Volume 7 - Year 2024- Pages 138-146
DOI: 10.11159/ijci.2024.014
Behavior of BFRP Bars in Moist Geopolymer Concrete and Alkaline-Exposed Conventional Concrete
Mouaz Chkhachirou1, Hilal EL-Hassan1, Tamer El-Maaddawy1, Mohammed AbuGhali1
United Arab Emirates University
Al Ain, United Arab Emirates
202170150@uaeu.ac.ae; helhassan@uaeu.ac.ae; tamer.maaddawy@uaeu.ac.ae, 202170069@uaeu.ac.ae
Abstract - This research studies the performance of sand-coated basalt fiber reinforced polymer (BFRP) in two different environments under varied temperatures conditioned for 3 months. During the conditioning period, these BFRP specimens were subject to two environmental conditioning schemes: moist geopolymer concrete and alkaline solution simulating the concrete pore solution. The conditioning temperature varied among 20, 40, and 60°C. Both types of concrete were designed with a nominal cylindrical compressive strength of 40 MPa with a slag-to-fly ash mass ratio of 1:3. The tensile strength, moisture uptake, and matrix retention of BFRP bars were measured. Test results highlighted the tensile strength of BFRP bars submerged in moist geopolymer concrete decreased significantly, retaining 68.3%, 47.6%, and 57.9% at 20°C, 40°C, and 60°C, respectively. In contrast, BFRP bars in the alkaline solution showed superior tensile performance with retention of 95.4%, 97.1%, and 91.2% at the same conditioning temperatures. All tested bars in moist geopolymer concrete exhibited higher moisture uptake compared to those in the alkaline solution. At 20°C, the moisture uptake was nearly double in geopolymer concrete, and this trend continued at higher temperatures. This indicates a higher rate of water diffusion in geopolymer concrete, which accelerates degradation mechanisms such as hydrolysis. The matrix retention of BFRP bars was significantly lower in moist geopolymer concrete, especially at elevated temperatures, suggesting greater susceptibility to resin matrix degradation in this environment. These results highlight the crucial influence of the surrounding concrete environment on the long-term performance of BFRP bars
Keywords: Basalt Fiber Reinforced Polymer, Moist Geopolymer Concrete, Alkaline Solution, Tensile Strength, Durability.
© Copyright 2024 Authors - This is an Open Access article published under the Creative Commons Attribution License terms. Unrestricted use, distribution, and reproduction in any medium are permitted, provided the original work is properly cited.
Date Received: 2024-01-18
Date Revised: 2024-07-12
Date Accepted: 2024-07-28
Date Published: 2024-08-16
1. Introduction
Numerous studies have been focusing on sustainable construction by exploring alternative materials for concrete and reinforcement, considering their chemical composition and mechanical performance. These advancements hold the potential to improve environmental sustainability and reduce the risk of concrete structure deterioration. Findings suggest that Geopolymer Concrete (GC) can be a viable replacement for conventional Portland cement concrete [1-3]. The production of concrete significantly impacts our environment by requiring the excessive use of resources, leading to environmental degradation. Its various components, particularly when considering the production of Portland cement, contribute heavily to issues like significant greenhouse gas emissions and high water consumption [4, 5].
Reinforcement corrosion, caused by carbonation, chloride ingress, and acid rain attack, is a major factor in the low durability performance of concrete structures. Corrosive ions, such as chlorides, penetrate the concrete due to carbonation or acid rain attack, breaking down the steel's passive layer and initiating the oxidation process [6]. This corrosion leads to cracking, spalling, and ultimately, a loss of the structure's load-bearing capacity, significantly reducing its service life. The repairs necessitated by reinforcement corrosion cost billions of dollars annually worldwide [6-9]. As a solution, Fiber-reinforced Polymer (FRP) bars offer a promising alternative to traditional steel reinforcement owing to their high strength capacity, thermal resistivity and resistance to corrosion [10-15]. FRP rebars come in various types, including Glass Fiber-reinforced polymer (GFRP), Carbon Fiber-reinforced Polymer (CFRP), and Basalt Fiber-reinforced Polymer (BFRP). BFRP has gained particular interest in recent years due to its low cost, excellent durability in alkaline environments (common in concrete), Fatigue performance, and zero-toxic material composition [16-17]. However, some limitations of BFRP include lower ductility compared to other FRPs, raising concerns about potential sudden failure in concrete structures. This highlights the importance of considering both the benefits and drawbacks of different FRP materials when selecting reinforcement options [19].
Numerous research studies have investigated the performance of BFRP composites in concrete, emphasizing their effectiveness under various conditions. Lu et al. [20] investigated the durability of BFRP bars embedded in concrete at 60°C for 6 months. They found that BFRPs in geopolymer concrete retained 11% more strength compared to those in conventional concrete, highlighting the potential benefits of geopolymer concrete for FRP reinforcement. Al-Hamrani and Alnahhal investigated the effect of seawater immersion on the bond strength of BFRP bars in concrete. They evaluated BFRP bars embedded in concrete specimens exposed to seawater at 50°C for 3, 6, and 9 months. Their results showed that BFRP bars maintained a higher bond strength in conventional concrete compared to those exposed to seawater [21]. Elgabbas et al. [12] quantified the detrimental effect of alkaline solutions on BFRP bars. Their research exposed BFRP bars to a simulated concrete environment and observed a measurable decrease in the bars' mechanical properties. Similarly, Al Rifai et al. [17] investigated the effect of harsh alkaline environments on basalt fiber-reinforced polymer (BFRP) rebar durability. Their study exposed BFRP bars to a simulated concrete pore solution at 60°C for 9 months. The results were concerning, with bars experiencing a significant 29% loss in tensile strength compared to a mere 15% reduction in bars submerged in standard tap water. Mingchao et al. [22] identified the flexural strength of BFRP bars as a more critical property than the flexural modulus when considering the impact of alkaline solution exposure on their performance in concrete structures. This highlights the potential vulnerability of BFRP reinforcement in highly alkaline concrete environments [22-24].
