried, A., 2018. Influence of nanoparticles on mechanical and non-destructive properties of high-performance concrete. Journal of the Chinese Advanced Materials Society, 6(4), pp.409-433.
View Article
[3]. Ghafari, E., Costa, H., Júlio, E., Portugal, A. & Durães, L., 2014. The effect of nanosilica addition on flowability, strength and transport properties of ultra high performance concrete. Materials and Design, 59, pp.1-9.
View Article
[4]. Lü, Q., Qiu, Q., Zheng, J., Wang, J. & Zeng, Q., 2019. Fractal dimension of concrete incorporating silica fume and its correlations to pore structure, strength and permeability. Construction and Building Materials, 228.
View Article
[5]. Esmaeili, J. & Andalibi, K., 2012. Investigation of the effects of nano-silica on the properties of concrete in comparison with micro-silica. Scientific Information Database (SID).
[6]. Tawfik, T.A., Aly Metwally, K., EL-Beshlawy, S.A., Al Saffar, D.M., Tayeh, B.A. & Soltan Hassan, H., 2021. Exploitation of the nanowaste ceramic incorporated with nano silica to improve concrete properties. Journal of King Saud University - Engineering Sciences, 33(8), pp.581-588.
View Article
[7]. Rebentrost, M. & G.W., Experience and applications of Ultra-high Performance concrete in Asia in Second International Symposium on Ultra High Performance Concrete. Kassel, Germany 2008.
[8]. Fehling, E. & Stürwald, M.S., (eds.) The Third International Symposium on Ultra High Performance Concrete and Nanotechnology for High Performance Construction Materials. Kassel, Germany: Kassel University Press, March 2012.
[9]. Graybeal, B.A., 2006. Material property characterization of ultra-high performance concrete. Federal Highway Administration Report No FHWA-HRT-06-103. McLean, Virginia, USA, August.
[10]. Richard, P. & Cheyrezy, M., 1995. Composition of reactive powder concrete. Cem Concr Res, 25, pp.1501-1511.
View Article
[11]. Li, H., Xiao, H., Yuan, J. & Jinping, O., 2004. Microstructure of cement mortar with nanoparticles. Compos B: Eng, 35, pp.185-189.
View Article
[12]. Collepardi, M., Collepardi, S., Skarp, U. & Troli, R., 2004. Optimization of silica fume, fly ash and amorphous nano-silica in superplasticized high-performance concretes. ACI Mater J, pp.495-506.
[13]. Li, G., 2004. Properties of high-volume fly ash concrete incorporating nano-SiO2. Cem Concr Res, 34, pp.1043-1049.
View Article
[14]. Aly, M., Hashmi, M.S.J., Olabi, A.G., Messeiry, M., Abadir, E.F. & Hussain, A.I., 2012. Effect of colloidal nano-silica on the mechanical and physical behaviour of waste-glass cement mortar. Mater Des, 33, pp.127-135.
View Article
[15]. He, X. & Shi, X., 2008. Chloride Permeability and microstructure of portland cement mortars incorporating nanomaterials. J Transport Res Board, pp.13-21.
View Article
[16]. Ji, T., 2005. Preliminary study on the water permeability and microstructure of concrete incorporating nano-SiO2. Cem Concr Res, 35, pp.1943-1947.
View Article
[17]. Sobolev, K., Flores, I., Hermosillo, R. & Torres-Martínez, L.M., 2008. Nanomaterials and nanotechnology for high-performance Cem Compos. ACI Mater J, 254, pp.93-120.
[18]. Qing, Y., Zenan, Z., Deyu, K. & Rongshen, C., 2007. Influence of nano-SiO2 addition on properties of hardened cement paste as compared with silica fume. Constr Build Mater, 21, pp.539-545.
View Article
[19]. Beedle, S., Groves, G.W. & Rodger, S.A., 1989. The effect of fine pozzolanic and other particles on the hydration of C3S. Adv Cem Res, 2, pp.3-8.
