Volume 7 - Year 2024- Pages 147-155
DOI: 10.11159/ijci.2024.015
The Impact of Sandy Fouled Ballast Properties on Its Mechanical Behavior
Ahmed Nabil Ramadan1, Jinxi Zhang1, Tianchi Li2, Biao Xu1, Peng Jing3,*
1Beijing University of Technology, College of Metropolitan Transportation
No.100 Ping Le Yuan, Beijing, China 100124,
ahmednabil@emails.bjut.edu.cn; zhangjinxi@bjut.edu.cn; biaox@emails.bjut.edu.cn
2China Railway Hohot Group Co., Ltd, Wuhai Track Maintenance Division
No.8 Shijidadao, Inner Mongolia, China 016000,
396070554@qq.com
3Beijing Jiaotong University, School of Civil Engineering
No.3 Shangyuan, Beijing, China 100044
pengjing@bjtu.edu.cn
*Author to whom correspondence should be addressed
Abstract - The impact of the coefficient of uniformity and porosity on the shear strength of sandy fouled ballast was examined in this study. Data from existing studies were analyzed to understand how these factors, alongside the fouling index, influence the mechanical behavior of the clean and fouled ballast. A clear inverse relationship between the coefficient of uniformity and shear strength was found when the fouling index was lower than 50%; beyond this point, the relationship tended to become positive. Furthermore, an unexpected inverse relationship was noted between porosity and shear strength, where lower porosity led to diminished shear strength. This atypical behavior was attributed to the combined presence of sand with ballast, creating a heterogeneous material that altered the typical impact of porosity seen in single-material compositions. These insights underscore the importance of considering multiple parameters, such as the coefficient of uniformity, porosity, and fouling index, for accurate predictions of shear strength. Understanding these relationships is essential for optimizing the mechanical behavior of sandy fouled ballast, thereby enhancing railway track design and maintenance strategies. This investigation provides a basic foundation to enhance the estimation and prediction of the shear strength of sandy fouled ballast based on experimental investigation of current studies.
Keywords: Sandy fouled ballast, Shear strength, Coefficient of uniformity, Porosity, Fouling index.
© Copyright 2024 Authors - This is an Open Access article published under the Creative Commons Attribution License terms. Unrestricted use, distribution, and reproduction in any medium are permitted, provided the original work is properly cited.
Date Received: 2023-11-16
Date Revised: 2024-07-19
Date Accepted: 2024-07-29
Date Published: 2024-09-13
1. Introduction
The mechanical behavior of railway ballast is critical to the stability and safety of railway tracks [1], [2]. Ballast, typically consisting of coarse aggregates, provides the necessary support and drainage for railway sleepers, ensuring the structural integrity of the track. However, over time, ballast can become fouled with finer materials such as sand and clay, which infiltrate the voids between the larger ballast particles [3]–[5]. This fouling can significantly alter the mechanical properties of the ballast, leading to changes in shear strength and overall track performance [6]–[8].
Fouled ballast poses several challenges for the mechanical behavior and railway maintenance. The presence of fouling materials affects the drainage capability and load distribution characteristics of the ballast layer [9], [10]. Understanding the impact of fouling on the shear strength of ballast is essential for developing effective maintenance strategies and improving the design of railway tracks. Previous studies explored various factors influencing the mechanical behavior of fouled ballast (e.g., type of fouling material, fouling percentage, water content, and abrasion and degradation) [6], [11]–[13]. And for unsaturated granular materials, there are semi-empirical equations used to predict the shear strength based on the hydraulic properties as illustrated in Eq. 1 [14] and Eq. 2 [15]. However, there is still a need for comprehensive analysis to establish robust predictive models with considering other important properties like coefficient of uniformity and porosity.


where τus is shear strength of soil in unsaturation state, uais pore air pressure, uw is pore water pressure, θs is saturated volumetric water content, θr is residual volumetric water content, ϕ' is effective angle of internal friction, and S is degree of saturation
This study aims to investigate the impact of key material properties, specifically the coefficient of uniformity and porosity along with fouling index, on the shear strength of sandy fouled ballast. Based on data from existing researches, the influence of variations in the coefficient of uniformity and porosity on the shear strength will be analyzed. The findings are expected to reveal an inverse relationship between the coefficient of uniformity and shear strength, where an increase in Cu leads to a decrease in shear strength. Additionally, an unusual inverse relationship between porosity and shear strength will be observed, attributed to the combined presence of ballast and sand. The presence of sand as a fouling material can alter the typical relationship between porosity and shear strength, as it fills the voids between ballast particles, affecting interparticle friction and cohesion. These insights highlight the importance of considering multiple parameters, such as Cu and porosity along with the fouling index, for accurate predictions of shear strength. This investigation provides a basic foundation to enhance the estimation and prediction of the shear strength of sandy fouled ballast, based on the experimental findings from current studies. By improving our understanding of these relationships, more effective maintenance strategies and track designs can be developed, ultimately enhancing the performance and safety of railway infrastructure.
2. Impact of Coefficient of Uniformity
The Coefficient of Uniformity (Cu) is a fundamental parameter in geotechnical engineering used to describe the gradation of granular materials like ballast and fouled ballast. It is defined based on Eq. 3, presenting the ratio of the particle diameter at 60% passing (D60) to the particle diameter at 10% passing (D10):

Generally for granular materials, a high Cu value indicates a wide range of particle sizes, suggesting a well-graded material with better packing and interlocking properties, which can enhance shear strength. Conversely, a low Cu value indicates a uniform particle size distribution, which might lead to lower shear strength due to reduced inter-particle friction and interlocking [16].
The shear strength of ballast fouled with sand and clay particles was investigated, considering various gradations of ballast stones [17]. Seven gradations of ballast stones were analyzed, with different fouling indices of sand particles (10%, 20%, and 40%). All samples were classified as poorly graded material according to Unified Soil Classification System [18]. The particle size distribution for the different gradations of ballast with sand fouling material is presented in Figure 1.
