Volume 7 - Year 2024- Pages 126-137
DOI: 10.11159/ijci.2024.013
Characteristics and performance of Geopolymer Concrete Incorporating Recycled Concrete Aggregates and Glass Fibers
Mohammed Abughali1, Hilal EL-Hassan1, Tamer El-Maaddawy1, Mouaz Chkhachirou 1
1United Arab Emirates University, Department of Civil and Environmental Engineering
P.O.Box 15551, Al-Ain, United Arab Emirates
202170069@uaeu.ac.ae; helhassan@uaeu.ac.ae; tamer.maaddawy@uaeu.ac.ae; 202170150@uaeu.ac.ae
Abstract - The purpose of this study is to investigate the workability and the compressive strength of geopolymer concrete incorporating recycled concrete aggregates (RCA) and glass fibers (GF) with varying aspect ratios. The binder material was a combination of class F fly ash and ground granulated blast furnace slag at a ratio of 1:3. Actually, dune sand served as fine aggregates. The coarse aggregates used were either natural aggregates or RCA. Unlike hydrated cement, geopolymers are activated in an alkaline solution. Therefore, a combination of sodium silicate and sodium hydroxide initiated the proper geopolymerization process. In fact, this particular solution creates a conducive environment for the exothermic chemical reaction to produce the newly formed concrete mixtures. Through this study, the impact of multiple parameters such as, the replacement percentage of natural aggregates with RCA, binder content, amount of additional water (added only to the alkaline activator solution), particle size distribution of RCA, and volume fraction of glass fibers were studied in detail. Experimental results revealed that the RCA-geopolymer concrete mixture exhibited a reduction in compressive strength by approximately 25%, compared to its NA-based counterpart geopolymer concrete, while the workability was unaffected. Meanwhile, increasing the binder content from 300 to 450 kg/m3 in RCA-based geopolymer concrete led to an improvement of 56 and 7% in the 7-day compressive strength and workability, respectively. Adding up to 100 kg/m3 of water increased the workability up to 240 mm while decreasing the compressive strength by almost 10%, compared to its counterpart concrete made with 50 kg/m3 of water. Moreover, when RCA was sieved to exclude particles smaller than 4.75 mm and larger than 19 mm, the slump increased to 210 mm. This process also led to a 29% increase in 1-day compressive strength and a 35% increase in 7-day compressive strength. The addition of glass fibers had a significant negative impact on the workability of geopolymer concrete as it led to a decrease in the workability by 2 and 9% when the volume fraction was 1 and 2%, respectively. The experimental findings emphasize the potential of using RCA as a substitute for natural aggregates in slag-fly ash blended geopolymer concrete reinforced with glass fibers, without compromising performance.
Keywords: Geopolymer concrete, Glass fibers, Recycled concrete aggregates, Workability, Compressive strength.
© Copyright 2024 Authors - This is an Open Access article published under the Creative Commons Attribution License terms. Unrestricted use, distribution, and reproduction in any medium are permitted, provided the original work is properly cited.
Date Received: 2024-02-06
Date Revised: 2024-07-12
Date Accepted: 2024-07-30
Date Published: 2024-08-13
1. Introduction
Concrete is among the most extensively used construction materials worldwide, primarily produced with ordinary Portland cement (OPC). Recent decades have seen a notable increase in concrete demand due to economic development and population growth. However, OPC production has significant environmental drawbacks. It is an energy-intensive process that consumes several natural resources and emits substantial greenhouse gases. Unfortunately, the production of Portland cement is considered an environmentally harmful process, as it is mainly responsible for 7% of global carbon dioxide emissions. Specifically, around 1 ton of carbon dioxide is usually emitted into the atmosphere, and almost 1.5 tons of natural resources are required to produce only 1 ton of cement. Due to its severe and significant environmental influences, there is a high demand for replacing the Portland cement with more eco-friendly binder material [1].
After several studies and experimental work, supplementary cementitious materials (SCMs) have been found to be the most promising alternative products to traditional cement. These materials showed superior properties that meet the aspirations and expectations required for being utilized in various industrial applications. Furthermore, these materials are typically rich in silica, alumina and/ or calcium, such as class F fly ash and slag. In fact, to initiate the geopolymerization process, these binder materials must be mixed properly with alkaline solution to produce newly formed alkali-activated geopolymer concrete. The geopolymerization process typically begins immediately when the aluminosilicate binder source and alkaline solution interact within the concrete mixture. This exothermic reaction results in the formation of a sophisticated 3-D polymeric chain structure. These structures can be categorized into three types based on the dominant element. The strongest structure for geopolymer concrete is known as the Poly (sialate-disclose) structure, where silica is the dominant element. [2-4]. One of the substantial environmental benefits of fly ash geopolymer concrete is its energy efficiency. The production process required about 60% less energy than ordinary Portland cement, while also contributing to an 80-90% reduction in CO2 emissions [5].
Natural aggregates (NA), the second major component of concrete, also creates environmental challenges due to their continuing extraction [6]. While increasing aggregate content can improve concrete performance, it's crucial to consider the environmental impact. Extracting natural aggregates through crushing rocks and mining gravel pits significantly harms the environment. To address the environmental impact of natural aggregate extraction, finding alternative sources is crucial and mandatory. Indeed, construction and demolition waste (C&D waste) presents a promising option for obtaining coarse aggregates. The infrastructure development occurring in many rich countries results in higher production of C&D waste, resulting from the demolishing of old buildings and structures. Without feasible uses for these large quantities of waste, they often end up in landfills. This practice is unsustainable and ineffective, as continuous dumping strains landfill capacity and increases the necessity of creating new landfills or stockpiles. To avoid these circumstances, recycling C&D waste and using it as a substitute for natural aggregates (NA) would be beneficial both environmentally and economically. In fact, replacing NA with recycled concrete aggregates (RCA) can reduce the cost of concrete by up to 80%. This approach not only mitigates the environmental impact associated with NA extraction but also offers significant cost savings [7,8]. Although RCA has higher potential to enhance the environment and achieve sustainability visions and goals, it also has notable drawbacks. The presence of large pores and the attached weak mortar on the surface of RCA can limit its benefits by causing a significant reduction in concrete strength [9-11]. However, the addition of glass fibers GF holds the promise for mitigating these strength reductions and enhancing the overall performance of concrete.
Parthiban and Saravana Raja Mohan [12] conducted a review investigating the mechanical properties of geopolymer concrete with varying percentages of RCA (0%, 25%, 50%, 75%, and 100% by weight) and compared it to conventional OPC concrete. Their experimental results indicated that geopolymer concrete containing RCA exhibited higher compressive strength than conventional concrete made with natural aggregates. However, as the RCA content increased, the compressive strength of the geopolymer concrete decreased, indicating an inverse correlation between the RCA content and compressive strength. Another study conducted by Vignesh et al. [13] to identify the effect of glass fibers on the mechanical strength of geopolymer concrete. The results showed that geopolymer concrete reinforced with 1% glass fibers demonstrated improvements of 11% in compressive strength, 11% in tensile strength, compared to the control concrete. Consequently, adding 1% glass fibers by weight was identified as the optimal amount for enhancing the mechanical properties of these concrete mixtures.
According to the literature, multiple replacements are being under investigation to replace the traditional steel including glass fibers, carbon fibers and the basalt fibers [14]. Yet, the chosen material glass fibers have the potential to enhance the compressive strength of geopolymer concrete made with recycled concrete aggregates (RCA). However, this specific application has not been extensively studied. Therefore, this research aimed to evaluate the fresh and hardened properties of slag-fly ash blended geopolymer concrete incorporating glass fibers and RCA. Additionally, it explores how various process parameters affect the workability and compressive strength of geopolymer concrete.
2. Materials
A combination of Class F fly ash and ground granulated blast furnace slag served as the main binder materials in all concrete mixtures with a ratio of (1:3). Both materials were locally obtained from Ashtech and Emirates cement factory, respectively. These binders were activated using an alkaline solution consisting of grade N sodium silicate and 14 M sodium hydroxide solution. Specifically, sodium hydroxide solution was formed by dissolving 97% - 99% purity flakes in tap water. To minimize the extra water needed to enhance the workability of the geopolymer concrete, a polycarboxylic ether-based polymer superplasticizer (SP) from BASF Chemicals Company was used at a fixed percentage of 2.5% of the binder weight for all concrete mixtures.