This study investigates the durability of sand-coated basalt fiber-reinforced polymer (BFRP) bars embedded in two concrete types: conventional Portland Cement Concrete (PCC) and slag-fly ash blended Geopolymer Concrete (GC). To assess the impact of the environment, PCC specimens are conditioned in an alkaline solution while GC specimens are submerged in tap water. After 3 months of immersion concrete at varying temperatures (20°, 40°C, and 60°C), evaluation included the tensile strength property of the BFRP bars. To understand the deterioration mechanisms, their moisture uptake and matrix composition analysis were done.
2. Experimental Program
2. 1. Materials
This experiment evaluated the performance of two different sizes of sand-coated basalt fiber-reinforced polymer (BFRP) rebar. Both rebars were manufactured using basalt fibers impregnated with epoxy resin. The nominal diameters were 10 mm and 12 mm, with the larger diameter (12 mm) rebar immersed in saturated geopolymer concrete and the smaller diameter (10 mm) rebar exposed to an alkaline solution. Following the procedures outlined in ACI 440.3R [26], the average cross-sectional area of the BFRP rebars was determined to be 94 mm² and 121 mm² for the 10 mm and 12 mm diameter rebars, respectively. This measurement is crucial for calculating the tensile load capacity of the rebars and ensuring they meet design requirements. To quantify the Fiber content by weight, the BFRP bars underwent matrix digestion using nitric acid (HNO3) as specified in ASTM D3171 [27]. This process dissolves the epoxy resin, leaving behind the isolated basalt fibers. The analysis revealed a fiber mass fraction of 74.5%. A high fiber content is desirable in BFRP rebars as it directly contributes to their tensile strength and stiffness. Finally, the void content was found to be 0.24% according to ASTM D3171 and D2734 [26, 27]. Voids within the BFRP composite can act as stress concentrators and potentially weaken the rebar. A low void content ensures a more uniform distribution of stress throughout the fiber-matrix interface, leading to improved mechanical performance.
Two concrete mixtures were prepared to evaluate the performance of BFRP rebar under different environments. The first concrete type was geopolymer concrete, formulated for enhanced durability. The geopolymer binder consisted of a 3:1 blend of Ground Granulated Blast Furnace Slag (GGBS) and Fly Ash (FA), activated by a 14 M sodium hydroxide (NaOH) solution at a 1.5:1 liquid-to-binder ratio [5]. This combination promotes a strong reaction that forms a highly alkaline, aluminosilicate gel matrix. Coarse aggregates for the geopolymer concrete were crushed dolomitic limestone with a 10 mm maximum size, while desert dune sand served as the fine aggregate. In contrast, the second concrete type was a commercially available ready-mix concrete containing Ordinary Portland Cement (OPC) conforming to ASTM Type I. Both concrete mixes were designed to achieve a target compressive strength of 40 MPa. After thorough mixing, casting, and compaction, the concrete specimens underwent testing to assess various performance characteristics, including compressive strength, split tensile strength, Ultrasonic Pulse Velocity (UPV), and pH value as per ASTM C39 [29], ASTM C496 [30], ASTM C597 [31] and ASTM E70-07[32], respectively. The properties of each type of concrete are summarized in Table 1.
Table 1. Surrounding concrete properties
Test |
Portland Cement Concrete |
Geopolymer Concrete |
Unit |
Standard |
Area |
94.3 |
121.3 |
mm |
ACI 440.3R [26] |
Compressive Strength |
46.7 |
37.5 |
MPa |
ASTM C39 [29] |
Split Tensile Strength |
3.2 |
3.1 |
MPa |
ASTM C496 [30] |
UPV |
4.8 |
4.7 |
Km/s |
ASTM C597 [31] |
pH |
12.5 |
11.4 |
- |
ASTM E70-07[32] |
Following initial characterization, the concrete specimens were subjected to different conditioning environments. Geopolymer concrete specimens were submerged in a saturated geopolymer concrete environment, closely representing the internal pore solution of the material. Meanwhile, Portland cement concrete specimens were immersed in an alkaline solution with a higher pH of 12.1, representing a more aggressive alkaline environment compared to the geopolymer concrete's internal pore solution (pH 8.8). This variation in pH levels allows us to investigate the potential impact of different alkaline environments on the durability of BFRP rebar embedded within each concrete type.
2. 2. Preparation of specimens
Eighteen concrete specimens were prepared, nine for each concrete type. Each specimen had a total length of 1200 mm to simulate realistic embedment lengths encountered in practice. The sand-coated BFRP rebars (shown in Figure 1) consisted of two nominal sizes, the larger diameter (12 mm) BFRP rebar BFRP was embedded 480 mm within the GC specimen, while the smaller diameter (10 mm) rebar was embedded 400 mm within the PCC specimen. The remaining lengths on either side of the embedded sections were used to install steel grips for subsequent tensile strength testing as per standard testing procedures. The concrete prism dimensions were designed with a length 40 times the diameter of the BFRP rebar as per ACI 440.4R [26]. The BFRP rebars were cast within concrete prisms having a square cross-section of 50 mm x 50 mm. These dimensions ensure a proper stress distribution during testing. After casting, the specimens were allowed to harden under controlled conditions. To achieve proper curing, they were wrapped in cloths and kept moist by regular spraying with potable water for 28 days. Following this initial curing period, the specimens were transferred to a natural environment until the conditioning tanks were prepared for testing.