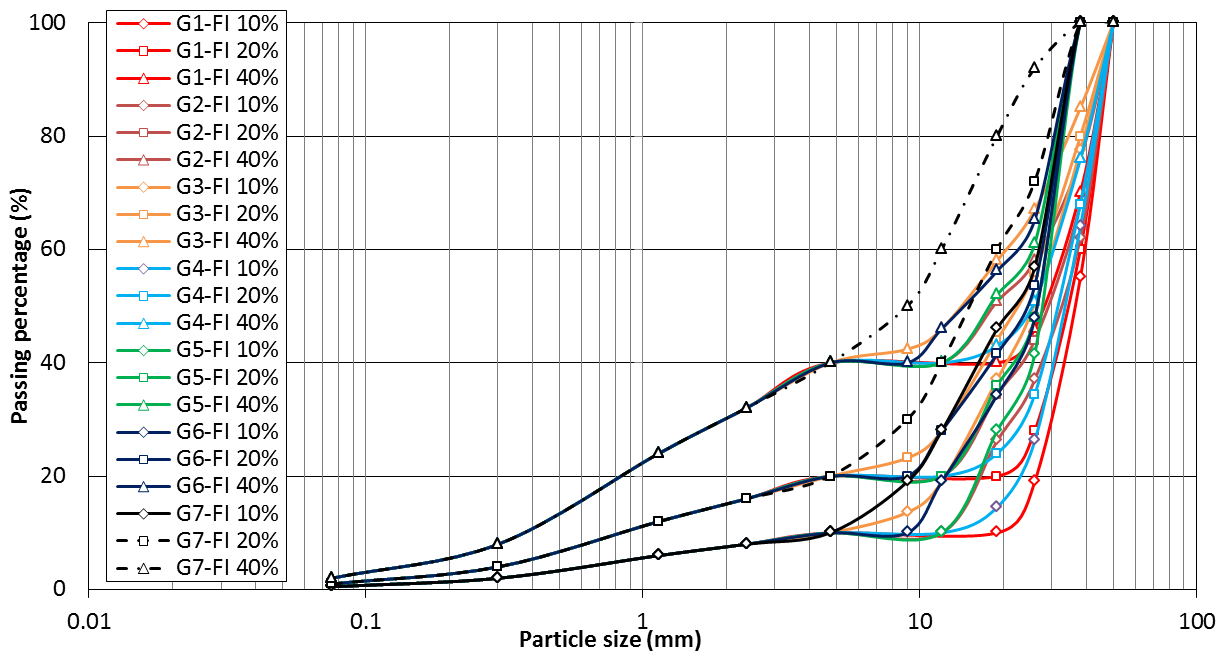
For each gradation of ballast with varying percentages of fouling index, the coefficient of uniformity (Cu) was calculated based on the particle size distribution curves, as shown in Table 1. The shear strength of each sample was determined by applying a maximum normal stress of 183 kPa, with the results presented in Table 1.
Table 1. Shear strength and coefficient of uniformity (Cu) of ballast with varying gradations and percentages of fouling index, based on [17].
Gradation type-FI (%) |
Coefficient of uniformity Cu |
Shear strength (kPa) at 183 kPa |
G1-0 |
50 |
263 |
G1-10 |
9.75 |
253.5 |
G1-20 |
44.7 |
245.5 |
G1-40 |
74.35 |
232.2 |
G2-0 |
50 |
281 |
G2-10 |
9.25 |
267.8 |
G2-20 |
41.17 |
255.7 |
G2-40 |
77.14 |
240.2 |
G3-0 |
50 |
300 |
G3-10 |
6.25 |
280.8 |
G3-20 |
32.94 |
265.8 |
G3-40 |
55.26 |
242 |
G4-0 |
40 |
231 |
G4-10 |
7.7 |
220.3 |
G4-20 |
41.14 |
210.2 |
G4-40 |
78.94 |
196.3 |
G5-0 |
37.5 |
204 |
G5-10 |
6.25 |
192.1 |
G5-20 |
35.29 |
177.9 |
G5-40 |
68.42 |
165.2 |
G6-0 |
37.5 |
213 |
G6-10 |
5.62 |
199.4 |
G6-20 |
32.94 |
182 |
G6-40 |
60.52 |
168.3 |
G7-0 |
37.5 |
226 |
G7-10 |
5.83 |
207 |
G7-20 |
22.35 |
185.3 |
G7-40 |
34.21 |
167.5 |
It can be observed that, regardless of the classification of the sandy fouled ballast (well-graded or poorly graded), the shear strength decreased with an increase in the coefficient of uniformity. In general, the presence of sand particles affected the size distribution of clean ballast, leading to a decrease in shear strength for any gradation type. Furthermore, the coefficient of uniformity decreased from the clean to the fouled state at low percentages of the fouling material.
Another investigation on shear strength was conducted for sandy fouled ballast with three levels of contamination (14%, 24%, and 37%). The particle size distribution for these samples is presented in Figure 2 [19].