Locally available dune sand from the deserts of the United Arab Emirates (UAE) was used as fine aggregate. Upon deep analysis, sand exhibited unique characteristics, such as a fineness modulus of 2.40, surface area of 5760 cm2/g, and absorption rate of 2%. While the coarse aggregates were either natural aggregate or RCA [15,16]. The natural aggregates used in this study was collected directly from Ras Al-Khaimah, a specific city in the UAE, Consisted of crushed dolomitic limestone with a nominal maximum size (NMS) of 19 mm. In contrast, the recycled concrete aggregates were sourced from a local recycling facility in the UAE, which specializes in recycling old demolished and construction concrete elements of varying compressive strengths.
Furthermore, In the experimental study, two different types of glass fibers were incorporated into the concrete mixtures. Typically, each one of them has its unique characteristics. Type A fibers were short, measuring just 24 mm in length, whereas Type B fibers had a more substantial length of 43 mm. The properties of the glass fibers are summarized in Table 1.
Table 1. The properties of Glass Fibers
Property |
Units |
Type A |
Type B |
Length |
mm |
24 |
43 |
Diameter |
mm |
0.7 |
0.7 |
Aspect ratio |
- |
35 |
62 |
Specific gravity |
- |
2.0 |
2.0 |
Tensile strength |
MPa |
> 1000 |
> 1000 |
Young’s modulus |
GPa |
42 |
42 |
3. Mixture proportions
Table 2 illustrates all the geopolymer concrete mixtures carried out to examine the impact of varying concrete ingredient proportions on the workability and compressive strength. Actually, the studied parameters included the replacement percentage of natural aggregates with RCA, binder content, additional water amount (added solely to the alkaline activator solution), particle size distribution of RCA, and volume fraction of glass fibers. The main objective was to identify the optimal mixture proportion that achieved a minimum workability of 150 mm and a 28-day compressive strength ranging from 30 to 40 MPa. To achieve this goal, a blended binder mixture was formulated with 75% slag and 25% fly ash [17]. This particular composition was chosen after confirming the significant impact of slag on compressive strength. The presence of a substantial amount of calcium in slag contributes to improved strength, which plays a crucial role in enhancing the overall performance of the mixture [18,19]. The liquid-to-binder (L/B) ratio was maintained at 0.5, while the sodium silicate to sodium hydroxide (SS/SH) ratio was set at 1.5. As mentioned earlier, a polycarboxylic ether-based polymer superplasticizer was consistently used across all mixtures at 2.5% of the binder weight, which was equivalent to nearly 11.25 kg/m3. Additionally, the study shows the influence of different glass fiber types and volume fractions, as well as the percentage of RCA replacement. Specifically, the glass fiber volume fractions varied from 0 to 2% (in 1% increments), while the RCA replacement percentages were set at 0 and 100%. In some mixes, the binder content was increased from 300 to 450 kg/m³ to assess its impact on the mixture properties.
4. Preparation of samples
The preparation of geopolymer concrete specimens started with accurately weighing the ingredients using a high-precision electronic scale. Once the required quantities were measured, the binder materials, fine aggregates, and coarse aggregates were mixed in a laboratory concrete mixer for a minimum of 3 minutes. In fact, it’s crucial to ensure that both natural and recycled concrete aggregates must be in a saturated surface dry (SSD) condition to account for their water absorption. To initiate the geopolymerization process, grade N sodium silicate and 14M sodium hydroxide were carefully prepared. Notably, the sodium hydroxide solution was made by dissolving flakes in tap water, creating a 14M solution that needed to cool for 1 hour after the exothermic reaction. This cooled solution was then mixed with sodium silicate to form the final alkaline activator solution. This activator, along with water and superplasticizers, was gradually added to the concrete mix to achieve a uniform consistency fresh mixture. If glass fibers were included in the mix, the appropriate volume fraction was calculated and mixed properly with the dry ingredients first to ensure even better distribution and avoid the fiber balling effect. Following this, the freshly mixed geopolymer concrete was poured into 100 mm cubical moulds and compacted on a vibrating table for at least 10 seconds to avoid the formation of bugholes or honeycombs. Polythene sheets were placed over the specimens to prevent water evaporation. After one day, the specimens were demoulded and cured at room temperature until the testing date.
Table 2. Mix proportions of geopolymer concrete (kg/m3)
Mix ID |
Aluminosilicate materials |
Fine aggregates |
Natural Coarse aggregates |
RCA |
Alkaline activator |
SP |
Water Content |
Glass fiber (%) |
Study Parameter |
|||||||||
Slag |
Fly ash |
Dune Sand |
10 mm |
20 mm |
SS |
SH | ||||||||||||
R0C450W100A0B0GF0 |
337.5 |
112.5 |
600 |
330 |
770 |
0 |
161 |
64 |
11.3 |
100 |
0 |
R |
||||||
R0C450W50A0B0GF0 |
337.5 |
112.5 |
600 |
330 |
770 |
0 |
161 |
64 |
11.3 |
50 |
0 |
R |
||||||
R100C300W100A0B0GF0-S |
225.0 |
75.0 |
725 |
0 |
0 |
1210 |
99 |
66 |
7.5 |
100 |
0 |
B |
||||||
R100C300W50A0B0GF0-S |
225.0 |
75.0 |
725 |
0 |
0 |
1210 |
99 |
66 |
7.5 |
50 |
0 |
B |
||||||
R100C300W25A0B0GF0-S |
225.0 |
75.0 |
725 |
0 |
0 |
1210 |
99 |
66 |
7.5 |
25 |
0 |
B |
||||||
R100C450W100A0B0GF0-S |
337.5 |
112.5 |
600 |
0 |
0 |
1100 |
161 |
64 |
11.3 |
100 |
0 |
B |
R |
W |
||||
R100C450W50A0B0GF0-S |
337.5 |
112.5 |
600 |
0 |
0 |
1100 |
161 |
64 |
11.3 |
50 |
0 |
B |
R |
W |
G |
|||
R100C450W25A0B0GF0-S |
337.5 |
112.5 |
600 |
0 |
0 |
1100 |
161 |
64 |
11.3 |
25 |
0 |
B |
W |
|||||
R100C450W50A100B0GF1-S |
337.5 |
112.5 |
600 |
0 |
0 |
1100 |
161 |
64 |
11.3 |
50 |
1 |
G |
||||||
R100C450W50A100B0GF2-S |
337.5 |
112.5 |
600 |
0 |
0 |
1100 |
161 |
64 |
11.3 |
50 |
2 |
G |
||||||
R100C450W50A0B100GF1-S |
337.5 |
112.5 |
600 |
0 |
0 |
1100 |
161 |
64 |
11.3 |
50 |
1 |
G |
||||||
R100C300W75A0B0GF0 |
225.0 |
75.0 |
725 |
0 |
0 |
1210 |
99 |
66 |
7.5 |
75 |
0 |
S |
||||||
R100C300W75A0B0GF0-S |
225.0 |
75.0 |
725 |
0 |
0 |
1210 |
99 |
66 |
7.5 |
75 |
0 |
S |
4. Performance evaluation
A slump cone test was conducted to evaluate the workability of geopolymer concrete, following the requirements procedures and procedures specified in ASTM C143 [20]. Actually, there was a strong preference to perform this specific test instead of others due to its simplicity and wide application in the construction field. Meanwhile. The compressive strength of concrete specimens was evaluated at the ages of 1 and 7 days in accordance with ASTM C39 [21]. In order to increase the reliability and accuracy of the results, each mixture was replicated and tested three times. The average value was then calculated to provide a significant and real representation of the concrete properties.