View Article
[20]. Lothenbach, B., Saout, L.G., Haha, M.B., Figi, R. & Wieland, E., 2012. Hydration of a low-alkali CEM III/B-SiO2 cement (LAC). Cem Concr Res, 42, pp.410-423.
View Article
[21]. Jalal, M., Mansouri, E., Sharifipour, M. & Pouladkhan, A., 2012. Mechanical, rheological, durability and microstructural properties of high performance self-compacting concrete containing SiO2 micro and nanoparticles. Mater Des, 34, pp.389-400.
View Article
[22]. Beigi, M.H., Berenjian, J., Omran, O.L., Nik, A.S. & Nikbin, I.M., 2013. An experimental survey on combined effects of fibers and nanosilica on the mechanical, rheological, and durability properties of self-compacting concrete. Mater Des, 50, pp.1019-1029.
View Article
[23]. Ghafari, E., Bandarabadi, M., Costa, H. & Júlio, E., 2012. Design of UHPC using artificial neural networks. In: 10th International symposium on brittle matrix composites. Warsaw, Poland.
View Article
[24]. Ghafari, E., Costa, H. & Júlio, E., 2012. Design of UHPFRC with Enhanced Ductility. 8th Rilem conference on fiber reinforced concrete. Guimares, Portugal.
[25]. Ghafari, E., Costa, H., Júlio, E., Portugal, A. & Durães, L., 2012. Optimization of UHPC by adding nanomaterials. In: 3rd international conference on ultra high performance concrete. Kassel, Germany, pp.71-79.
[26]. Kendrick, D.A., Parsonage, J.R. & Vazifdar, R., 1998. Interaction of alkali and alkali earth metal hydroxides with microsilica. Cem Concr Res, 28, pp.1537-1544.
View Article
[27]. CEN EN 196-1, 2005. Methods of testing cement-Part 1: Determination of strength, European Committee for standardization.
[28]. Bentz, D.P., Clifton, J.R., Ferraris, C.F. & Garboczi, E.J., 1999. Transport properties and durability of concrete. Maryland: National Institute of Standard and Technology.
View Article
[29]. Garboczi, E.J., 1990. Permeability, diffusivity, and microstructural parameters: a critical review. Cem Concr Res, 20, pp.591-601.
View Article
[30]. Sabir, B.B., Wild, S. & Farrell, M.O., 1998. A water sorptivity test for mortar and concrete. Mater Struct, 31, pp.568-574.
View Article
[31]. Neimark, A.V., 1990. Determination of fractal dimension of surface pores of porous solids by fluid adsorption. In: K.R. Hall, D.H. Kuo and H.M. Seller, eds. Fundamentals of adsorption. Boston: Springer, pp.231-24
[32]. IS 10262: 2019. Concrete mix proportioning - guidelines. 5th revision, Bureau of Indian Standards, New Delhi, India.
[33]. IS 9103: 1999. Specification for concrete admixtures. 4th revision, Bureau of Indian Standards, New Delhi, India.
[34]. IS 456: 2000. Plain and reinforced concrete - code of practice. 4th revision, Bureau of Indian Standards, New Delhi, India.
[35]. ASTM C 494/C 494M-13. Standard Specification for Chemical Admixtures for Concrete. ASTM International, West Conshohocken, PA.
[36]. ASTM C 618-19. Standard Specification for Coal Fly Ash and Raw or Calcined Natural Pozzolan for Use in Concrete. ASTM International, West Conshohocken, PA.
[37]. ASTM C 150/C 150M-20. Standard Specification for Portland Cement. ASTM International, West Conshohocken, PA.
[38]. ASTM C 33/C 33M-18. Standard Specification for Concrete Aggregates. ASTM International, West Conshohocken, PA.