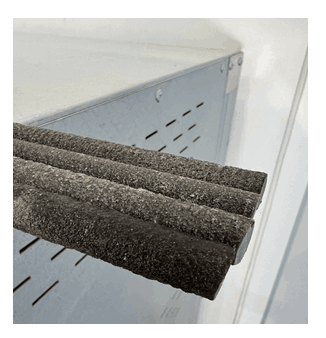
The actual conditioning phase involved immersing the specimens in a moist environment for 3 months at three different temperatures: 20°C, 40°C, and 60°C. Six conditioning tanks were utilized to accommodate these varying temperatures. Stainless steel tanks were used for PCC specimens submerged in the alkaline solution, while fiberglass high-resistance tanks were used for GC specimens. To ensure proper isolation and maintain the desired temperatures, each set of three tanks (one for each temperature) was independent. For the PCC specimens, an alkaline solution with a pH matching the internal pore water of concrete was prepared. This solution was achieved by adding and thoroughly mixing 40 g/L of sodium hydroxide (NaOH) with water. High-quality thermostats were installed in each tank to precisely control the conditioning temperatures. Water levels were monitored and adjusted regularly to maintain consistent testing conditions. Additionally, thermostats were replaced periodically if necessary, throughout the experiment period. Polyvinyl Chloride (PVC) pipes were installed on both sides of the embedded BFRP rebar sections within each specimen to isolate the BFRP bars effectively within the conditioned solutions. These PVC pipes were filled with a universal multi-foam material to create a physical barrier between the bars and the surrounding conditioning solution. Finally, the open ends of the PVC pipes were sealed with impermeable plastic covers to prevent any leakage or contamination.
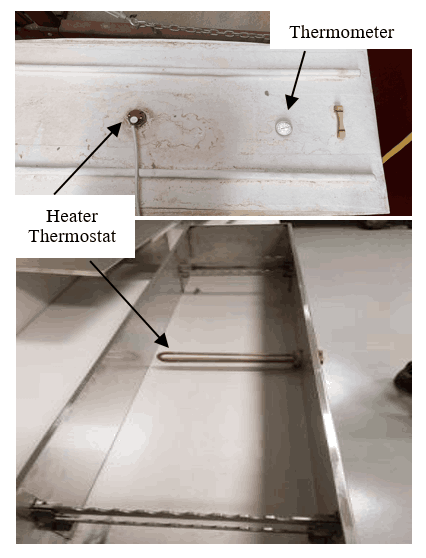
2.3 Performance Evaluation
Following the 3-month conditioning period, the BFRP rebars were extracted from tanks, and concrete was removed. a standardized testing procedure outlined in ACI 440.3R-04 [26] was employed to evaluate the tensile strength after exposure to different environments and temperatures. Specially designed steel grips were crucial for this test. These grips were designed with a 50 mm outer diameter, 400 mm length, and 1.5 mm thickness and ensured safe and efficient load transfer from the tensile testing machine to the BFRP rebars. The inner surface of the grips was roughened to enhance epoxy adhesion along the entire 400 mm length and to achieve a strong and reliable connection. After applying epoxy and allowing it to cure for 24 hours, the BFRP rebars were secured within the grips for testing. The test involved applying a uniaxial tensile load at a controlled displacement rate of 1.5 mm/minute until failure. The recorded load data was used to calculate the tensile strength by dividing the maximum load by the BFRP rebar's cross-sectional area. In addition to tensile strength, the moisture uptake of the BFRP rebars was evaluated following the completion of the conditioning phase. This test, conducted according to ASTM D570 [33]. This code allowed assessing the amount of moisture absorbed by the BFRP specimens at each temperature (20°C, 40°C, and 60°C). BFRP rebars were dried in an oven at 100°C for 24 hours before testing for eliminating any potential mass loss from the specimens. The fiber and matrix contents were analyzed using a matrix digestion technique specified in ASTM D3171 [27] for more insights into the potential degradation mechanisms of the BFRP rebars under different conditions. This test involved mixing a sample of BFRP material (0.5-1.5 g) with 50 mL of a 70% nitric acid solution. The resulting mixture was then subjected to a controlled temperature of 80°C within a heated container for 6 hours. This elevated temperature facilitated a chemical reaction that dissolved the epoxy resin within the BFRP composite. Following this process, the mixture was washed with distilled water and oven-dried at 100°C for 1 hour to remove any remaining moisture before further analysis. Analyzing the residuals after digestion provides the relative proportions of fiber and matrix within the BFRP rebars. Potentially revealing how these components were affected by the different conditioning environments.
3. Experimental Results
3. 1. Tensile Strength
To identify potential correlations between tensile strength and environmental conditions, the specimens were designated with a code "XX-Y," where "XX" represents the concrete type (GC for geopolymer concrete and PCC for Portland cement concrete) and "Y" represents the immersion environment (W for moist geopolymer concrete and A for alkaline solution). Figure 3 presents the tensile strength of BFRP rebars after exposure to different environments for 3 months. Compared to the control specimens, all conditioned rebars exhibited different drops in tensile strength values. Notably, BFRP rebars embedded in moist geopolymer concrete (GC) displayed a progressive reduction in tensile strength with increasing temperature. At 20°C, 40°C, and 60°C, these rebars retained only 68.3%, 47.6%, and 57.9% of their original strength, respectively. In contrast, BFRP rebars conditioned in the alkaline solution of Portland cement concrete demonstrated superior performance. These rebars experienced minimal strength reduction across all temperatures, with strength retention of 95.4%, 97.1%, and 91.2%, respectively, compared to the control group for all the temperatures as per Table 2. Notably, the highest strength (1232 MPa) was observed at 40°C, with minimal further change at 60°C. This suggests that the alkaline solution environment within Portland cement concrete may offer some protection for BFRP rebars against the detrimental effects of temperature.
These findings emphasize the significant influence of the surrounding concrete and the type of conditioning environment on the BFRP rebars' response to elevated temperatures [33, 34]. While increasing temperature from 20°C to 40°C negatively impacts the strength of rebars in moist geopolymer concrete, those embedded in the alkaline solution of Portland cement concrete appear less susceptible. This behaviour aligns with El-Hassan et al. [36] research suggests that temperature can accelerate hydrolysis degradation mechanisms within BFRP composites, particularly when water diffusion is high. For both types of environments, the specimens submerged at higher temperatures (60°C) experienced more disintegration in the bonds between fiber and matrix which resulted higher separation rate to those submerged at (20°C) temperature. These findings corroborate Lu et al. [23] conclusion that the tensile strength of BFRP is heavily reliant on fiber integrity. The contrasting performance in tensile strength of BFRP rebars in these environments emphasizes the need for careful consideration of the concrete type, environment media, and the potential service temperature when selecting the proper BFRP reinforcement for concrete structures. Consideration of the potential service temperature is paramount, as elevated temperatures have been shown to accelerate degradation mechanisms within the BFRP composite.