4. Results and Discussion
4. 1. Workability
Figure 1 presents the slump values of slag-fly ash blended geopolymer concrete. The concrete mixtures were categorized into five distinct groups, each studying a separate parameter. The summarization of the impact of process parameters in the workability of geopolymer concrete is graphically presented in Figure 2. The first group consisted of six different concrete mixtures designed to investigate the effect of increasing binder content on workability. Specifically, the binder content was raised from 300 to 450 kg/m3. Experimental results revealed a significant improvement in the workability of geopolymer concrete with higher binder content. With a water content of 100 kg/m3, increasing the binder content resulted in a slump value of 240 mm compared to 225 mm obtained with a binder content of 300 kg/m3. This observation reflected an improvement of 7% compared to its counterpart mixture. A similar trend was observed when the water content was 50 kg/m³, where increasing the binder content enhanced workability by up to 30%. The most pronounced impact was noted in the mixture with 75 kg/m³ of water, where the slump values increased from 140 mm to 235 mm, representing a 68% improvement. Therefore, regardless of the water content used, increasing the binder content led to a significant improvement in the workability of geopolymer concrete. Similar improvement trends associated with increasing binder content were observed in a study by El-Hassan and Ismail [16]. The increase in the workability associated with the increasing binder content is typically attributed to the improved particle packing and arrangement within the concrete, which results from the increased binder content [22-23]. This additional binder helps to fill the gaps and spaces among the larger particles, thereby enhancing the flowability of the concrete [24]. Changes in water content, like those in binder content, had a significant impact on workability. In mixtures with a high binder content of 450 kg/m³, increasing the water content from 25 to 50 and 100 kg/m³ led to a noticeable rise in slump values, from 205 to 230 and 240 mm, representing an average improvement of 12 and 17%, respectively. This trend was also observed in mixtures with a lower binder content of 300 kg/m³, where slump values increased dramatically from 20 mm to 225 mm. These results highlighted the pronounced effect of water content on the workability of concrete, especially in mixtures with lower binder content. This finding was anticipated, as the more water content increase effectively the flow-ability of concrete [25].
This study also examined the impact of substituting natural aggregates (NA) with recycled concrete aggregates (RCA) in geopolymer concrete. Although theoretically, the inclusion of RCA is usually expected to reduce slump values, the experimental results showed that replacing NA with RCA didn’t significantly impact the workability of alkali-activated geopolymer concrete. Even the full substitution had no major effect at all. This discrepancy between theoretical expectations and experimental results may be due to the types, quality, and composition of RCA used, which had similar physical properties such as surface roughness and frictional texture to those of NA [15], [26]. For example, the fineness modulus and surface area for the RCA were 7.44 and 2.5 cm²/g, respectively, compared to 6.82 and 2.49 cm²/g for NA. These results reflected the significant similarity between these types of aggregates. Indeed, the RCA-based geopolymer concrete mixture (R1000C450W100A0B0GF0) exhibited a slump value of 240 mm, compared to the NA-based geopolymer concrete counterpart (R0C450W100A0B0GF0), which showed a slump value of 239 mm. Similar results were obtained for all mixtures regardless of the water content used.
Moreover, this study highlighted the impact of varying the type and volume fraction of glass fibers on the workability of alkali-activated geopolymer concrete. Indeed, the addition of fiber led to further reduction in slump values. This decrease in slump was observed to be proportional to the increase in the volume fraction of glass fibers. The inclusion of 1 and 2% Type A glass fibers in the concrete mixtures led to a decrease in slump values, ranging from 230 to 210 mm. This specific range indicated a reduction in workability by approximately 2% to 9%, compared to the control mix. In contrast to Type A glass fibers, the maximum volume fraction for Type B glass fibers was restricted to 1%. Any attempt to exceed this volume resulted in concrete that was uncastable. Consequently, the experimental work was restricted to incorporating only 1% of Type B glass fibers. This incorporation resulted in a significant reduction in workability, with a 24% decrease in slump value, dropping from 230 mm to 175 mm. These findings highlight the more pronounced negative impact of Type B glass fibers on the workability of geopolymer concrete compared to Type A glass fibers. The differences in the reduction percentages between Type A and Type B glass fibers were typically attributed to the variations in their aspect ratios [27-28]. The longer length and aspect ratio of Type B fibers compared to Type A fibers led to more tangling and balling within the concrete mix. This increased friction and fiber interaction generally resist the smooth flow of the concrete, which resulted in a more significant reduction in workability and lower slump values as well. This reduction was aligned with the findings reported in previous studies[29-30].
The effect of sieving RCA to remove particles smaller than 4.75 mm and larger than 19 mm on the workability of geopolymer concrete was also assessed through this study. In fact, a notable substantial improvement in the workability of geopolymer concrete was obtained after applying the sieving phenomenon. The average slump value was raised from 0 to 210 mm by eliminating particles smaller than 4.75 mm and larger than 19 mm. Indeed, removing smaller particles (less than 4.75 mm) resulted in larger aggregates with a lower surface area, which usually improved the workability due to the reduced amount of water being absorbed caused by the resultant reduced surface area. In a similar way, eliminating particles larger than 19 mm could reduce the overall number of large voids in the concrete, which was highly effective and impactful in further improving the workability of geopolymer concrete.
As discussed earlier and illustrated in Figure 2, among all the concrete mixtures, geopolymer concrete mix R100C450W100A0B0GF0-S exhibited the highest value of workability, reaching almost 240 mm. Notably, this mix also had the highest binder content. On the other hand, for mixtures with lower binder content, mix R100C300W100A0B0GF0-S achieved the best value of workability of 225 mm. This indicates the more pronounced impact of binder content in improving the overall workability of concrete mixtures made with lower water content. Moreover, Due to the high similarity between the two types of aggregates in terms of physical and surface textures, replacing NA with RCA had no impact at all on workability. Therefore, it was clear that the difference between the workability of NA-based geopolymer concrete and RCA-based geopolymer concrete was zero, irrespective of the amount of water.
The addition of Type A glass fibers at a volume fraction of 1% noticeably reduced its slump value to 225 mm compared to the mixture without fibers. While increasing the fiber content to 2% further decreased the slump value to 210 mm, which clearly indicated the additional minimal impact on workability. A reduction of 7% in the workability was observed when the volume fraction of Type A glass fibers was raised from 1 to 2%. In comparison with Type A GF, Type B glass fibers had an even more substantial negative impact on the workability by lowering the workability value by 24%, compared to 7% caused by the addition of 1% Type A GF.
While sieving the RCA was ultimately beneficial in dramatically improving the workability of geopolymer concrete. It is strongly recommended to employ such a practice when using RCA in concrete applications.
Furthermore, the mean workability of alkali-activated geopolymer concrete in this study was approximately 197.42 mm with a standard deviation of 62.92 mm. In fact, the high value of standard deviation indicates significant variability among the concrete mixtures. This outcome was anticipated, as the concrete mixtures were prepared with varying concrete proportions aiming to study several parameters, which resulted in increasing the variability of the mixtures and, thus, a higher standard deviation. Statistically, mild outliers were identified when any value exceed the specific limit of µ±2σ (197.42±62.92). Therefore, the mixture R100C300W75A0B0GF0, which exhibited a zero-slump value is considered as a mild outlier. To improve the accuracy of the data, this mix could be excluded from any further analysis.
Additionally, the coefficient of variation was identified as 18%, which indicated a low to moderate level of variability compared to the mean workability value. This could reflect an overall acceptable dispersion of data. There were some sources of errors that impacted the accuracy and consistency of the results. These errors happened due to errors in measuring the components, variations in weather temperature, which can negatively affect the workability due to the accelerated concrete setting in high temperature, and human errors such as inaccuracies during slump tests or reading measurements.