[1]. Shaikh, F., Chavda, V., Minhaj, N. & Arel, H.S., 2018. Effect of mixing methods of nano silica on properties of recycled aggregate concrete. Structural Concrete, 19(2), pp.387-399. View Article
[2]. Tawfik, T.A., Abd EL-Aziz, M.A., Abd El-Aleem, S. & Serag Faried, A., 2018. Influence of nanoparticles on mechanical and non-destructive properties of high-performance concrete. Journal of the Chinese Advanced Materials Society, 6(4), pp.409-433. View Article
[3]. Ghafari, E., Costa, H., Júlio, E., Portugal, A. & Durães, L., 2014. The effect of nanosilica addition on flowability, strength and transport properties of ultra high performance concrete. Materials and Design, 59, pp.1-9. View Article
[4]. Lü, Q., Qiu, Q., Zheng, J., Wang, J. & Zeng, Q., 2019. Fractal dimension of concrete incorporating silica fume and its correlations to pore structure, strength and permeability. Construction and Building Materials, 228. View Article
[5]. Esmaeili, J. & Andalibi, K., 2012. Investigation of the effects of nano-silica on the properties of concrete in comparison with micro-silica. Scientific Information Database (SID).
[6]. Tawfik, T.A., Aly Metwally, K., EL-Beshlawy, S.A., Al Saffar, D.M., Tayeh, B.A. & Soltan Hassan, H., 2021. Exploitation of the nanowaste ceramic incorporated with nano silica to improve concrete properties. Journal of King Saud University - Engineering Sciences, 33(8), pp.581-588. View Article
[7]. Rebentrost, M. & G.W., Experience and applications of Ultra-high Performance concrete in Asia in Second International Symposium on Ultra High Performance Concrete. Kassel, Germany 2008.
[8]. Fehling, E. & Stürwald, M.S., (eds.) The Third International Symposium on Ultra High Performance Concrete and Nanotechnology for High Performance Construction Materials. Kassel, Germany: Kassel University Press, March 2012.
[9]. Graybeal, B.A., 2006. Material property characterization of ultra-high performance concrete. Federal Highway Administration Report No FHWA-HRT-06-103. McLean, Virginia, USA, August.
[10]. Richard, P. & Cheyrezy, M., 1995. Composition of reactive powder concrete. Cem Concr Res, 25, pp.1501-1511. View Article
[11]. Li, H., Xiao, H., Yuan, J. & Jinping, O., 2004. Microstructure of cement mortar with nanoparticles. Compos B: Eng, 35, pp.185-189. View Article
[12]. Collepardi, M., Collepardi, S., Skarp, U. & Troli, R., 2004. Optimization of silica fume, fly ash and amorphous nano-silica in superplasticized high-performance concretes. ACI Mater J, pp.495-506.
[13]. Li, G., 2004. Properties of high-volume fly ash concrete incorporating nano-SiO2. Cem Concr Res, 34, pp.1043-1049. View Article
[14]. Aly, M., Hashmi, M.S.J., Olabi, A.G., Messeiry, M., Abadir, E.F. & Hussain, A.I., 2012. Effect of colloidal nano-silica on the mechanical and physical behaviour of waste-glass cement mortar. Mater Des, 33, pp.127-135. View Article
[15]. He, X. & Shi, X., 2008. Chloride Permeability and microstructure of portland cement mortars incorporating nanomaterials. J Transport Res Board, pp.13-21. View Article
[16]. Ji, T., 2005. Preliminary study on the water permeability and microstructure of concrete incorporating nano-SiO2. Cem Concr Res, 35, pp.1943-1947. View Article
[17]. Sobolev, K., Flores, I., Hermosillo, R. & Torres-Martínez, L.M., 2008. Nanomaterials and nanotechnology for high-performance Cem Compos. ACI Mater J, 254, pp.93-120.