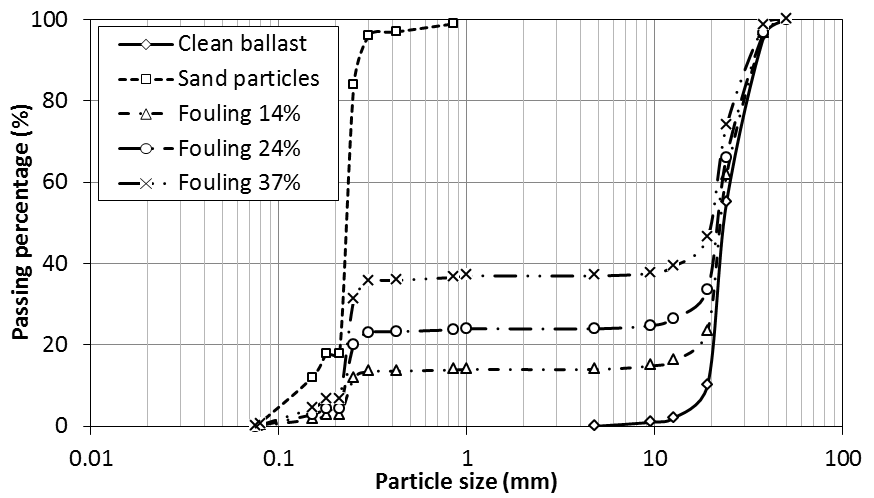
Based on the particle size distribution, the coefficients of uniformity for the three samples of fouled ballast (14%, 24%, and 37%) are 97.88, 98.44, and 99.95, respectively. In contrast, the coefficient of uniformity for the clean ballast is significantly lower, at 1.32. The shear strength of the samples was determined using a large-scale shear box test. The shear strength parameters, including cohesion and friction angle, were determined for each sample, as illustrated in Table 2.
Table 2. Shear strength parameters for each sample of clean and fouled ballast with sand, derived from [19].
Fouling (%) |
Coefficient of uniformity |
Cohesion intercept (kPa) |
Friction angle (Degree) |
Shear strength (kPa) at 100 kPa |
0 |
1.32 |
12.3 |
53.1 |
145.3 |
14 |
97.88 |
20.5 |
48.6 |
133.5 |
24 |
98.44 |
25.4 |
45.9 |
128.4 |
37 |
99.95 |
12 |
38.3 |
90.9 |
The clean ballast exhibits an effective cohesion intercept of 12.3 kPa. This value represents the base cohesion of the ballast material, which is free from any contaminating fines. It has a friction angle of 53.1 degrees, indicating a high resistance to shear due to the coarse, angular nature of the ballast particles that interlock effectively. When sand particles added to ballast to be contaminated, the cohesion intercept increases significantly to 20.5 kPa. The increase in cohesion can be attributed to the presence of fines that filled the voids between the ballast particles, enhancing interparticle friction and binding the particles more effectively. While the friction angle decreased to 48.6 degrees as sand particles reduced the interlocking, leading to a decrease in the overall shear resistance. Further contamination led to a peak cohesion intercept of 25.4 kPa. At this stage, the fines continue to fill the voids, further increasing the overall cohesion of the ballast material. The friction angle decreased to 45.9 degrees. This continued reduction reflects the on-going loss of interparticle friction as sand filled the voids, reducing the overall shear strength. With a higher level of fouling, the cohesion decreased to 12.0 kPa. The friction angle significantly drops to 38.3 degrees. This substantial reduction highlights the detrimental effects of excessive sand on the shear resistance of ballast. The sand may also create a lubrication effect, reducing the effective contact area between ballast particles. It can be noticed that the shear strength at a specific normal stress (e.g., 100 kPa) decreased by increasing the coefficient of uniformity and fouling index as shown in Table 2. So it can be found that in the fouled state with sand, by increasing the fouling index the coefficient of uniformity increased and the shear strength decreased.
Moreover, the shear strength of ballast fouled with varying percentages of sand was examined, as depicted by the particle size distribution shown in Figure 3.
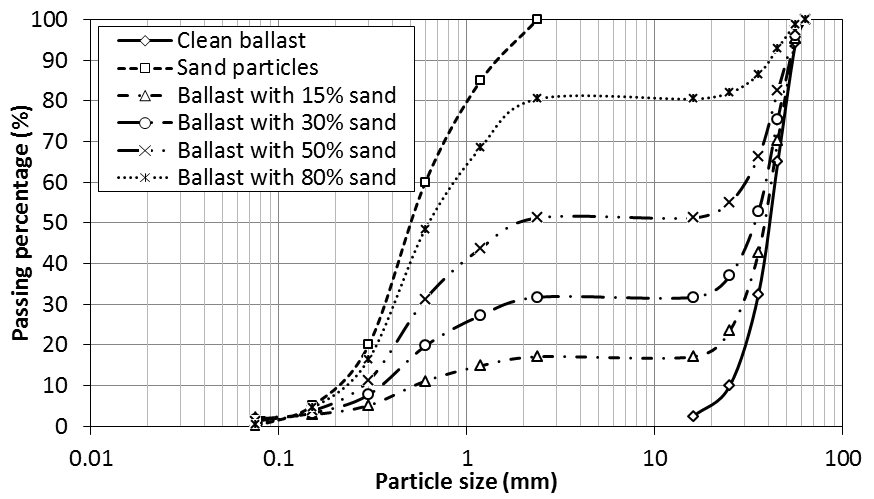
Based on the particle size distribution, the coefficients of uniformity for the five samples of clean and fouled ballast with their corresponding shear strengths at a normal stress of 150 kPa are presented in Table 3. It can be concluded that as the percentage of fouling material increased, the Cu increased and the shear strength decreased, as proven before, but only up to a certain threshold of 50% sand. At this percentage, the shear strength began to increase gradually, eventually surpassing the shear strength of the clean ballast.
Table 3. Shear strength of fouled ballast with sand considering its Cu, originating from [20].
