Volume 4 - Year 2021- Pages 78-84
DOI: 10.11159/ijci.2021.011
Life Cycle Inventory for the Production of Recycled Concrete Aggregates in the United Arab Emirates
Mohammed Alzard1, Hilal El-Hassan1, Tamer El-Maaddawy1
1United Arab Emirates University, Department of Civil and Environmental Engineering
P.O. Box 15551, Al Ain, United Arab Emirates
201570286@uaeu.ac.ae; helhassan@uaeu.ac.ae; tamer.maaddawy@uaeu.ac.ae
Abstract - Environmental life cycle inventory (LCI) datasets are crucial for conducting life cycle assessment (LCA) of concrete or any other products. It is necessary to obtain these values based on local practices to provide accurate LCA results that reflect real-life scenarios. In the city of Abu Dhabi, United Arab Emirates, datasets for the recycling process of construction and demolition waste into recycled concrete aggregates are currently unavailable. Therefore, this research aims to draw a detailed environmental LCI dataset for the production of RCA in Abu Dhabi. As part of the adopted methodology proposed by the International Standards Organization (ISO) to build an LCI (ISO 14040), a thorough investigation of the RCA production practice was performed to highlight the input and output of each process unit. The resulting LCI value of RCA production was found to be 0.676 kg CO2eq per ton of aggregates (or 6.67x10-4 kg CO2eq/kg). It is eight times less than the environmental burden of producing natural aggregates. Research findings serve as a benchmark to evaluate the environmental sustainability of RCA and RCA-based products in a holistic LCA study, while also enriching the LCI of the city of Abu Dhabi.
Keywords: Recycled concrete aggregates, Life cycle assessment, Life cycle inventory, Construction and demolition waste.
© Copyright 2021 Authors - This is an Open Access article published under the Creative Commons Attribution License terms. Unrestricted use, distribution, and reproduction in any medium are permitted, provided the original work is properly cited.
Date Received: 2020-12-18
Date Accepted: 2020-12-22
Date Published: 2021-04-07
1. Introduction
In a rapidly growing economy, the need for natural aggregates (NA) has increased dramatically. Recent statistics show that there is an expected 45% increase in demand for aggregates by the year 2025 [1]. Concurrently, a significant amount of waste is generated due to construction and demolition activities. This type of waste is called construction and demolition waste (CDW). It poses a major challenge for the construction industry, owing to its increasing volumes, which account for 30-40% of the total amount of solid waste worldwide, and its associated environmental impact [2]. Traditionally, CDW is sent to landfills for disposal. However, this waste management technique is not sustainable due to the scarcity of landfill sites and their adverse impact on the environment [3]–[5]. Recycling such CDW through their conversion into recycled concrete aggregates (RCA) is a more sustainable approach and has a positive influence on both the environment and economy [6]. The process aims to alleviate the burden on landfills, reduce the demand for NA, cut the cost of the primary production of NA, and potentially lower the cost of construction [6].
Recycled concrete aggregates can be utilized in different construction applications. These include the use of RCA in the production of concrete [7]–[9], as secondary raw material in concrete curbs and floor blocks [10], [11], in precast concrete products [12], and as an engineering fill in the construction of roads (sub-base materials) [13]. Even with its impressive potential to promote environmental sustainability, the inferior performance of RCA compared to NA renders it useful for non-structural applications only. Such inferior properties of RCA are a result of the presence of an old mortar attached to the NA [3], [5], [6]. Despite their negative impact when employed in concrete, their true potential should be exploited by expanding their use to structural applications. In fact, previous research has been successful in developing structural concrete made with RCA [14]–[18]. Therefore, it is clear that the performance-based qualitative assessment of RCA concrete is promising.
Even if RCA could replace NA for use in structural applications, its adoption by the construction industry will be hindered until the burden of its recycling and production process is investigated from an environmental perspective [19]. To achieve this, a life cycle assessment (LCA) of RCA production should be conducted. Several guidelines have been developed to provide means and tools to conduct LCA such as the Intergovernmental Panel on Climate Change (2006 IPCC Guidelines) [20] and the International Standards Organization (ISO 14040) [21]. Usually, these methodologies provide default life cycle inventory values to facilitate carrying out the LCA. Yet, these values may lead to an inaccurate assessment since they are common and not country/region-specific. Therefore, most guidelines emphasize developing and using local datasets to better reflect the real situation in the country or region and produce an accurate assessment. In the city of Abu Dhabi, the United Arab Emirates, such datasets for the recycling process do not exist and should be developed to properly assess the environmental feasibility of using RCA in construction applications [22].
This research aims to develop a life cycle inventory (LCI) dataset for the recycling of CDW into RCA in the city of Abu Dhabi based on current local practices. Developing these values is of critical importance, as it is the building block for conducting an LCA study for different locally-made products that may utilize RCA rather than NA. It is also essential to allow stakeholders to compare the environmental impact of NA and RCA production in Abu Dhabi.
2. Methodology
The ISO 14040 proposed methodology to build an LCI was adopted to carry out this study [21]. Based on this methodology, the LCI development process mainly consists of data collection and calculations. These aim to quantify inputs and outputs of materials and energy associated with the product system under investigation. The described operational procedure is illustrated in Figure 1. The following sections describe the data collection and present the calculations and results.