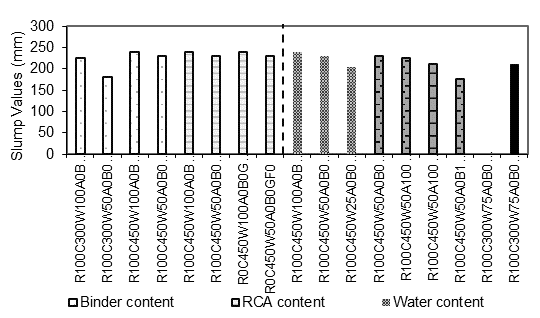
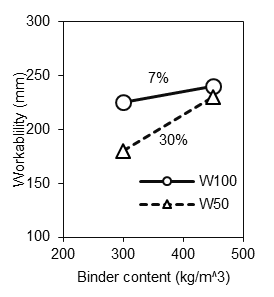
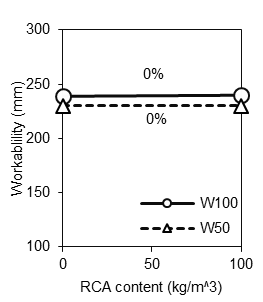
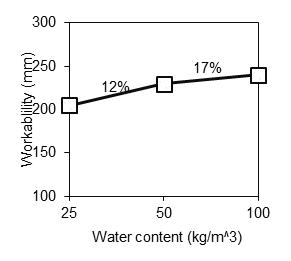
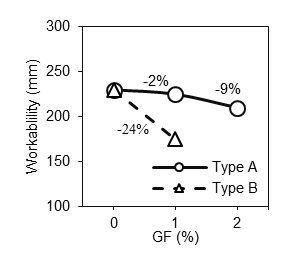
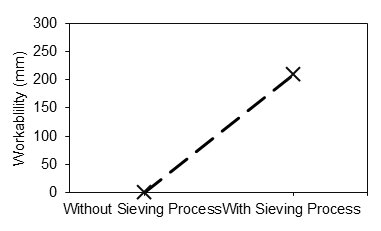
4. 2. Compressive strength
Figure 3 illustrates the compressive strength (fcu) of alkali-activated geopolymer concrete at 1 and 7 days. While Figure 4 defined the impact of several parameters on the concrete strength. The experimental results indicated an improvement in the compressive strength with the increases in the binder content. This observation was consistent across all concrete mixes, regardless of the amount of additional water used. For instance, mix R100C450W100A0B0GF0 exhibited a 1- and 7-day compressive strength of 19.5 and 26.9 MPa, respectively, compared to its counterpart mix with a binder content of 300 kg/m3 where it achieved strengths of 1.4 and 11.3 MPa. Similarly, when the water content was fixed at 50 kg/m3, increasing the binder content improved the compressive strength by 70 and 17% after 1 and 7-day curing, respectively. Indeed, similar enhancement was investigated for all the mixtures irrespective of the amount of additional water used. In mixtures with a high binder content of 450 kg/m³, the 7-day compressive strength ranged from 26.9 to 38.7 MPa, compared to their counterparts with strengths ranging from 11.3 to 29.2 MPa. Moreover, the 7-day compressive strength improved by 138, 17, and 33% with an increase in the binder content from 300 to 450 kg/m3. These findings suggest that higher binder content enhanced compressive strength by reducing the volume of voids within the concrete. The excess binder material effectively fills these voids and consequently leads to a denser structure with improved cohesion and overall strength [31].
The impact of incorporating RCA in fly ash/slag blended geopolymer concrete was investigated through a deep comparing between different concrete mixtures at a different water content. An inverse correlation between the amount of RCA and compressive strength was observed and proved experimentally. In fact, regardless of the amount of additional water used, the compressive strength decreased with the addition of RCA. The full replacement of NA with RCA led to a reduction on the 1-and 7-day compressive strength up to 19 and 25%, respectively. Furthermore, at water content of 100 kg/m3, the respective 1 and 7-day compressive strengths for concrete mixes incorporated RCA decreased by approximately 2 and 5%. Such a reduction in the compressive strength associated with the incorporation of RCA is attributed to the presence of large pores inside the RCA and the weak attached mortar on the surface of RCA. This reduction trend was consistent with a study conducted by other researches [32-33].
While adding water could improve the workability of geopolymer concrete, it has a significant negative influence in terms of compressive strength. Increasing the water content from 25 to 50 and 100 kg/m3 led to substantial reductions in early-age compressive strength, from 20.4 to 18 and 17 MPa, representing corresponding reductions of 12 and 17%, respectively. A similar trend was observed at 7 days, with compressive strength reductions of 22 and 30% compared to the mixture with 100 kg/m³ of additional water. Experimental works revealed an inverse relationship between compressive strength and water-to-geopolymer binder material ratio. As the water-to-geopolymer binder ratio increases, the compressive strength decreases accordingly. This is because most of the added water evaporates during the geopolymerization process, enhancing workability but not contributing to strength. Similarly, the excess amount of water could reduce density and create defects in its microstructure, which consequently led to a further reduction in the strength. These findings were consistent with the outcomes of Patankar et al. [34]
The influence of incorporating different types and volume fractions of glass fibers on the compressive strength of geopolymer concrete was thoroughly investigated. The experimental results showed a slight increase in compressive strength with the addition of Type A glass fibers. Specifically, the compressive strength rose from 18 to 19 MPa with 1% Type A fibers and to 19.3 MPa with 2% Type A fibers. In contrast, the inclusion of 1% of Type B glass fibers resulted in a 1-day compressive strength of 19.2 MPa, representing corresponding improvements of 7%. Regardless of the type or volume fraction of glass fibers, the addition of glass fibers consistently enhanced only the early-age compressive strength of the geopolymer concrete. On the other hand, the 7-day compressive strength remained almost the same across all mixtures. These findings highlighted the more positive pronounced effect of fibers on early-age performance. Indeed, the impact of Type B glass fibers was slightly greater than its counterpart Type A glass fibers at the same volume fraction. Such a result is typically attributed to the higher aspect ratio of Type B fibers, which effectively reduces the formation and the propagation of the cracks thereby enhancing the overall strength [35-37].
Furthermore, the impact of sieving recycled concrete aggregates (RCA) to remove particles smaller than 4.75 mm and larger than 19 mm is graphically illustrated in Figure 3. The experimental results demonstrated a significant enhancement in the compressive strength after sieving the RCA, with strength increasing from 15 to 20.3 MPa, representing a corresponding enhancement of nearly 35%. Similarly, the 1-day compressive strength effectively increased substantially from 6.6 to 8.5 MPa. Actually, removing fine particles smaller than 4.75 mm can reduce water absorption due to the reduction in the surface area. At the same time, this practice also helps in improving the packing of aggregates inside the concrete, resulting in an even more cohesive mixture with higher density and strength. Similarly, eliminating large particles (larger than 19 mm) led to a notable reduction in voids, thereby enhancing the strength. [38-40]. Figure 4 showed the impact of process parameters in the compressive strength of geopolymer concrete.
As previously discussed and shown in Figure 4, among all the concrete mixtures cast to evaluate the effect of the binder content, the geopolymer concrete mix R100C450W25A0B0GF0-S exhibited the highest compressive strength of 38.7 MPa at 7 days. Thos represented a 33% enhancement compared to its counterpart mixture with lower binder content. Similar strength enhancement trends were observed at all ages, regardless of the water quantity. Furthermore, due to the large voids and the weakness of the mortar attached to the surface of RCA, the strength of the concrete mixture decreased significantly with the inclusion of RCA. The reduction in strength was particularly notable with lower water content. A reduction of approximately 25% in the 7-day compressive strength was observed with the full replacement of NA with RCA at a water content of 50 kg/m³, compared to a 2% reduction at a water content of 100 kg/m³.
Undoubtedly, the water content had a significantly negative impact on the compressive strength, regardless of the age of concrete. Indeed, increasing the water content from 0 to 50 kg/m³ deceased the 7-day compressive strength by 22%. Similarly, a further increase to 100 kg/m³ resulted in a 30% reduction.
Surprisingly, the inclusion of glass fibers had no impact on the 7-day compressive strength. However, there was a slight increase in the 1-day compressive strength with the addition of glass fibers. In fact, Type B GF had a slightly more pronounced impact compared to Type A GF.
Actually, sieving the RCA to remove particles smaller than 4.75 mm and larger than 19 mm increased the 7-day compressive strength by nearly 35%. This improvement resulted from the reduction in water absorption associated with the lower surface area due to the elimination of small particles. Additionally, the reduction in the volume of voids caused by the removal of large particles also contributed to the enhanced strength.