Sand percentage or FI (%) |
Cu |
Shear strength (kPa) at 150 kPa |
0 |
1.76 |
418 |
15 |
84 |
361 |
30 |
90.69 |
359 |
50 |
111.11 |
440 |
80 |
3.86 |
462 |
The observed decrease in shear strength with an increasing coefficient of uniformity in wide grain particles, such as sandy fouled ballast (FI < 50%), can be attributed to several interrelated factors. Firstly, a higher coefficient of uniformity indicates a broader range of particle sizes, which often results in smaller particles filling the voids between larger ones. This filling action reduces the interlocking among larger particles because of the sand grains, thereby diminishing the material's ability to resist shear forces [21]. Additionally, the uneven load distribution due to the presence of a wide range of particle sizes leads to larger particles bearing most of the load, while smaller particles contribute less to load-bearing capacity, further weakening the structure. The increased proportion of small particles, commonly associated with a higher coefficient of uniformity, tends to act as a lubricant, reducing the overall frictional resistance between particles, which is crucial for shear strength. Moreover, while a higher coefficient of uniformity can lead to a denser packing and reduced void ratio, this densification does not necessarily enhance shear strength in heterogeneous materials like fouled ballast and sand. The complex interactions between different-sized particles in such mixtures often result in a weaker material structure, leading to decrease the shear strength [7], [22]. Consequently, the combination of reduced particle interlock, uneven load distribution, decreased frictional resistance, and changes in void ratio collectively justifies the reduction in shear strength with an increased coefficient of uniformity in these materials. Theoretical frameworks such as Terzaghi's effective stress principle [23] and critical state soil mechanics [24] provide insights into this phenomena, explaining the complex interplay between particle size distribution and shear strength.
However, once the fouling index exceeded 50%, the Cu began to decrease, indicating a reduction in the range of particle sizes. In this phase, the proportion of smaller particles increased that led to higher chances of filling more voids. This packing blockage restricted the movement of material particles, thereby increased the friction between them and subsequently enhanced the frictional resistance between particles [25], [26]. This increase in frictional resistance restored the interlocking and load-bearing capabilities of the material, contributing to a further increase in shear strength.
Hence, the coefficient of uniformity of sandy fouled ballast, which is related with the fouling index, plays an important vital rule and needed to be considered for estimating and predicting the shear strength of fouled ballast with sand in both cases of low and high fouling percentages.
4. Impact of Porosity (η)
Porosity, defined as the ratio of the volume of voids to the total volume of a material, plays a crucial role in geotechnical engineering, especially in the study of fouled ballast. In the context of sandy fouled ballast, porosity determines the material's ability to drain water and simultaneously affects its mechanical behavior under train loads. High porosity of the same material can lead to lower shear strength due to reduced contact between particles, resulting in decreased interparticle friction and cohesion.
The shear strength of sand soil particles (0.075 mm, 0.15 mm, 0.212 mm, 0.3 mm, 0.6 mm, 1.18 mm, 1.7 mm, and 2.36 mm) was examined by [27]. It was found that increasing the particle size of sand led to an increase in porosity that gave the chance to reduce the frictional area between particles and consequently decreased the shear strength. As illustrated in Figure 4, this relationship is evident, with higher porosity correlating with lower shear strength across different levels of applied loads (0.05 kN, 0.10 kN, and 0.15 kN). However, decreasing the porosity of ballast by adding fouling material (e.g., sand) can affect the mechanical behavior dreadfully.
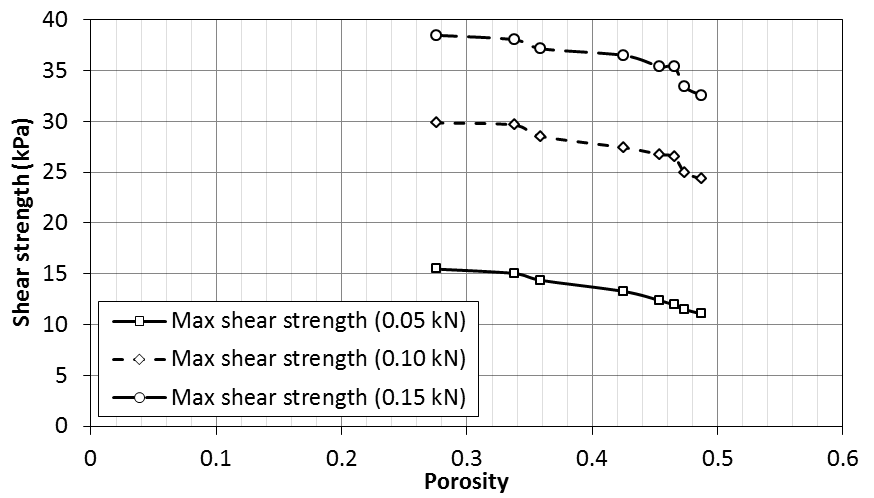
Through analysis and further investigation of the shear strength behavior of sandy fouled ballast samples from [5], a relationship was identified between porosity and shear strength under varying vertical loads. Table 4 presents the changes in shear strength corresponding to alterations in the porosity of the sandy fouled ballast.
Table 4. Relation between porosity and shear strength at different normal stress, dependent on [5].
Fouling index (%) |
Porosity |
Shear strength (kPa) |
|||
Normal stress (kPa) |
|||||
50 |
100 |
150 |
200 |
||
0 |
0.3518 |
101 |
143 |
207 |
284 |
14 |
0.2455 |
91 |
135 |
190 |
256 |
19 |
0.1986 |
86 |
131 |
184 |
238 |
24 |
0.1456 |
82 |
128 |
181 |
233 |
It was observed that increasing the fouling index led to a decrease in porosity, as sand particles filled the gaps between the ballast stones. Consequently, the shear strength decreased with the addition of fouling material and the reduction in porosity, which is an unusual behavior. Figure 5 illustrates how changes in the fouling index and porosity affected the shear strength of sandy fouled ballast under various normal stresses.