[18]. Qing, Y., Zenan, Z., Deyu, K. & Rongshen, C., 2007. Influence of nano-SiO2 addition on properties of hardened cement paste as compared with silica fume. Constr Build Mater, 21, pp.539-545. View Article
[19]. Beedle, S., Groves, G.W. & Rodger, S.A., 1989. The effect of fine pozzolanic and other particles on the hydration of C3S. Adv Cem Res, 2, pp.3-8. View Article
[20]. Lothenbach, B., Saout, L.G., Haha, M.B., Figi, R. & Wieland, E., 2012. Hydration of a low-alkali CEM III/B-SiO2 cement (LAC). Cem Concr Res, 42, pp.410-423. View Article
[21]. Jalal, M., Mansouri, E., Sharifipour, M. & Pouladkhan, A., 2012. Mechanical, rheological, durability and microstructural properties of high performance self-compacting concrete containing SiO2 micro and nanoparticles. Mater Des, 34, pp.389-400. View Article
[22]. Beigi, M.H., Berenjian, J., Omran, O.L., Nik, A.S. & Nikbin, I.M., 2013. An experimental survey on combined effects of fibers and nanosilica on the mechanical, rheological, and durability properties of self-compacting concrete. Mater Des, 50, pp.1019-1029. View Article
[23]. Ghafari, E., Bandarabadi, M., Costa, H. & Júlio, E., 2012. Design of UHPC using artificial neural networks. In: 10th International symposium on brittle matrix composites. Warsaw, Poland. View Article
[24]. Ghafari, E., Costa, H. & Júlio, E., 2012. Design of UHPFRC with Enhanced Ductility. 8th Rilem conference on fiber reinforced concrete. Guimares, Portugal.
[25]. Ghafari, E., Costa, H., Júlio, E., Portugal, A. & Durães, L., 2012. Optimization of UHPC by adding nanomaterials. In: 3rd international conference on ultra high performance concrete. Kassel, Germany, pp.71-79.
[26]. Kendrick, D.A., Parsonage, J.R. & Vazifdar, R., 1998. Interaction of alkali and alkali earth metal hydroxides with microsilica. Cem Concr Res, 28, pp.1537-1544. View Article
[27]. CEN EN 196-1, 2005. Methods of testing cement-Part 1: Determination of strength, European Committee for standardization.
[28]. Bentz, D.P., Clifton, J.R., Ferraris, C.F. & Garboczi, E.J., 1999. Transport properties and durability of concrete. Maryland: National Institute of Standard and Technology. View Article
[29]. Garboczi, E.J., 1990. Permeability, diffusivity, and microstructural parameters: a critical review. Cem Concr Res, 20, pp.591-601. View Article
[30]. Sabir, B.B., Wild, S. & Farrell, M.O., 1998. A water sorptivity test for mortar and concrete. Mater Struct, 31, pp.568-574. View Article
[31]. Neimark, A.V., 1990. Determination of fractal dimension of surface pores of porous solids by fluid adsorption. In: K.R. Hall, D.H. Kuo and H.M. Seller, eds. Fundamentals of adsorption. Boston: Springer, pp.231-24
[32]. IS 10262: 2019. Concrete mix proportioning - guidelines. 5th revision, Bureau of Indian Standards, New Delhi, India.
[33]. IS 9103: 1999. Specification for concrete admixtures. 4th revision, Bureau of Indian Standards, New Delhi, India.
[34]. IS 456: 2000. Plain and reinforced concrete - code of practice. 4th revision, Bureau of Indian Standards, New Delhi, India.
[35]. ASTM C 494/C 494M-13. Standard Specification for Chemical Admixtures for Concrete. ASTM International, West Conshohocken, PA.
[36]. ASTM C 618-19. Standard Specification for Coal Fly Ash and Raw or Calcined Natural Pozzolan for Use in Concrete. ASTM International, West Conshohocken, PA.
[37]. ASTM C 150/C 150M-20. Standard Specification for Portland Cement. ASTM International, West Conshohocken, PA.
[38]. ASTM C 33/C 33M-18. Standard Specification for Concrete Aggregates. ASTM International, West Conshohocken, PA.