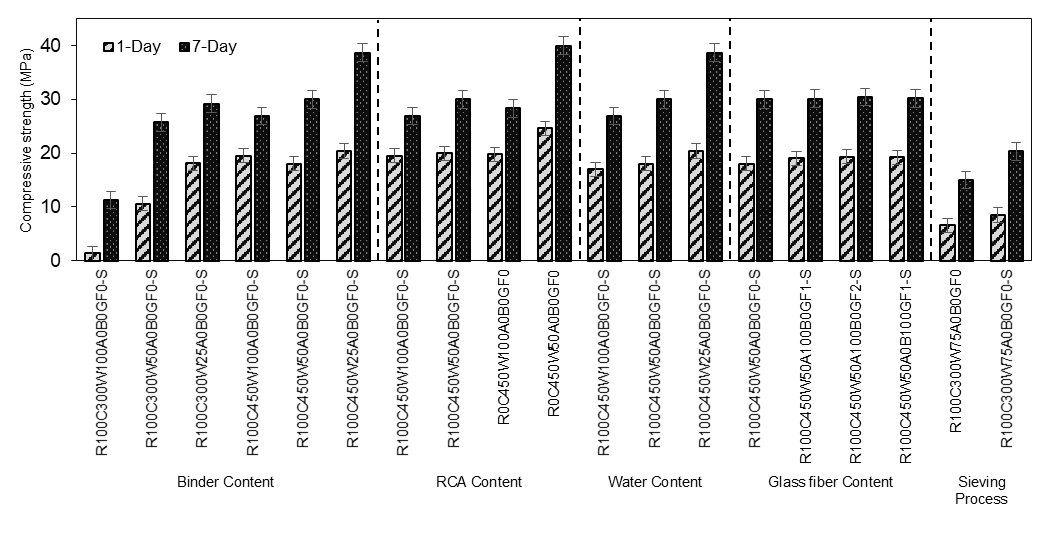
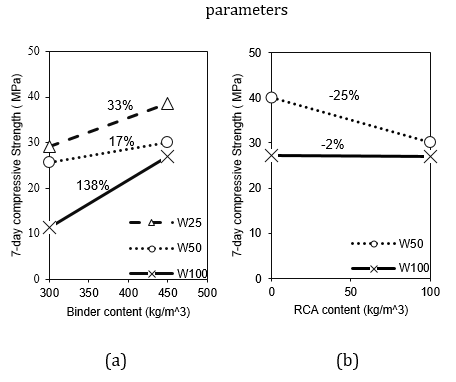
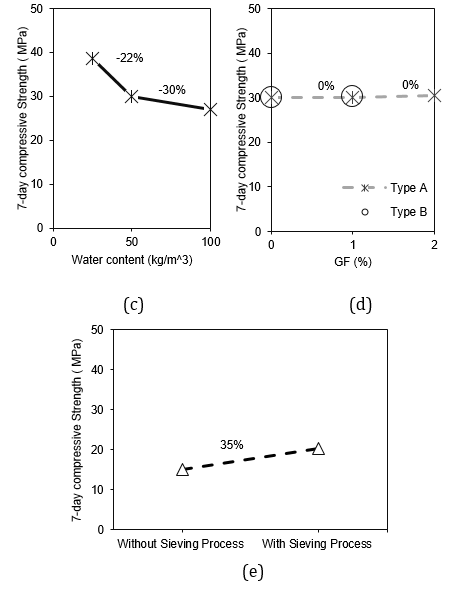
Moreover, the error analysis was conducted to assess the deviation and dispersion of the data. Table 3 presents a comprehensive summary of the compressive strength values and their respective standard deviations and percentage errors for each concrete mixture. In general, a smaller standard deviation value represented a low variability and more precise and consistent measurements. Indeed, the majority of the concrete mixtures had a lower standard deviation, which indicated a low dispersion of the data. Moreover, the error percentage was calculated for each mix at the two ages separately. During the experimental process and data analysis, several sources of uncertainty and error were identified. These errors included random errors from sample preparation and testing procedures, human errors from the inaccurate measurements and recording of data, and systematic errors that could have resulted from improper calibration of the testing machine.
Table 3. The error analysis of geopolymer concrete mixtures
Mix ID |
Slump Value (mm) |
Cu,1 day
(MPa) |
Error
(%) |
Cu,7 day
(MPa) |
Error
(%) |
R100C300W100A0B0GF0-S |
225 |
1.4±0.2 |
8.2 |
11.3±2.80 |
14.3 |
R100C300W50A0B0GF0-S |
180 |
10.6±1.95 |
10.6 |
25.7±0.46 |
1.0 |
R100C450W100A0B0GF0-S |
240 |
19.5±0.29 |
0.9 |
26.9±3.63 |
7.8 |
R100C450W50A0B0GF0-S |
230 |
18.0±1 |
3.2 |
30±0.25 |
0.5 |
R0C450W100A0B0GF0 |
239 |
19.8±0.74 |
2.1 |
28.3±1.66 |
3.4 |
R0C450W50A0B0GF0 |
230 |
24.6±0.06 |
0.1 |
40±1.00 |
1.4 |
R100C450W25A0B0GF0-S |
205 |
20.4±4.01 |
11.4 |
38.7±1.50 |
2.2 |
R100C450W50A100B0GF1-S |
225 |
19.0±0.25 |
0.8 |
30.1±1.72 |
3.3 |
R100C450W50A100B0GF2-S |
210 |
19.3±1.04 |
3.1 |
30.4±1.59 |
3.0 |
R100C450W50A0B100GF1-S |
175 |
19.2±0.06 |
0.2 |
30.2±1.86 |
3.5 |
R100C300W75A0B0GF0 |
0 |
6.6±0.06 |
0.5 |
15±0.15 |
0.6 |
R100C300W75A0B0GF0-S |
210 |
8.5±0.68 |
4.6 |
20.3±1.18 |
3.4 |
5. Conclusion
This paper examined the impact of various mix design parameters on the workability and compressive strength of geopolymer concrete. These parameters included the replacement percentage of natural aggregates (NA) with recycled concrete aggregates (RCA), binder content, additional water quantity, particle size distribution of RCA, and volume fraction of glass fibers (GF). Based on the experimental results, the following conclusions were drawn:
- Increasing binder content from 300 to 450 kg/m³ improved the workability by 30% and enhanced the compressive strength by almost 17%
- The full substitution of NA with RCA had no significant effect on workability but decreased the 7-day compressive strength by 25%.
- A direct relationship between workability of geopolymer concrete and the addition of water was observed. However, there was an inverse relationship between compressive strength and additional water content.
- As the water-to-geopolymer binder ratio increased, the compressive strength decreased accordingly
- The addition of 1 and 2% GF, by volume, had a minor effect on the compressive strength of RCA slag-fly ash blended geopolymer concrete. Fibers with larger aspect ratio were more impactful on the 1-day strength.
- Sieving the RCA to remove particles smaller than 4.75 mm and larger than 19 mm increased the slump to 210 mm and the 1- and 7-day compressive strengths by 29% and 35%, respectively.
- The optimum design of RCA-based geopolymer concrete to be comparable with NA-based geopolymer concrete was attained by using 50 kg/m3 of additional water, which led to a slump of 230 mm and compressive strength of 30 MPa.
- Geopolymer materials offer several advantages, such as addressing the environmental concerns associated with conventional concrete and providing superior technical properties.
Acknowledgments
The authors gratefully acknowledge the financial support of the United Arab Emirates University through grant 12N115.
References
[1] K. A. A., "Strength characteristic of geopolymer concrete containing recycled concrete aggregate," International Journal of Civil & Environmental Engineering IJCEE-IJENS Vol: 11 No: 01, vol. 11, Jan. 2011.
[2] D. D. Burduhos Nergis, M. M. A. B. Abdullah, P. Vizureanu, and M. F. M. Tahir, "Geopolymers and Their Uses: Review," IOP Conf. Ser.: Mater. Sci. Eng., vol. 374, p. 012019, Jun. 2018, doi: 10.1088/1757-899X/374/1/012019.
View Article
[3] P. Duxson, A. Fernández-Jiménez, J. L. Provis, G. C. Lukey, A. Palomo, and J. S. J. Van Deventer, "Geopolymer technology: the current state of the art," J Mater Sci, vol. 42, no. 9, pp. 2917-2933, May 2007, doi: 10.1007/s10853-006-0637-z.