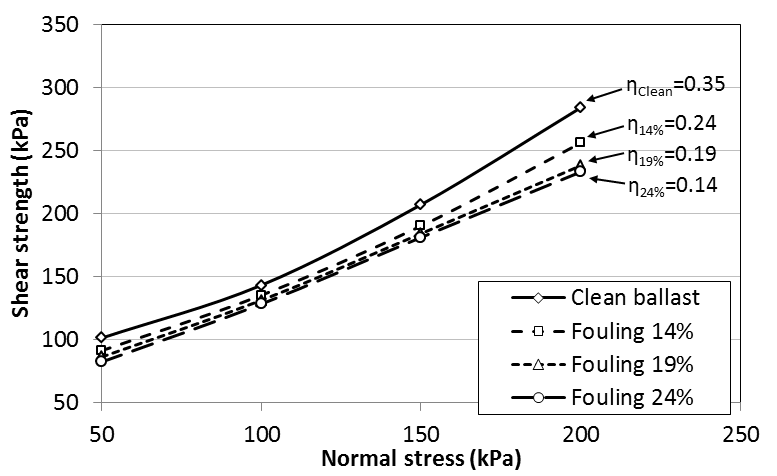
Continuing the investigation of the properties of clean and fouled ballast from [17], the effects of different porosities on shear strength were examined. Table 5 presents the impact of varying porosities on the shear strength of both clean and fouled ballast, with the fouling index considered as a fundamental parameter.
Table 5. Impact of porosity on shear strength at different normal stress, built upon [17].
Fouling index (%) |
Porosity |
Shear strength (kPa) |
||
Normal stress (kPa) |
||||
78 |
128 |
183 |
||
0 |
0.3522 |
141 |
205 |
263 |
10 |
0.3281 |
134 |
196.7 |
253.5 |
20 |
0.3040 |
125 |
188.6 |
245.5 |
40 |
0.2530 |
118.7 |
177.5 |
232.2 |
The analysis of the data presented in Table 4 reveals a significant impact of porosity on the shear strength of fouled ballast under different levels of normal stress. As the fouling index increases from 0% to 40%, the porosity of the material decreases from 0.3522 to 0.2530, indicating a denser mixture due to the higher sand content. This reduction in porosity correlates with a notable decrease in shear strength across all normal stress levels examined. Figure 6 illustrates how the decrease in porosity leads to a reduction in the shear strength of sandy fouled ballast.
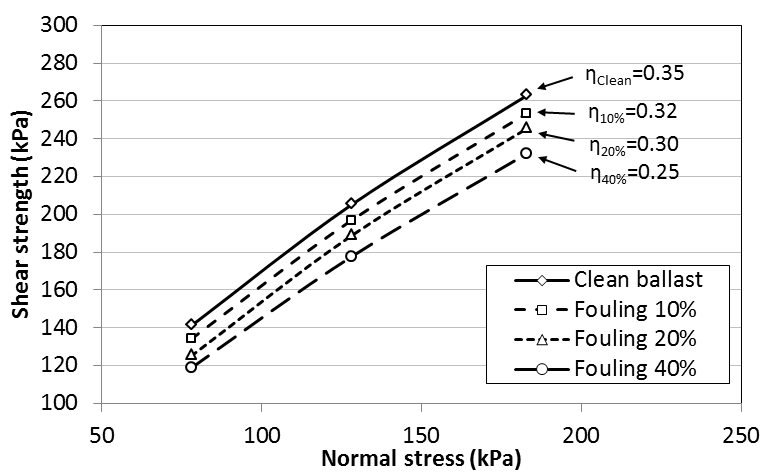
These findings underscored a consistent inverse relationship between porosity and shear strength in sandy fouled ballast. As porosity decreased and the bimodal material became denser, its ability to resist shear forces diminished across all normal stress conditions [28]. This behavior could be attributed to several key factors. In denser mixtures, smaller particles filled the voids between larger particles, reducing overall interlocking and weakening the material's ability to resist deformation under shear stress [29], [30]. Additionally, the presence of a wide range of particle sizes led to uneven load distribution, with larger particles bearing most of the load while smaller particles contributed less, further weakening the structure [31]. Moreover, smaller particles in denser mixtures acted as lubricants, reducing frictional resistance and thereby decreasing shear strength [32]. The reduced void ratio in denser mixtures could also increase pore water pressure during shear for wetted fouled ballast, further lowering shear strength by reducing effective stress. These factors collectively highlighted the critical role of porosity in determining the mechanical behavior of fouled ballast, emphasizing that lower porosity generally weakened the material's shear strength.
Hence, determining the shear strength of sandy fouled ballast material could be predicted not only based on the mechanical properties but also based on the material physical properties of coefficient of uniformity and porosity with considering the value of the fouling index.
5.Conclusion
The study underscores the intricate relationship between the coefficient of uniformity (Cu), porosity, and shear strength in sandy fouled ballast, emphasizing their critical roles in determining mechanical behavior and serving as a foundation for predicting shear strength based on the properties of this material. Initially, an increase in Cu up to a fouling index (FI) of 50% decreases shear strength due to smaller particles filling voids, reducing particle interlocking, and creating an uneven load distribution where larger particles bear most of the load. This increased proportion of small particles acts as a lubricant, lowering frictional resistance and consequently diminishing shear strength. Despite the denser packing associated with a higher Cu, the resultant complex particle interactions weaken the material structure. However, as the FI exceeds 50%, the Cu decreases, smaller particles fill more voids, restrict movement, and enhance frictional resistance, restoring interlocking and load-bearing capabilities and increasing shear strength. Additionally, the study demonstrates an inverse relationship between porosity and shear strength, where decreased porosity leads to denser material and diminished shear resistance due to reduced interlocking and causing lubrication by smaller particles. Unlike individual soils, sandy fouled ballast is a heterogeneous material with a wide range of grain sizes, contributing to its unique behavior based on the percentage of each size.
To ensure accurate predictions of shear strength for sandy fouled ballast, it is crucial to consider material properties such as the coefficient of uniformity and porosity, in addition to the fouling index. Understanding these relationships is essential for optimizing the mechanical behavior of sandy fouled ballast, thereby improving railway track maintenance and design. Future studies should focus on experimental validation of these findings and explore additional parameters that may influence shear strength.