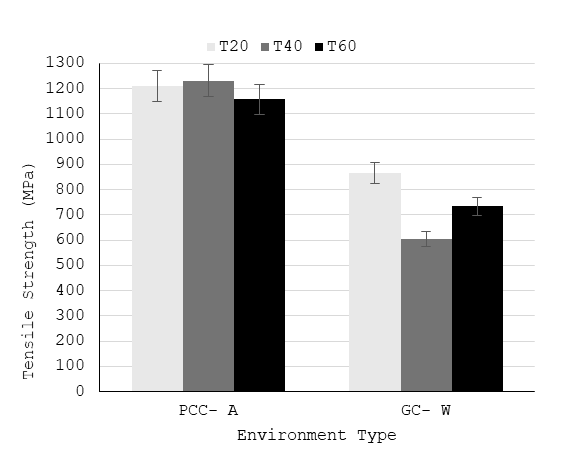
Table 2. BFRP tensile strength retention analysis
Environment |
Surrounding concrete |
Conditioning temperature (oC) |
Tensile Strength |
Tensile retention % |
Error % |
Control |
1268.0 ± 15.2 |
0 |
1.3 |
||
Tap water |
Geopolymer Concrete |
20 |
866.2 ± 20.4 |
68.3 |
2.4 |
40 |
604.6 ± 28.7 |
47.6 |
4.7 |
||
60 |
734.1 ± 54.5 |
57.9 |
7.6 |
||
Alkaline solution |
Portland Cement Concrete |
20 |
1210.9 ± 25.3 |
95.4 |
2.1 |
40 |
1232.1 ± 27.9 |
97.1 |
1.9 |
||
60 |
1157.5 ± 12.8 |
91.2 |
1.1 |
3.2 Moisture Uptake
The inherent porosity of concrete, regardless of type (geopolymer or Portland cement concrete), allows for water absorption from the surrounding environment. This absorbed moisture can potentially contribute to the deterioration of BFRP rebars through existing microcracks within the concrete mixture. As depicted in Figure 3, the moisture uptake data for the conditioned BFRP rebars differs. Interestingly, the average moisture uptake across all three temperatures (20°C, 40°C, and 60°C) remained below 1% for both concrete types. However, a notable trend emerged: BFRP rebars embedded in moist geopolymer concrete (GC-W) consistently exhibited higher moisture uptake compared to those in the alkaline solution of Portland cement concrete (PCC-A). At 20°C, the moisture uptake in GC-W specimens was nearly double that of PCC-A specimens (0.39% compared to 0.19%). This difference became even more pronounced at 40°C, with GC-W specimens showing a 61% increase in moisture uptake compared to PCC-A specimens. Finally, at 60°C, the moisture uptake remained higher in GC-W specimens. These observations suggest that the type of conditioning environment significantly impacts the water absorption behavior of BFRP rebars. The higher temperatures may have contributed to an increased water diffusion rate within the geopolymer concrete, potentially expanding existing microcracks and facilitating greater moisture ingress into the BFRP rebars. This increased moisture uptake, coupled with the elevated temperatures, could potentially accelerate degradation mechanisms within the BFRP composite, such as hydrolysis, which can weaken the fiber-matrix interface and compromise the overall performance of the rebar [35]. These findings provide a compelling explanation for the observed correlation between the observed reduction in tensile strength and the elevated moisture absorption, particularly at 40°C and 60°C. The deterioration of the fiber-matrix interface, exacerbated by increased moisture ingress at higher temperatures, likely contributed to a reduction in the load-bearing capacity of the BFRP rebars. Consequently, the BFRP rebars exhibited diminished resistance to tensile forces under these conditions.
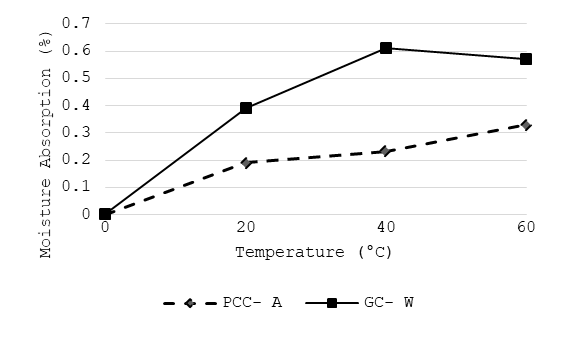
3.3 Matrix Digestion Analysis
Table 3 presents the results of the matrix digestion test, which provides insights into the potential degradation of the epoxy resin matrix within the BFRP rebars under different conditioning environments. The analysis focused on the mass content of the remaining matrix and the corresponding fiber content after the digestion process.