View Article
[4] Y. S. N. Kishore, S. G. D. Nadimpalli, A. K. Potnuru, J. Vemuri, and M. A. Khan, "Statistical analysis of sustainable geopolymer concrete," Materials Today: Proceedings, vol. 61, pp. 212-223, 2022, doi: 10.1016/j.matpr.2021.08.129.
View Article
[5] V. K. J. Bohra, R. Nerella, and S. R. C. Madduru, "Material properties, processing & characterization of fly ash based geopolymer," Materials Today: Proceedings, vol. 19, pp. 2617-2621, 2019, doi: 10.1016/j.matpr.2019.10.099.
View Article
[6] M. Nedeljković, J. Visser, B. Šavija, S. Valcke, and E. Schlangen, "Use of fine recycled concrete aggregates in concrete: A critical review," Journal of Building Engineering, vol. 38, p. 102196, Jun. 2021, doi: 10.1016/j.jobe.2021.102196.
View Article
[7] Md. U. Hossain, C. S. Poon, I. M. C. Lo, and J. C. P. Cheng, "Comparative environmental evaluation of aggregate production from recycled waste materials and virgin sources by LCA," Resources, Conservation and Recycling, vol. 109, pp. 67-77, May 2016, doi: 10.1016/j.resconrec.2016.02.009.
View Article
[8] A. M. Braga, J. D. Silvestre, and J. De Brito, "Compared environmental and economic impact from cradle to gate of concrete with natural and recycled coarse aggregates," Journal of Cleaner Production, vol. 162, pp. 529-543, Sep. 2017, doi: 10.1016/j.jclepro.2017.06.057.
View Article
[9] S. Mesgari, A. Akbarnezhad, and J. Z. Xiao, "Recycled geopolymer aggregates as coarse aggregates for Portland cement concrete and geopolymer concrete: Effects on mechanical properties," Construction and Building Materials, vol. 236, p. 117571, Mar. 2020, doi: 10.1016/j.conbuildmat.2019.117571.
View Article
[10] S. Shoaib, T. El-Maaddawy, H. El-Hassan, B. El-Ariss, and M. Alsalami, "Characteristics of Basalt Macro-Fiber Reinforced Recycled Aggregate Concrete," Sustainability, vol. 14, no. 21, p. 14267, Nov. 2022, doi: 10.3390/su142114267.
View Article
[11] N. Kachouh, T. El-Maaddawy, H. El-Hassan, and B. El-Ariss, "Shear Response of Recycled Aggregates Concrete Deep Beams Containing Steel Fibers and Web Openings," Sustainability, vol. 14, no. 2, p. 945, Jan. 2022, doi: 10.3390/su14020945.
View Article
[12] K. Parthiban and K. Saravana Raja Mohan, "Influence of recycled concrete aggregates on the engineering and durability properties of alkali activated slag concrete," Construction and Building Materials, vol. 133, pp. 65-72, Feb. 2017, doi: 10.1016/j.conbuildmat.2016.12.050.
View Article
[13] S. Krishna, "Study on Mechanical properties of Geo Polymer Concrete Using M-Sand and Glass Fibers," 2014. Accessed: Sep. 05, 2023. [Online]. Available:
View Article
[14] M. Chkhachirou, T. El-Maaddawy, and H. El-Hassan, "Effect of Temperature on Basalt Fiber Reinforced Polymer Bars in Moist Geopolymer Concrete," presented at the The 9th International Conference on Civil, Structural and Transportation Engineering, Jun. 2024. doi: 10.11159/iccste24.183.
View Article
[15] M. Abughali, T. El-Maaddawy, and H. El-Hassan, "Properties of Geopolymer Concrete Made With Recycled Concrete Aggregates and Glass Fibers," presented at the The 9th International Conference on Civil, Structural and Transportation Engineering, Jun. 2024. doi: 10.11159/iccste24.199.
View Article
[16] H. El-Hassan and N. Ismail, "Effect of process parameters on the performance of fly ash/GGBS blended geopolymer composites," Journal of Sustainable Cement-Based Materials, vol. 7, no. 2, pp. 122-140, Mar. 2018, doi: 10.1080/21650373.2017.1411296.
View Article
[17] H. El-Hassan and S. Elkholy, "Enhancing the performance of Alkali-Activated Slag-Fly ash blended concrete through hybrid steel fiber reinforcement," Construction and Building Materials, vol. 311, p. 125313, Dec. 2021, doi: 10.1016/j.conbuildmat.2021.125313.
View Article
[18] H. Wang, X. Zhao, T. Wang, L. Su, B. Zhou, and Y. Lin, "Determination of Gel Products in Alkali-Activated Fly Ash-Based Composites Incorporating Inorganic Calcium Additives," Advances in Materials Science and Engineering, vol. 2022, pp. 1-13, Feb. 2022, doi: 10.1155/2022/7476671.
View Article
[19] I. Garcia-Lodeiro, A. Palomo, A. Fernández-Jiménez, and D. E. Macphee, "Compatibility studies between N-A-S-H and C-A-S-H gels. Study in the ternary diagram Na2O-CaO-Al2O3-SiO2-H2O," Cement and Concrete Research, vol. 41, no. 9, pp. 923-931, Sep. 2011, doi: 10.1016/j.cemconres.2011.05.006.
View Article
[20] C09 Committee, "Standard Test Method for Slump of Hydraulic-Cement Concrete." ASTM International. doi: 10.1520/C0143_C0143M.
View Article
[21] C09 Committee, "ASTM C39 / C39M Standard Test Method for Compressive Strength of Cylindrical Concrete Specimens." ASTM International.
View Article
[22] L. Nishanth and Dr. N. N. Patil, "Experimental evaluation on workability and strength characteristics of self-consolidating geopolymer concrete based on GGBFS, flyash and alccofine," Materials Today: Proceedings, vol. 59, pp. 51-57, 2022, doi: 10.1016/j.matpr.2021.10.200.
View Article
[23] Niyazuddin and U. B, "Mechanical and durability properties of standard and high strength geopolymer concrete using particle packing theory," Construction and Building Materials, vol. 400, p. 132722, Oct. 2023, doi: 10.1016/j.conbuildmat.2023.132722.
View Article
[24] D. Hou, M. Zhang, Z. Ma, D. Wu, Q.Song, Q. Zheng, M.Wang, S. Sui, X. Zhang, and Xi.Wang, "Comparative optimization of densified system of ultra-fine particles (DSP) and Horsfield filling toward UHPC fabrication," Cement and Concrete Composites, vol. 144, p. 105267, Nov. 2023, doi: 10.1016/j.cemconcomp.2023.105267.
View Article
[25] S. Popovics, "ANALYSIS OF THE INFLUENCE OF WATER CONTENT ON CONSISTENCY".
[26] M. C. Limbachiya, T. Leelawat, and R. K. Dhir, "Use of recycled concrete aggregate in high-strength concrete," Mat. Struct., vol. 33, no. 9, pp. 574-580, Nov. 2000, doi: 10.1007/BF02480538.
View Article
[27] P. A. Sivanantham, G. G. Prabhu, G. G. Vimal Arokiaraj, and K. Sunil, "Effect of Fibre Aspect-Ratio on the Fresh and Strength Properties of Steel Fibre Reinforced Self-Compacting Concrete," Advances in Materials Science and Engineering, vol. 2022, pp. 1-8, May 2022, doi: 10.1155/2022/1207273.
View Article
[28] A. Alrawashdeh and O. Eren, "Mechanical and physical characterisation of steel fibre reinforced self-compacting concrete: Different aspect ratios and volume fractions of fibres," Results in Engineering, vol. 13, p. 100335, Mar. 2022, doi: 10.1016/j.rineng.2022.100335.
View Article
[29] U. Sharma N. Gupta, A. Bahrami, Y.O. Özkılıç, M. Verma, P. Berwal, E. Althaqafi, M.A. Khan, and S. Islam, "Behavior of Fibers in Geopolymer Concrete: A Comprehensive Review," Buildings, vol. 14, no. 1, p. 136, Jan. 2024, doi: 10.3390/buildings14010136.