References
[1] C. Ngamkhanong, B. Feng, E. Tutumluer, Y. M.A. Hashash, and S. Kaewunruen, "Evaluation of lateral stability of railway tracks due to ballast degradation," Constr. Build. Mater., vol. 278, p. 122342, Apr. 2021, doi: 10.1016/j.conbuildmat.2021.122342.
View Article
[2] C. Shi, Z. Fan, D. P. Connolly, G. Jing, V. Markine, and Y. Guo, "Railway ballast performance: Recent advances in the understanding of geometry, distribution and degradation," Transp. Geotech., vol. 41, p. 101042, Jul. 2023, doi: 10.1016/j.trgeo.2023.101042.
View Article
[3] A. Ebrahimi, J. M. Tinjum, and T. B. Edil, "Deformational behavior of fouled railway ballast," Can. Geotech. J., vol. 52, no. 3, pp. 344-355, Mar. 2015, doi: 10.1139/cgj-2013-0271.
View Article
[4] N. TENNAKOON and B. INDRARATNA, "Behaviour of clay-fouled ballast under cyclic loading," Géotechnique, vol. 64, no. 6, pp. 502-506, May 2014, doi: 10.1680/geot.13.T.033.
View Article
[5] J. Sadeghi, D. Ph, A. Reza, T. Kian, D. Ph, and M. Fallah, "Experimental Investigation of Mechanical Properties of Ballast Contaminated with Wet Sand Materials," vol. 21, no. 1, pp. 1-13, 2021, doi: 10.1061/(ASCE)GM.1943-5622.0001886.
View Article
[6] L. Wang, M. Meguid, and H. S. Mitri, "Impact of Ballast Fouling on the Mechanical Properties of Railway Ballast: Insights from Discrete Element Analysis," Processes, vol. 9, no. 8, p. 1331, Jul. 2021, doi: 10.3390/pr9081331.
View Article
[7] J. J. Kumara and K. Hayano, "Deformation characteristics of fresh and fouled ballasts subjected to tamping maintenance," Soils Found., vol. 56, no. 4, pp. 652-663, 2016, doi: 10.1016/j.sandf.2016.07.006.
View Article
[8] P. Anbazhagan, T. P. Bharatha, and G. Amarajeevi, "Study of Ballast Fouling in Railway Track Formations," Indian Geotech. J., vol. 42, no. 2, pp. 87-99, Jun. 2012, doi: 10.1007/s40098-012-0006-6.
View Article
[9] N. Tennakoon, B. Indraratna, C. Rujikiatkamjorn, S. Nimbalkar, and T. Neville, "The Role of Ballast-Fouling Characteristics on the Drainage Capacity of Rail Substructure," Geotech. Test. J., vol. 35, no. 4, p. 104107, Jul. 2012, doi: 10.1520/GTJ104107.
View Article
[10] N. Tennakoon, B. Indraratna, and S. Nimbalkar, "Impact of Ballast Fouling on Rail Tracks," doi: 10.4203/ccp.104.122.
View Article
[11] S. Kulesza, M. L. Barry, S. Debojit, F. Ruimin, R. William, and P. Kyle, "Unsaturated Characteristics of Fouled Ballast to Support In Situ Identification of Fouling Using Ground Penetrating Radar - Phase II," 2023.
[12] R. Bruzek, T. D. Stark, S. T. Wilk, H. B. Thompson, and T. R. Sussmann, "Fouled Ballast Definitions and Parameters," Apr. 2016, doi: 10.1115/JRC2016-5725.
View Article
[13] Y. Cui, T. V. Duong, and A. M. Tang, "Investigation of the hydro-mechanical behaviour of fouled ballast," doi: https://doi.org/10.1631/jzus.A1200337.
View Article
[14] S. K. Vanapalli, D. G. Fredlund, D. E. Pufahl, and A. W. Clifton, "Model for the prediction of shear strength with respect to soil suction," Can. Geotech. J., vol. 33, no. 3, pp. 379-392, Jul. 1996, doi: 10.1139/t96-060.
View Article
[15] A. Öberg and G. Sällfors, "Determination of Shear Strength Parameters of Unsaturated Silts and Sands Based on the Water Retention Curve," Geotech. Test. J., vol. 20, no. 1, pp. 40-48, Mar. 1997, doi: 10.1520/GTJ11419J.
View Article
[16] B. B. Dai, J. Yang, and C. Y. Zhou, "Observed Effects of Interparticle Friction and Particle Size on Shear Behavior of Granular Materials," Int. J. Geomech., vol. 16, no. 1, Feb. 2016, doi: 10.1061/(ASCE)GM.1943-5622.0000520.
View Article
[17] A. Danesh, M. Palassi, and A. A. Mirghasemi, "Effect of sand and clay fouling on the shear strength of railway ballast for different ballast gradations," Granul. Matter, vol. 20, no. 3, pp. 1-14, 2018, doi: 10.1007/s10035-018-0824-z.
View Article
[18] I. ASTM, "Standard Practice for Classification of Soils for Engineering Purposes (Unified Soil Classification System) ASTM D2487-17," West Conshohocken, PA, 2017. doi: https://doi.org/10.1520/D2487-17.
View Article
[19] A. R. TolouKian, J. Sadeghi, and J.-A. Zakeri, "Large-scale direct shear tests on sand-contaminated ballast," Proc. Inst. Civ. Eng. - Geotech. Eng., vol. 171, no. 5, pp. 451-461, Oct. 2018, doi: 10.1680/jgeen.17.00107.
View Article
[20] Y. Chi et al., "Research on the mechanism of railway ballast shear performance under various sand contents and load conditions," Comput. Part. Mech., May 2024, doi: 10.1007/s40571-024-00776-1.
View Article
[21] B. Indraratna, L. Su, and C. Rujikiatkamjorn, "A new parameter for classification and evaluation of railway ballast fouling," Can. Geotech. J., vol. 48, no. 2, pp. 322-326, Feb. 2011, doi: 10.1139/T10-066.