Table 3. Matrix digestion analysis for the specimens
Specimen Designation |
Conditioning temperature (oC) |
Content (%) |
Matrix retention % |
Matrix loss % |
|
Fiber |
Matrix |
||||
Control |
74.6 |
25.4 |
- |
- |
|
GC- W |
20 |
79.3 |
20.7 |
81 |
19 |
40 |
86.3 |
13.7 |
54 |
46 |
|
60 |
82.4 |
17.6 |
69 |
31 |
|
PCC-A |
20 |
81 |
19 |
75.5 |
24.5 |
40 |
82.3 |
17.7 |
69.4 |
30.6 |
|
60 |
84.7 |
15.3 |
60 |
40 |
At 20°C, the matrix content of BFRP rebars exposed to both moist geopolymer concrete and alkaline solution environments showed a minimal difference. In both cases, the matrix loss was around 20% with a corresponding fiber content exceeding 79%. This suggests that at this relatively low temperature, neither environment significantly affected the integrity of the epoxy matrix. However, a concerning trend emerged at higher temperatures. BFRP rebars embedded in the GC environment exhibited a more pronounced decrease in matrix content than those in the PCC environment. At 40°C, the GC specimens displayed a 16% higher matrix loss compared to their PCC counterparts. This suggests that the geopolymer concrete environment might be more aggressive towards the epoxy resin at this temperature, potentially leading to accelerated hydrolysis or other degradation mechanisms [37]. Interestingly, the matrix in the GC specimens was retained more than in the PCC environment at 60°C, indicating a less substantial degradation of the epoxy matrix in the GC. In contrast, the BFRP rebars in the alkaline solution of PCC showed a slight increase in fiber content at 60°C compared to lower temperatures. This could be attributed to the dissolution of the remaining, potentially degraded, epoxy matrix, revealing a higher proportion of fibers. These observations align with previous research on GFRP bars exposed to moist seawater-contaminated concrete [35], which also reported accelerated degradation of the polymer matrix at elevated temperatures. The increased temperature could enhance the water diffusion rate within the geopolymer concrete. Potentially, this enhanced moisture ingress could have promoted hydrolytic degradation of the epoxy resin at the fiber-matrix interface. The resulting hydrolysis products may have weakened the interfacial bond, thereby compromising the load-transfer capacity of the composite and ultimately contributing to the observed reduction in tensile strength.
4. Conclusions
This study has provided a comprehensive comparison of the performance of basalt fiber-reinforced polymer (BFRP) bars in moist geopolymer concrete and in an alkaline solution environment typical of Portland cement concrete. The findings indicate that BFRP bars exhibit a notable variation in tensile strength, moisture uptake, and matrix retention when subjected to different temperatures and environmental conditions. BFRP bars embedded in moist geopolymer concrete exhibited a substantial reduction in tensile strength with increasing temperature, retaining only 68.3%, 47.6%, and 57.9% of their original strength at 20°C, 40°C, and 60°C, respectively. In contrast, those conditioned in the alkaline solution of Portland cement concrete demonstrated minimal strength reduction, retaining over 90% of their original tensile strength across all tested temperatures. The BFRP bars in moist geopolymer concrete consistently showed higher moisture uptake compared to those in the alkaline solution. At 20°C, the moisture uptake in geopolymer concrete was nearly double that of Portland cement concrete, and this trend was even more pronounced at higher temperatures. This increased moisture uptake in geopolymer concrete is likely due to higher water diffusion rates, which can accelerate degradation mechanisms such as hydrolysis. The matrix retention of BFRP bars was significantly lower in moist geopolymer concrete, especially at higher temperatures. This suggests that the resin matrix of BFRP bars is more susceptible to degradation in a moist geopolymer environment, leading to a greater loss of mechanical integrity.
Acknowledgments
This research is funded by the United Arab Emirates University and the authors acknowledge the financial support this support under grant 12N115.
References
[1] A. L. Almutairi, B. A. Tayeh, A. Adesina, H. F. Isleem, and A. M. Zeyad, "Potential applications of geopolymer concrete in construction: A review," Case Stud. Constr. Mater., vol. 15, p. e00733, Dec. 2021, doi: 10.1016/j.cscm.2021.e00733.
View Article
[2] S. Astutiningsih, D. M. Nurjaya, H. W. Ashadi, and N. Swastika, "Durability of Geopolymer Concretes upon Seawater Exposure," presented at the Geopolymers and Geocements: Low Environmentally Impact Ceramic Materials, Oct. 2010, pp. 92-96. doi: 10.4028/www.scientific.net/AST.69.92.
View Article
[3] N. Gupta, A. Gupta, K. K. Saxena, A. Shukla, and S. K. Goyal, "Mechanical and durability properties of geopolymer concrete composite at varying superplasticizer dosage," Mater. Today Proc., vol. 44, pp. 12-16, 2021, doi: 10.1016/j.matpr.2020.05.646.
View Article
[4] B. Afkhami, B. Akbarian, N. Beheshti A., A. H. Kakaee, and B. Shabani, "Energy consumption assessment in a cement production plant," Sustain. Energy Technol. Assess., vol. 10, pp. 84-89, Jun. 2015, doi: 10.1016/j.seta.2015.03.003.
View Article
[5] M. Abughali, H. El-Hassan, and T. El-Maaddawy, "Properties of Geopolymer Concrete Made With Recycled Concrete Aggregates and Glass Fibers".
[6] S. Ahmad, "Reinforcement corrosion in concrete structures, its monitoring and service life prediction--a review," Cem. Concr. Compos., vol. 25, no. 4-5, pp. 459-471, May 2003, doi: 10.1016/S0958-9465(02)00086-0.
View Article
[7] R. R. Hussain, A. Al-Negheimish, A. Alhozaimy, and D. D. N. Singh, "Corrosion characteristics of vanadium micro-alloyed steel reinforcement bars exposed in concrete environments and industrially polluted atmosphere," Cem. Concr. Compos., vol. 113, p. 103728, Oct. 2020, doi: 10.1016/j.cemconcomp.2020.103728.
View Article
[8] F. Yan, Z. Lin, and M. Yang, "Bond mechanism and bond strength of GFRP bars to concrete: A review," Compos. Part B Eng., vol. 98, pp. 56-69, Aug. 2016, doi: 10.1016/j.compositesb.2016.04.068.
View Article
[9] G. K. Glass and N. R. Buenfeld, "Chloride-induced corrosion of steel in concrete," Prog. Struct. Eng. Mater., vol. 2, no. 4, pp. 448-458, 2000, doi: 10.1002/pse.54.
View Article
[10] M. Quraishi, D. Nayak, R. Kumar, and V. Kumar, "Corrosion of Reinforced Steel in Concrete and Its Control: An overview," J. Steel Struct. Constr., vol. 03, no. 01, 2017, doi: 10.4172/2472-0437.1000124.