View Article
[30] O. Mohamed and H. Zuaiter, "Fresh Properties, Strength, and Durability of Fiber-Reinforced Geopolymer and Conventional Concrete: A Review," Polymers, vol. 16, no. 1, p. 141, Jan. 2024, doi: 10.3390/polym16010141.
View Article
[31] C. De Backere, T. De Beer, C. Vervaet, and V. Vanhoorne, "Effect of binder type and lubrication method on the binder efficacy for direct compression," International Journal of Pharmaceutics, vol. 607, p. 120968, Sep. 2021, doi: 10.1016/j.ijpharm.2021.120968.
View Article
[32] P. Nuaklong, V. Sata, and P. Chindaprasirt, "Influence of recycled aggregate on fly ash geopolymer concrete properties," Journal of Cleaner Production, vol. 112, pp. 2300-2307, Jan. 2016, doi: 10.1016/j.jclepro.2015.10.109.
View Article
[33] F. U. A. Shaikh, "Mechanical and durability properties of fly ash geopolymer concrete containing recycled coarse aggregates," International Journal of Sustainable Built Environment, vol. 5, no. 2, pp. 277-287, Dec. 2016, doi: 10.1016/j.ijsbe.2016.05.009.
View Article
[34] S. V. Patankar, S. S. Jamkar, and Y. M. Ghugal, "EFFECT OF WATER-TO-GEOPOLYMER BINDER RATIO ON THE PRODUCTION OF FLY ASH BASED GEOPOLYMER CONCRETE," IJATCE, pp. 296-300, Oct. 2012, doi: 10.47893/IJATCE.2012.1048.
View Article
[35] C. Han, J. Pang, S. Hu, and C. Yang, "Study on static and dynamic mechanical properties and microstructure of silica fume-polypropylene fiber modified rubber concrete," Sci Rep, vol. 14, no. 1, p. 12573, May 2024, doi: 10.1038/s41598-024-63341-z.
View Article
[36] Y. Zheng, P. Zhang, Y. Cai, Z. Jin, and E. Moshtagh, "Cracking resistance and mechanical properties of basalt fibers reinforced cement-stabilized macadam," Composites Part B: Engineering, vol. 165, pp. 312-334, May 2019, doi: 10.1016/j.compositesb.2018.11.115.
View Article
[37] C.-S. Tang, B. Shi, Y.-J. Cui, C. Liu, and K. Gu, "Desiccation cracking behavior of polypropylene fiber-reinforced clayey soil," Can. Geotech. J., vol. 49, no. 9, pp. 1088-1101, Sep. 2012, doi: 10.1139/t2012-067.
View Article
[38] Safiuddin, U. J. Alengaram, A. Salam, M. Z. Jumaat, F. F. Jaafar, and H. B. Saad, "Properties of high-workability concrete with recycled concrete aggregate," Mat. Res., vol. 14, no. 2, pp. 248-255, Jun. 2011, doi: 10.1590/S1516-14392011005000039.
View Article
[39] Abba Bashir, Chhavi Gupta, M A Abubakar, and S I Abba, "Comparison of Properties of Coarse Aggregate Obtained from Recycled Concrete with that of Conventional Coarse Aggregates." Unpublished, 2018.
View Article
[40] Md. H. R. Sobuz, SD. Datta, AS. Akid, VW. Tam, S. Islam, MJ. Rana, F. Aslani, Ç. Yalçınkaya, and NM. Sutan, "Evaluating the effects of recycled concrete aggregate size and concentration on properties of high-strength sustainable concrete," Journal of King Saud University - Engineering Sciences, p. S1018363922000356, Apr. 2022, doi: 10.1016/j.jksues.2022.04.004.
View Article
[1] K. A. A., "Strength characteristic of geopolymer concrete containing recycled concrete aggregate," International Journal of Civil & Environmental Engineering IJCEE-IJENS Vol: 11 No: 01, vol. 11, Jan. 2011.
[2] D. D. Burduhos Nergis, M. M. A. B. Abdullah, P. Vizureanu, and M. F. M. Tahir, "Geopolymers and Their Uses: Review," IOP Conf. Ser.: Mater. Sci. Eng., vol. 374, p. 012019, Jun. 2018, doi: 10.1088/1757-899X/374/1/012019. View Article
[3] P. Duxson, A. Fernández-Jiménez, J. L. Provis, G. C. Lukey, A. Palomo, and J. S. J. Van Deventer, "Geopolymer technology: the current state of the art," J Mater Sci, vol. 42, no. 9, pp. 2917-2933, May 2007, doi: 10.1007/s10853-006-0637-z. View Article
[4] Y. S. N. Kishore, S. G. D. Nadimpalli, A. K. Potnuru, J. Vemuri, and M. A. Khan, "Statistical analysis of sustainable geopolymer concrete," Materials Today: Proceedings, vol. 61, pp. 212-223, 2022, doi: 10.1016/j.matpr.2021.08.129. View Article
[5] V. K. J. Bohra, R. Nerella, and S. R. C. Madduru, "Material properties, processing & characterization of fly ash based geopolymer," Materials Today: Proceedings, vol. 19, pp. 2617-2621, 2019, doi: 10.1016/j.matpr.2019.10.099. View Article
[6] M. Nedeljković, J. Visser, B. Šavija, S. Valcke, and E. Schlangen, "Use of fine recycled concrete aggregates in concrete: A critical review," Journal of Building Engineering, vol. 38, p. 102196, Jun. 2021, doi: 10.1016/j.jobe.2021.102196. View Article
[7] Md. U. Hossain, C. S. Poon, I. M. C. Lo, and J. C. P. Cheng, "Comparative environmental evaluation of aggregate production from recycled waste materials and virgin sources by LCA," Resources, Conservation and Recycling, vol. 109, pp. 67-77, May 2016, doi: 10.1016/j.resconrec.2016.02.009. View Article
[8] A. M. Braga, J. D. Silvestre, and J. De Brito, "Compared environmental and economic impact from cradle to gate of concrete with natural and recycled coarse aggregates," Journal of Cleaner Production, vol. 162, pp. 529-543, Sep. 2017, doi: 10.1016/j.jclepro.2017.06.057. View Article
[9] S. Mesgari, A. Akbarnezhad, and J. Z. Xiao, "Recycled geopolymer aggregates as coarse aggregates for Portland cement concrete and geopolymer concrete: Effects on mechanical properties," Construction and Building Materials, vol. 236, p. 117571, Mar. 2020, doi: 10.1016/j.conbuildmat.2019.117571. View Article
[10] S. Shoaib, T. El-Maaddawy, H. El-Hassan, B. El-Ariss, and M. Alsalami, "Characteristics of Basalt Macro-Fiber Reinforced Recycled Aggregate Concrete," Sustainability, vol. 14, no. 21, p. 14267, Nov. 2022, doi: 10.3390/su142114267. View Article
[11] N. Kachouh, T. El-Maaddawy, H. El-Hassan, and B. El-Ariss, "Shear Response of Recycled Aggregates Concrete Deep Beams Containing Steel Fibers and Web Openings," Sustainability, vol. 14, no. 2, p. 945, Jan. 2022, doi: 10.3390/su14020945. View Article
[12] K. Parthiban and K. Saravana Raja Mohan, "Influence of recycled concrete aggregates on the engineering and durability properties of alkali activated slag concrete," Construction and Building Materials, vol. 133, pp. 65-72, Feb. 2017, doi: 10.1016/j.conbuildmat.2016.12.050. View Article
[13] S. Krishna, "Study on Mechanical properties of Geo Polymer Concrete Using M-Sand and Glass Fibers," 2014. Accessed: Sep. 05, 2023. [Online]. Available: View Article
[14] M. Chkhachirou, T. El-Maaddawy, and H. El-Hassan, "Effect of Temperature on Basalt Fiber Reinforced Polymer Bars in Moist Geopolymer Concrete," presented at the The 9th International Conference on Civil, Structural and Transportation Engineering, Jun. 2024. doi: 10.11159/iccste24.183. View Article