View Article
[22] J. Chen, R. Gao, Y. Liu, Z. Shi, and R. Zhang, "Numerical exploration of the behavior of coal-fouled ballast subjected to direct shear test," Constr. Build. Mater., vol. 273, p. 121927, Mar. 2021, doi: 10.1016/j.conbuildmat.2020.121927.
View Article
[23] T. Karl, Theoretical Soil Mechanics, 1st ed. New York: John Wiley & Sons, Inc., 1943.
[24] A. Schofield and P. Wroth, Critical State Soil Mechanics, 1st ed. London: McGraw-Hill, 1968.
[25] F. Daghistani and H. Abuel-Naga, "Evaluating the Influence of Sand Particle Morphology on Shear Strength: A Comparison of Experimental and Machine Learning Approaches," Appl. Sci., vol. 13, no. 14, p. 8160, Jul. 2023, doi: 10.3390/app13148160.
View Article
[26] C. Chen, J. Gu, Z. Peng, X. Dai, Q. Liu, and G.-Q. Zhu, "Discrete element modeling of particles sphericity effect on sand direct shear performance," Sci. Rep., vol. 12, no. 1, p. 5490, Mar. 2022, doi: 10.1038/s41598-022-09543-9.
View Article
[27] M. N. Islam, A. Siddika, M. B. Hossain, A. Rahman, and M. A. Asad, "Effect of particle size on the shear strength behavior of sands," Aust. Geomech., vol. 46, no. 3, 2011.
[28] M. P. J. Schöpfer, S. Abe, C. Childs, and J. J. Walsh, "The impact of porosity and crack density on the elasticity, strength and friction of cohesive granular materials: Insights from DEM modelling," Int. J. Rock Mech. Min. Sci., vol. 46, no. 2, pp. 250-261, Feb. 2009, doi: 10.1016/j.ijrmms.2008.03.009.
View Article
[29] Y. Peng, L. Su, Y. Wang, and L. Zhang, "Analysis of the Effect of Porosity in Concrete under Compression Based on DIP Technology," J. Mater. Civ. Eng., vol. 34, no. 1, Jan. 2022, doi: 10.1061/(ASCE)MT.1943-5533.0004011.
View Article
[30] R. Parsons, A. Rahman, and J. Han, "Properties of Fouled Railroad Ballast (Phase 1)," 2012. [Online]. Available:
View Article
[31] A. K. Rohrman, C. L. Ho, H. F. Kashani, and J. P. Hyslip, "Laboratory Study of the Failure Characteristics of Fouled Ballast: Phase II," 2018. [Online]. Available:
View Article
[32] T. R. Sussmann, M. Ruel, and S. M. Chrismer, "Source of Ballast Fouling and Influence Considerations for Condition Assessment Criteria," Transp. Res. Rec. J. Transp. Res. Board, vol. 2289, no. 1, pp. 87-94, Jan. 2012, doi: 10.3141/2289-12.
View Article
[1] C. Ngamkhanong, B. Feng, E. Tutumluer, Y. M.A. Hashash, and S. Kaewunruen, "Evaluation of lateral stability of railway tracks due to ballast degradation," Constr. Build. Mater., vol. 278, p. 122342, Apr. 2021, doi: 10.1016/j.conbuildmat.2021.122342. View Article
[2] C. Shi, Z. Fan, D. P. Connolly, G. Jing, V. Markine, and Y. Guo, "Railway ballast performance: Recent advances in the understanding of geometry, distribution and degradation," Transp. Geotech., vol. 41, p. 101042, Jul. 2023, doi: 10.1016/j.trgeo.2023.101042. View Article
[3] A. Ebrahimi, J. M. Tinjum, and T. B. Edil, "Deformational behavior of fouled railway ballast," Can. Geotech. J., vol. 52, no. 3, pp. 344-355, Mar. 2015, doi: 10.1139/cgj-2013-0271. View Article
[4] N. TENNAKOON and B. INDRARATNA, "Behaviour of clay-fouled ballast under cyclic loading," Géotechnique, vol. 64, no. 6, pp. 502-506, May 2014, doi: 10.1680/geot.13.T.033. View Article
[5] J. Sadeghi, D. Ph, A. Reza, T. Kian, D. Ph, and M. Fallah, "Experimental Investigation of Mechanical Properties of Ballast Contaminated with Wet Sand Materials," vol. 21, no. 1, pp. 1-13, 2021, doi: 10.1061/(ASCE)GM.1943-5622.0001886. View Article
[6] L. Wang, M. Meguid, and H. S. Mitri, "Impact of Ballast Fouling on the Mechanical Properties of Railway Ballast: Insights from Discrete Element Analysis," Processes, vol. 9, no. 8, p. 1331, Jul. 2021, doi: 10.3390/pr9081331. View Article
[7] J. J. Kumara and K. Hayano, "Deformation characteristics of fresh and fouled ballasts subjected to tamping maintenance," Soils Found., vol. 56, no. 4, pp. 652-663, 2016, doi: 10.1016/j.sandf.2016.07.006. View Article
[8] P. Anbazhagan, T. P. Bharatha, and G. Amarajeevi, "Study of Ballast Fouling in Railway Track Formations," Indian Geotech. J., vol. 42, no. 2, pp. 87-99, Jun. 2012, doi: 10.1007/s40098-012-0006-6. View Article
[9] N. Tennakoon, B. Indraratna, C. Rujikiatkamjorn, S. Nimbalkar, and T. Neville, "The Role of Ballast-Fouling Characteristics on the Drainage Capacity of Rail Substructure," Geotech. Test. J., vol. 35, no. 4, p. 104107, Jul. 2012, doi: 10.1520/GTJ104107. View Article
[10] N. Tennakoon, B. Indraratna, and S. Nimbalkar, "Impact of Ballast Fouling on Rail Tracks," doi: 10.4203/ccp.104.122. View Article
[11] S. Kulesza, M. L. Barry, S. Debojit, F. Ruimin, R. William, and P. Kyle, "Unsaturated Characteristics of Fouled Ballast to Support In Situ Identification of Fouling Using Ground Penetrating Radar - Phase II," 2023.