View Article
[11] M. R. Irshidat, M. H. Al-Saleh, and M. Al-Shoubaki, "Using carbon nanotubes to improve strengthening efficiency of carbon fiber/epoxy composites confined RC columns," Compos. Struct., vol. 134, pp. 523-532, Dec. 2015, doi: 10.1016/j.compstruct.2015.08.108.
View Article
[12] F. Elgabbas, E. A. Ahmed, and B. Benmokrane, "Physical and mechanical characteristics of new basalt-FRP bars for reinforcing concrete structures," Constr. Build. Mater., vol. 95, pp. 623-635, Oct. 2015, doi: 10.1016/j.conbuildmat.2015.07.036.
View Article
[13] F. Abed and A. R. Alhafiz, "Effect of basalt fibers on the flexural behavior of concrete beams reinforced with BFRP bars," Compos. Struct., vol. 215, pp. 23-34, May 2019, doi: 10.1016/j.compstruct.2019.02.050.
View Article
[14] V. Dhand, G. Mittal, K. Y. Rhee, S.-J. Park, and D. Hui, "A short review on basalt fiber reinforced polymer composites," Compos. Part B Eng., vol. 73, pp. 166-180, May 2015, doi: 10.1016/j.compositesb.2014.12.011.
View Article
[15] P. Ghosh, N. R. Bose, B. C. Mitra, and S. Das, "Dynamic mechanical analysis of FRP composites based on different fiber reinforcements and epoxy resin as the matrix material," J. Appl. Polym. Sci., vol. 64, no. 12, pp. 2467-2472, Jun. 1997, doi: 10.1002/(SICI)1097-4628(19970620)64:12<2467::AID-APP21>3.0.CO;2-X.
View Article
[16] Y. Pan and D. Yan, "Study on the durability of GFRP bars and carbon/glass hybrid fiber reinforced polymer (HFRP) bars aged in alkaline solution," Compos. Struct., vol. 261, p. 113285, Apr. 2021, doi: 10.1016/j.compstruct.2020.113285.
View Article
[17] M. A. Rifai, H. El-Hassan, T. El-Maaddawy, and F. Abed, "Durability of basalt FRP reinforcing bars in alkaline solution and moist concrete environments," Constr. Build. Mater., vol. 243, p. 118258, May 2020, doi: 10.1016/j.conbuildmat.2020.118258.
View Article
[18] G. Wu, Z.-Q. Dong, X. Wang, Y. Zhu, and Z.-S. Wu, "Prediction of Long-Term Performance and Durability of BFRP Bars under the Combined Effect of Sustained Load and Corrosive Solutions," J. Compos. Constr., vol. 19, no. 3, p. 04014058, Jun. 2015, doi: 10.1061/(ASCE)CC.1943-5614.0000517.
View Article
[19] M. Chkhachirou, H. El-Hassan, and T. El-Maaddawy, "Effect of Temperature on Basalt Fiber Reinforced Polymer Bars in Moist Geopolymer Concrete," Jun. 2024, doi: 10.11159/iccste24.183.
View Article
[20] Z. Lu, L. Su, J. Lai, J. Xie, and B. Yuan, "Bond durability of BFRP bars embedded in concrete with fly ash in aggressive environments," Compos. Struct., vol. 271, p. 114121, Sep. 2021, doi: 10.1016/j.compstruct.2021.114121.
View Article
[21] A. Al-Hamrani and W. Alnahhal, "Bond durability performance of sand-coated BFRP bars in high-strength fiber reinforced concrete," Compos. Struct., vol. 321, p. 117306, Oct. 2023, doi: 10.1016/j.compstruct.2023.117306.
View Article
[22] Wang Mingchao, Zhang Zuoguang, Li Yubin, Li Min, and Sun Zhijie, "Chemical Durability and Mechanical Properties of Alkali-proof Basalt Fiber and its Reinforced Epoxy Composites," J. Reinf. Plast. Compos., vol. 27, no. 4, pp. 393-407, Mar. 2008, doi: 10.1177/0731684407084119.
View Article
[23] Z. Lu, G. Xian, and H. Li, "Effects of exposure to elevated temperatures and subsequent immersion in water or alkaline solution on the mechanical properties of pultruded BFRP plates," Compos. Part B Eng., vol. 77, pp. 421-430, Aug. 2015, doi: 10.1016/j.compositesb.2015.03.066.
View Article
[24] S. Li et al., "Transverse low-velocity impact performance of BFRP bars after exposure to the saline-alkaline environment," Constr. Build. Mater., vol. 307, p. 124650, Nov. 2021, doi: 10.1016/j.conbuildmat.2021.124650.
View Article
[25] M. Hassan, B. Benmokrane, A. ElSafty, and A. Fam, "Bond durability of basalt-fiber-reinforced-polymer (BFRP) bars embedded in concrete in aggressive environments," Compos. Part B Eng., vol. 106, pp. 262-272, Dec. 2016, doi: 10.1016/j.compositesb.2016.09.039.
View Article
[26] "440.3R-04 Guide Test Methods for Fiber-Reinforced Polymers (FRPs) for Reinforcing or Strengthening Concrete Structures".
[27] D30 Committee, "Test Methods for Constituent Content of Composite Materials," ASTM International. doi: 10.1520/D3171-22.
View Article
[28] D20 Committee, "Test Methods for Void Content of Reinforced Plastics," ASTM International. doi: 10.1520/D2734-23.
View Article
[29] C09 Committee, Test Method for Compressive Strength of Cylindrical Concrete Specimens. doi: 10.1520/C0039_C0039M-23.
View Article
[30] C09 Committee, "Test Method for Splitting Tensile Strength of Cylindrical Concrete Specimens," ASTM International. doi: 10.1520/C0496_C0496M-17.
View Article
[31] C09 Committee, "Test Method for Pulse Velocity Through Concrete," ASTM International. doi: 10.1520/C0597-22.
View Article
[32] D16 Committee, Test Method for pH of Aqueous Solutions With the Glass Electrode. doi: 10.1520/E0070-24.
View Article
[33] D20 Committee, "Test Method for Water Absorption of Plastics," ASTM International. doi: 10.1520/D0570-22.