[15] M. Abughali, T. El-Maaddawy, and H. El-Hassan, "Properties of Geopolymer Concrete Made With Recycled Concrete Aggregates and Glass Fibers," presented at the The 9th International Conference on Civil, Structural and Transportation Engineering, Jun. 2024. doi: 10.11159/iccste24.199. View Article
[16] H. El-Hassan and N. Ismail, "Effect of process parameters on the performance of fly ash/GGBS blended geopolymer composites," Journal of Sustainable Cement-Based Materials, vol. 7, no. 2, pp. 122-140, Mar. 2018, doi: 10.1080/21650373.2017.1411296. View Article
[17] H. El-Hassan and S. Elkholy, "Enhancing the performance of Alkali-Activated Slag-Fly ash blended concrete through hybrid steel fiber reinforcement," Construction and Building Materials, vol. 311, p. 125313, Dec. 2021, doi: 10.1016/j.conbuildmat.2021.125313. View Article
[18] H. Wang, X. Zhao, T. Wang, L. Su, B. Zhou, and Y. Lin, "Determination of Gel Products in Alkali-Activated Fly Ash-Based Composites Incorporating Inorganic Calcium Additives," Advances in Materials Science and Engineering, vol. 2022, pp. 1-13, Feb. 2022, doi: 10.1155/2022/7476671. View Article
[19] I. Garcia-Lodeiro, A. Palomo, A. Fernández-Jiménez, and D. E. Macphee, "Compatibility studies between N-A-S-H and C-A-S-H gels. Study in the ternary diagram Na2O-CaO-Al2O3-SiO2-H2O," Cement and Concrete Research, vol. 41, no. 9, pp. 923-931, Sep. 2011, doi: 10.1016/j.cemconres.2011.05.006. View Article
[20] C09 Committee, "Standard Test Method for Slump of Hydraulic-Cement Concrete." ASTM International. doi: 10.1520/C0143_C0143M. View Article
[21] C09 Committee, "ASTM C39 / C39M Standard Test Method for Compressive Strength of Cylindrical Concrete Specimens." ASTM International. View Article
[22] L. Nishanth and Dr. N. N. Patil, "Experimental evaluation on workability and strength characteristics of self-consolidating geopolymer concrete based on GGBFS, flyash and alccofine," Materials Today: Proceedings, vol. 59, pp. 51-57, 2022, doi: 10.1016/j.matpr.2021.10.200. View Article
[23] Niyazuddin and U. B, "Mechanical and durability properties of standard and high strength geopolymer concrete using particle packing theory," Construction and Building Materials, vol. 400, p. 132722, Oct. 2023, doi: 10.1016/j.conbuildmat.2023.132722. View Article
[24] D. Hou, M. Zhang, Z. Ma, D. Wu, Q.Song, Q. Zheng, M.Wang, S. Sui, X. Zhang, and Xi.Wang, "Comparative optimization of densified system of ultra-fine particles (DSP) and Horsfield filling toward UHPC fabrication," Cement and Concrete Composites, vol. 144, p. 105267, Nov. 2023, doi: 10.1016/j.cemconcomp.2023.105267. View Article
[25] S. Popovics, "ANALYSIS OF THE INFLUENCE OF WATER CONTENT ON CONSISTENCY".
[26] M. C. Limbachiya, T. Leelawat, and R. K. Dhir, "Use of recycled concrete aggregate in high-strength concrete," Mat. Struct., vol. 33, no. 9, pp. 574-580, Nov. 2000, doi: 10.1007/BF02480538. View Article
[27] P. A. Sivanantham, G. G. Prabhu, G. G. Vimal Arokiaraj, and K. Sunil, "Effect of Fibre Aspect-Ratio on the Fresh and Strength Properties of Steel Fibre Reinforced Self-Compacting Concrete," Advances in Materials Science and Engineering, vol. 2022, pp. 1-8, May 2022, doi: 10.1155/2022/1207273. View Article
[28] A. Alrawashdeh and O. Eren, "Mechanical and physical characterisation of steel fibre reinforced self-compacting concrete: Different aspect ratios and volume fractions of fibres," Results in Engineering, vol. 13, p. 100335, Mar. 2022, doi: 10.1016/j.rineng.2022.100335. View Article
[29] U. Sharma N. Gupta, A. Bahrami, Y.O. Özkılıç, M. Verma, P. Berwal, E. Althaqafi, M.A. Khan, and S. Islam, "Behavior of Fibers in Geopolymer Concrete: A Comprehensive Review," Buildings, vol. 14, no. 1, p. 136, Jan. 2024, doi: 10.3390/buildings14010136. View Article
[30] O. Mohamed and H. Zuaiter, "Fresh Properties, Strength, and Durability of Fiber-Reinforced Geopolymer and Conventional Concrete: A Review," Polymers, vol. 16, no. 1, p. 141, Jan. 2024, doi: 10.3390/polym16010141. View Article
[31] C. De Backere, T. De Beer, C. Vervaet, and V. Vanhoorne, "Effect of binder type and lubrication method on the binder efficacy for direct compression," International Journal of Pharmaceutics, vol. 607, p. 120968, Sep. 2021, doi: 10.1016/j.ijpharm.2021.120968. View Article
[32] P. Nuaklong, V. Sata, and P. Chindaprasirt, "Influence of recycled aggregate on fly ash geopolymer concrete properties," Journal of Cleaner Production, vol. 112, pp. 2300-2307, Jan. 2016, doi: 10.1016/j.jclepro.2015.10.109. View Article
[33] F. U. A. Shaikh, "Mechanical and durability properties of fly ash geopolymer concrete containing recycled coarse aggregates," International Journal of Sustainable Built Environment, vol. 5, no. 2, pp. 277-287, Dec. 2016, doi: 10.1016/j.ijsbe.2016.05.009. View Article
[34] S. V. Patankar, S. S. Jamkar, and Y. M. Ghugal, "EFFECT OF WATER-TO-GEOPOLYMER BINDER RATIO ON THE PRODUCTION OF FLY ASH BASED GEOPOLYMER CONCRETE," IJATCE, pp. 296-300, Oct. 2012, doi: 10.47893/IJATCE.2012.1048. View Article
[35] C. Han, J. Pang, S. Hu, and C. Yang, "Study on static and dynamic mechanical properties and microstructure of silica fume-polypropylene fiber modified rubber concrete," Sci Rep, vol. 14, no. 1, p. 12573, May 2024, doi: 10.1038/s41598-024-63341-z. View Article
[36] Y. Zheng, P. Zhang, Y. Cai, Z. Jin, and E. Moshtagh, "Cracking resistance and mechanical properties of basalt fibers reinforced cement-stabilized macadam," Composites Part B: Engineering, vol. 165, pp. 312-334, May 2019, doi: 10.1016/j.compositesb.2018.11.115. View Article
[37] C.-S. Tang, B. Shi, Y.-J. Cui, C. Liu, and K. Gu, "Desiccation cracking behavior of polypropylene fiber-reinforced clayey soil," Can. Geotech. J., vol. 49, no. 9, pp. 1088-1101, Sep. 2012, doi: 10.1139/t2012-067. View Article
[38] Safiuddin, U. J. Alengaram, A. Salam, M. Z. Jumaat, F. F. Jaafar, and H. B. Saad, "Properties of high-workability concrete with recycled concrete aggregate," Mat. Res., vol. 14, no. 2, pp. 248-255, Jun. 2011, doi: 10.1590/S1516-14392011005000039. View Article
[39] Abba Bashir, Chhavi Gupta, M A Abubakar, and S I Abba, "Comparison of Properties of Coarse Aggregate Obtained from Recycled Concrete with that of Conventional Coarse Aggregates." Unpublished, 2018. View Article
[40] Md. H. R. Sobuz, SD. Datta, AS. Akid, VW. Tam, S. Islam, MJ. Rana, F. Aslani, Ç. Yalçınkaya, and NM. Sutan, "Evaluating the effects of recycled concrete aggregate size and concentration on properties of high-strength sustainable concrete," Journal of King Saud University - Engineering Sciences, p. S1018363922000356, Apr. 2022, doi: 10.1016/j.jksues.2022.04.004. View Article