[12] R. Bruzek, T. D. Stark, S. T. Wilk, H. B. Thompson, and T. R. Sussmann, "Fouled Ballast Definitions and Parameters," Apr. 2016, doi: 10.1115/JRC2016-5725. View Article
[13] Y. Cui, T. V. Duong, and A. M. Tang, "Investigation of the hydro-mechanical behaviour of fouled ballast," doi: https://doi.org/10.1631/jzus.A1200337. View Article
[14] S. K. Vanapalli, D. G. Fredlund, D. E. Pufahl, and A. W. Clifton, "Model for the prediction of shear strength with respect to soil suction," Can. Geotech. J., vol. 33, no. 3, pp. 379-392, Jul. 1996, doi: 10.1139/t96-060. View Article
[15] A. Öberg and G. Sällfors, "Determination of Shear Strength Parameters of Unsaturated Silts and Sands Based on the Water Retention Curve," Geotech. Test. J., vol. 20, no. 1, pp. 40-48, Mar. 1997, doi: 10.1520/GTJ11419J. View Article
[16] B. B. Dai, J. Yang, and C. Y. Zhou, "Observed Effects of Interparticle Friction and Particle Size on Shear Behavior of Granular Materials," Int. J. Geomech., vol. 16, no. 1, Feb. 2016, doi: 10.1061/(ASCE)GM.1943-5622.0000520. View Article
[17] A. Danesh, M. Palassi, and A. A. Mirghasemi, "Effect of sand and clay fouling on the shear strength of railway ballast for different ballast gradations," Granul. Matter, vol. 20, no. 3, pp. 1-14, 2018, doi: 10.1007/s10035-018-0824-z. View Article
[18] I. ASTM, "Standard Practice for Classification of Soils for Engineering Purposes (Unified Soil Classification System) ASTM D2487-17," West Conshohocken, PA, 2017. doi: https://doi.org/10.1520/D2487-17. View Article
[19] A. R. TolouKian, J. Sadeghi, and J.-A. Zakeri, "Large-scale direct shear tests on sand-contaminated ballast," Proc. Inst. Civ. Eng. - Geotech. Eng., vol. 171, no. 5, pp. 451-461, Oct. 2018, doi: 10.1680/jgeen.17.00107. View Article
[20] Y. Chi et al., "Research on the mechanism of railway ballast shear performance under various sand contents and load conditions," Comput. Part. Mech., May 2024, doi: 10.1007/s40571-024-00776-1. View Article
[21] B. Indraratna, L. Su, and C. Rujikiatkamjorn, "A new parameter for classification and evaluation of railway ballast fouling," Can. Geotech. J., vol. 48, no. 2, pp. 322-326, Feb. 2011, doi: 10.1139/T10-066. View Article
[22] J. Chen, R. Gao, Y. Liu, Z. Shi, and R. Zhang, "Numerical exploration of the behavior of coal-fouled ballast subjected to direct shear test," Constr. Build. Mater., vol. 273, p. 121927, Mar. 2021, doi: 10.1016/j.conbuildmat.2020.121927. View Article
[23] T. Karl, Theoretical Soil Mechanics, 1st ed. New York: John Wiley & Sons, Inc., 1943.
[24] A. Schofield and P. Wroth, Critical State Soil Mechanics, 1st ed. London: McGraw-Hill, 1968.
[25] F. Daghistani and H. Abuel-Naga, "Evaluating the Influence of Sand Particle Morphology on Shear Strength: A Comparison of Experimental and Machine Learning Approaches," Appl. Sci., vol. 13, no. 14, p. 8160, Jul. 2023, doi: 10.3390/app13148160. View Article
[26] C. Chen, J. Gu, Z. Peng, X. Dai, Q. Liu, and G.-Q. Zhu, "Discrete element modeling of particles sphericity effect on sand direct shear performance," Sci. Rep., vol. 12, no. 1, p. 5490, Mar. 2022, doi: 10.1038/s41598-022-09543-9. View Article
[27] M. N. Islam, A. Siddika, M. B. Hossain, A. Rahman, and M. A. Asad, "Effect of particle size on the shear strength behavior of sands," Aust. Geomech., vol. 46, no. 3, 2011.
[28] M. P. J. Schöpfer, S. Abe, C. Childs, and J. J. Walsh, "The impact of porosity and crack density on the elasticity, strength and friction of cohesive granular materials: Insights from DEM modelling," Int. J. Rock Mech. Min. Sci., vol. 46, no. 2, pp. 250-261, Feb. 2009, doi: 10.1016/j.ijrmms.2008.03.009. View Article
[29] Y. Peng, L. Su, Y. Wang, and L. Zhang, "Analysis of the Effect of Porosity in Concrete under Compression Based on DIP Technology," J. Mater. Civ. Eng., vol. 34, no. 1, Jan. 2022, doi: 10.1061/(ASCE)MT.1943-5533.0004011. View Article
[30] R. Parsons, A. Rahman, and J. Han, "Properties of Fouled Railroad Ballast (Phase 1)," 2012. [Online]. Available: View Article
[31] A. K. Rohrman, C. L. Ho, H. F. Kashani, and J. P. Hyslip, "Laboratory Study of the Failure Characteristics of Fouled Ballast: Phase II," 2018. [Online]. Available: View Article
[32] T. R. Sussmann, M. Ruel, and S. M. Chrismer, "Source of Ballast Fouling and Influence Considerations for Condition Assessment Criteria," Transp. Res. Rec. J. Transp. Res. Board, vol. 2289, no. 1, pp. 87-94, Jan. 2012, doi: 10.3141/2289-12. View Article