View Article
[34] C. N. Morales, G. Claure, A. R. Emparanza, and A. Nanni, "Durability of GFRP reinforcing bars in seawater concrete," Constr. Build. Mater., vol. 270, p. 121492, Feb. 2021, doi: 10.1016/j.conbuildmat.2020.121492.
View Article
[35] H. El-Hassan, T. El-Maaddawy, A. Al-Sallamin, and A. Al-Saidy, "Performance evaluation and microstructural characterization of GFRP bars in seawater-contaminated concrete," Constr. Build. Mater., vol. 147, pp. 66-78, Aug. 2017, doi: 10.1016/j.conbuildmat.2017.04.135.
View Article
[36] H. El-Hassan, T. El-Maaddawy, A. Al-Sallamin, and A. Al-Saidy, "Durability of glass fiber-reinforced polymer bars conditioned in moist seawater-contaminated concrete under sustained load," Constr. Build. Mater., vol. 175, pp. 1-13, Jun. 2018, doi: 10.1016/j.conbuildmat.2018.04.107.
View Article
[37] O. A. Mohamed, W. Al Hawat, and M. Keshawarz, "Durability and Mechanical Properties of Concrete Reinforced with Basalt Fiber-Reinforced Polymer (BFRP) Bars: Towards Sustainable Infrastructure," Polymers, vol. 13, no. 9, p. 1402, Apr. 2021, doi: 10.3390/polym13091402.
View Article
[1] A. L. Almutairi, B. A. Tayeh, A. Adesina, H. F. Isleem, and A. M. Zeyad, "Potential applications of geopolymer concrete in construction: A review," Case Stud. Constr. Mater., vol. 15, p. e00733, Dec. 2021, doi: 10.1016/j.cscm.2021.e00733. View Article
[2] S. Astutiningsih, D. M. Nurjaya, H. W. Ashadi, and N. Swastika, "Durability of Geopolymer Concretes upon Seawater Exposure," presented at the Geopolymers and Geocements: Low Environmentally Impact Ceramic Materials, Oct. 2010, pp. 92-96. doi: 10.4028/www.scientific.net/AST.69.92. View Article
[3] N. Gupta, A. Gupta, K. K. Saxena, A. Shukla, and S. K. Goyal, "Mechanical and durability properties of geopolymer concrete composite at varying superplasticizer dosage," Mater. Today Proc., vol. 44, pp. 12-16, 2021, doi: 10.1016/j.matpr.2020.05.646. View Article
[4] B. Afkhami, B. Akbarian, N. Beheshti A., A. H. Kakaee, and B. Shabani, "Energy consumption assessment in a cement production plant," Sustain. Energy Technol. Assess., vol. 10, pp. 84-89, Jun. 2015, doi: 10.1016/j.seta.2015.03.003. View Article
[5] M. Abughali, H. El-Hassan, and T. El-Maaddawy, "Properties of Geopolymer Concrete Made With Recycled Concrete Aggregates and Glass Fibers".
[6] S. Ahmad, "Reinforcement corrosion in concrete structures, its monitoring and service life prediction--a review," Cem. Concr. Compos., vol. 25, no. 4-5, pp. 459-471, May 2003, doi: 10.1016/S0958-9465(02)00086-0. View Article
[7] R. R. Hussain, A. Al-Negheimish, A. Alhozaimy, and D. D. N. Singh, "Corrosion characteristics of vanadium micro-alloyed steel reinforcement bars exposed in concrete environments and industrially polluted atmosphere," Cem. Concr. Compos., vol. 113, p. 103728, Oct. 2020, doi: 10.1016/j.cemconcomp.2020.103728. View Article
[8] F. Yan, Z. Lin, and M. Yang, "Bond mechanism and bond strength of GFRP bars to concrete: A review," Compos. Part B Eng., vol. 98, pp. 56-69, Aug. 2016, doi: 10.1016/j.compositesb.2016.04.068. View Article
[9] G. K. Glass and N. R. Buenfeld, "Chloride-induced corrosion of steel in concrete," Prog. Struct. Eng. Mater., vol. 2, no. 4, pp. 448-458, 2000, doi: 10.1002/pse.54. View Article
[10] M. Quraishi, D. Nayak, R. Kumar, and V. Kumar, "Corrosion of Reinforced Steel in Concrete and Its Control: An overview," J. Steel Struct. Constr., vol. 03, no. 01, 2017, doi: 10.4172/2472-0437.1000124. View Article
[11] M. R. Irshidat, M. H. Al-Saleh, and M. Al-Shoubaki, "Using carbon nanotubes to improve strengthening efficiency of carbon fiber/epoxy composites confined RC columns," Compos. Struct., vol. 134, pp. 523-532, Dec. 2015, doi: 10.1016/j.compstruct.2015.08.108. View Article
[12] F. Elgabbas, E. A. Ahmed, and B. Benmokrane, "Physical and mechanical characteristics of new basalt-FRP bars for reinforcing concrete structures," Constr. Build. Mater., vol. 95, pp. 623-635, Oct. 2015, doi: 10.1016/j.conbuildmat.2015.07.036. View Article
[13] F. Abed and A. R. Alhafiz, "Effect of basalt fibers on the flexural behavior of concrete beams reinforced with BFRP bars," Compos. Struct., vol. 215, pp. 23-34, May 2019, doi: 10.1016/j.compstruct.2019.02.050. View Article
[14] V. Dhand, G. Mittal, K. Y. Rhee, S.-J. Park, and D. Hui, "A short review on basalt fiber reinforced polymer composites," Compos. Part B Eng., vol. 73, pp. 166-180, May 2015, doi: 10.1016/j.compositesb.2014.12.011. View Article
[15] P. Ghosh, N. R. Bose, B. C. Mitra, and S. Das, "Dynamic mechanical analysis of FRP composites based on different fiber reinforcements and epoxy resin as the matrix material," J. Appl. Polym. Sci., vol. 64, no. 12, pp. 2467-2472, Jun. 1997, doi: 10.1002/(SICI)1097-4628(19970620)64:12<2467::AID-APP21>3.0.CO;2-X. View Article
[16] Y. Pan and D. Yan, "Study on the durability of GFRP bars and carbon/glass hybrid fiber reinforced polymer (HFRP) bars aged in alkaline solution," Compos. Struct., vol. 261, p. 113285, Apr. 2021, doi: 10.1016/j.compstruct.2020.113285. View Article
[17] M. A. Rifai, H. El-Hassan, T. El-Maaddawy, and F. Abed, "Durability of basalt FRP reinforcing bars in alkaline solution and moist concrete environments," Constr. Build. Mater., vol. 243, p. 118258, May 2020, doi: 10.1016/j.conbuildmat.2020.118258. View Article
[18] G. Wu, Z.-Q. Dong, X. Wang, Y. Zhu, and Z.-S. Wu, "Prediction of Long-Term Performance and Durability of BFRP Bars under the Combined Effect of Sustained Load and Corrosive Solutions," J. Compos. Constr., vol. 19, no. 3, p. 04014058, Jun. 2015, doi: 10.1061/(ASCE)CC.1943-5614.0000517. View Article
[19] M. Chkhachirou, H. El-Hassan, and T. El-Maaddawy, "Effect of Temperature on Basalt Fiber Reinforced Polymer Bars in Moist Geopolymer Concrete," Jun. 2024, doi: 10.11159/iccste24.183. View Article
[20] Z. Lu, L. Su, J. Lai, J. Xie, and B. Yuan, "Bond durability of BFRP bars embedded in concrete with fly ash in aggressive environments," Compos. Struct., vol. 271, p. 114121, Sep. 2021, doi: 10.1016/j.compstruct.2021.114121. View Article
[21] A. Al-Hamrani and W. Alnahhal, "Bond durability performance of sand-coated BFRP bars in high-strength fiber reinforced concrete," Compos. Struct., vol. 321, p. 117306, Oct. 2023, doi: 10.1016/j.compstruct.2023.117306. View Article
[22] Wang Mingchao, Zhang Zuoguang, Li Yubin, Li Min, and Sun Zhijie, "Chemical Durability and Mechanical Properties of Alkali-proof Basalt Fiber and its Reinforced Epoxy Composites," J. Reinf. Plast. Compos., vol. 27, no. 4, pp. 393-407, Mar. 2008, doi: 10.1177/0731684407084119. View Article
[23] Z. Lu, G. Xian, and H. Li, "Effects of exposure to elevated temperatures and subsequent immersion in water or alkaline solution on the mechanical properties of pultruded BFRP plates," Compos. Part B Eng., vol. 77, pp. 421-430, Aug. 2015, doi: 10.1016/j.compositesb.2015.03.066. View Article
[24] S. Li et al., "Transverse low-velocity impact performance of BFRP bars after exposure to the saline-alkaline environment," Constr. Build. Mater., vol. 307, p. 124650, Nov. 2021, doi: 10.1016/j.conbuildmat.2021.124650. View Article
[25] M. Hassan, B. Benmokrane, A. ElSafty, and A. Fam, "Bond durability of basalt-fiber-reinforced-polymer (BFRP) bars embedded in concrete in aggressive environments," Compos. Part B Eng., vol. 106, pp. 262-272, Dec. 2016, doi: 10.1016/j.compositesb.2016.09.039. View Article
[26] "440.3R-04 Guide Test Methods for Fiber-Reinforced Polymers (FRPs) for Reinforcing or Strengthening Concrete Structures".
[27] D30 Committee, "Test Methods for Constituent Content of Composite Materials," ASTM International. doi: 10.1520/D3171-22. View Article
[28] D20 Committee, "Test Methods for Void Content of Reinforced Plastics," ASTM International. doi: 10.1520/D2734-23. View Article
[29] C09 Committee, Test Method for Compressive Strength of Cylindrical Concrete Specimens. doi: 10.1520/C0039_C0039M-23. View Article
[30] C09 Committee, "Test Method for Splitting Tensile Strength of Cylindrical Concrete Specimens," ASTM International. doi: 10.1520/C0496_C0496M-17. View Article
[31] C09 Committee, "Test Method for Pulse Velocity Through Concrete," ASTM International. doi: 10.1520/C0597-22. View Article
[32] D16 Committee, Test Method for pH of Aqueous Solutions With the Glass Electrode. doi: 10.1520/E0070-24. View Article
[33] D20 Committee, "Test Method for Water Absorption of Plastics," ASTM International. doi: 10.1520/D0570-22. View Article
[34] C. N. Morales, G. Claure, A. R. Emparanza, and A. Nanni, "Durability of GFRP reinforcing bars in seawater concrete," Constr. Build. Mater., vol. 270, p. 121492, Feb. 2021, doi: 10.1016/j.conbuildmat.2020.121492. View Article
[35] H. El-Hassan, T. El-Maaddawy, A. Al-Sallamin, and A. Al-Saidy, "Performance evaluation and microstructural characterization of GFRP bars in seawater-contaminated concrete," Constr. Build. Mater., vol. 147, pp. 66-78, Aug. 2017, doi: 10.1016/j.conbuildmat.2017.04.135. View Article
[36] H. El-Hassan, T. El-Maaddawy, A. Al-Sallamin, and A. Al-Saidy, "Durability of glass fiber-reinforced polymer bars conditioned in moist seawater-contaminated concrete under sustained load," Constr. Build. Mater., vol. 175, pp. 1-13, Jun. 2018, doi: 10.1016/j.conbuildmat.2018.04.107. View Article
[37] O. A. Mohamed, W. Al Hawat, and M. Keshawarz, "Durability and Mechanical Properties of Concrete Reinforced with Basalt Fiber-Reinforced Polymer (BFRP) Bars: Towards Sustainable Infrastructure," Polymers, vol. 13, no. 9, p. 1402, Apr. 2021, doi: 10.3390/polym13091402. View Article