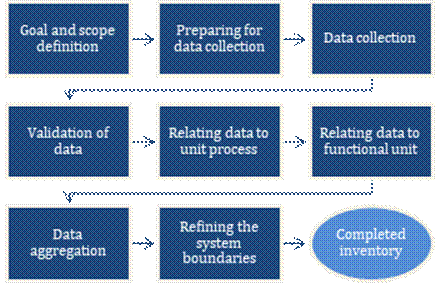
2. 1. Preparation for Data Collection
In preparation for data collection, input, and output data of unit processes were identified within the holistic process tree. Data was then collected following a detailed examination of the RCA production system. Furthermore, time-related, geographical, and technological coverage were defined. Identifying and depicting a comprehensive representation of the involved process is a critical step in data collection. In fact, a detailed process reduces the uncertainty related to the process identification while also highlighting the processes that should be included. A preliminary visit and examination of the site were conducted to establish these parameters. The recycling plant under investigation is part of Al Dhafra Recycling Industries (ADRI), which is located 60 km to the southwest of Abu Dhabi, the capital of the United Arab Emirates. This recycling plant is the largest in the region of Abu Dhabi by land area and handling capacity of CDW. An aerial view of the plant is shown in Figure 2. This preliminary visit was conducted to attain a comprehensive understanding of the recycling process at ADRI, the characteristics of the unit process under consideration, the input parameters (raw materials, ancillary materials, energy, transportation), and the output parameters (emissions to air, water, and land) along with their quantities.
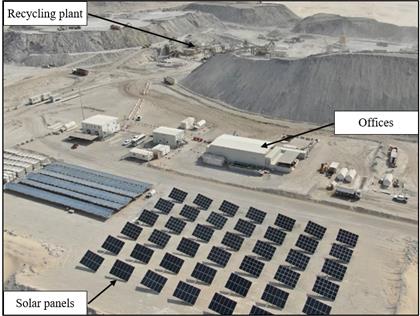
2. 2. Data Collection and Verification
A description of the recycling process in the plant was drawn after acquiring sufficient information from the preliminary investigation visit to the site, as shown in Figure 3. The recycling process first entails the inspection and weighing of the CDW in the delivery trucks. This step is important to ensure that the delivered waste conforms to the plant’s requirements. After inspection, the trucks unload the CDW in a designated area where wheel loaders then load the waste into the plant’s feeding inlet. This inlet feeds the waste to jaw crushers to be crushed. The resulting crushed waste material is then transported by a series of conveyor belts to a station with an overhead magnet to remove the steel and separate it from the crushed product. This steel is either sold as scrap metal or sent to an adjacent steel recycling plant to be recycled. The conveyor belts further transport the crushed materials to a picking station where workers manually remove any visible undesired components, such as plastic, glass, or wood. These materials are separated from the crushed wastes because they may negatively impact the quality of the final product. The crushed material is then forwarded to a screening station to examine its size distribution and ensure its compliance with the standards. At this point, if the required size is not achieved, the material is sent to a second crushing cycle. This process ensures that the desired aggregates size is attained. Based on past experience, some relatively fine steel particles passed the first magnet, so a second magnet was installed to ensure that any residual steel was isolated and removed. The final obtained product is sprayed with water to rid the aggregates from attached dust. Finally, the aggregates are stockpiled and ready to be used. The final product (RCA) is presented in Figure 4, and its physical properties are summarized in Table 1.
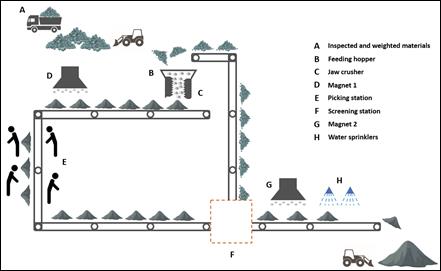
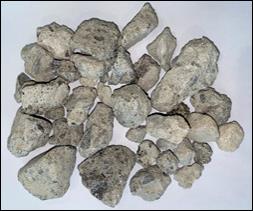
Table 1. Physical properties of the RCA.
Physical property | Unit | Value |
Dry rodded density | kg/m3 | 1563.0 |
Water absorption | % | 6.6 |
Los Angeles abrasion | % | 32.6 |
Specific gravity | - | 2.6 |
Fineness modulus | - | 7.7 |
Soundness (MgSO4) | % | 2.7 |
Surface area | cm2/g | 2.5 |
The subsequent step involves the collection of data relating to the input of materials and energy and the output (such as products, co-products, and emissions) of each unit process within the RCA production process. This step was performed based on the information provided by ADRI recycling plant officials. It highlights the possible sources of influence on the environmental impact of RCA. Evidently, the recycling plant processes up to 7000 tons of RCA during a 12-hour work shift, consuming up to 700 kW of electricity per day to power the plant and offices. This required electricity is entirely generated by solar panels that are installed within the vicinity of the plant, as displayed in Figure 2. These panels serve as a renewable energy source and do not have any environmental footprint during their operation or construction phase [24]. On this basis, it was assumed that the plant did not consume energy and consequently, its environmental burden relevant to energy usage was discarded.
Moreover, part of the operations includes several heavy machinery and equipment that operate as part of the recycling process, as shown in Figure 3. The investigation showed that these heavy machinery are the main contributors to the environmental impact of RCA. These equipment use diesel as a fuel and operate for 12 hours per day shift to transfer the waste to the feeding inlet of the crushers, convey the final product into stockpiles, and consequently, relocate it to delivery trucks. To calculate their environmental impact, their daily diesel consumption was calculated. The manufacturer’s specifications and application handbook of these heavy machinery were used to obtain their fuel consumption data, considering their working load as “medium” [18]. Based on the methodology proposed by the Intergovernmental Panel on Climate Change (IPCC) [20], to quantify the environmental impact of a product or a service, the impact of each activity is quantified and then multiplied by the proper emission factor, as shown in Eq. 1 [22]. In this equation, the emission factor refers to the equivalent CO2 (CO2eq) produced from the combustion of 1 liter of diesel fuel, assuming that such diesel fuel was entirely combusted without any losses.

Where E is emissions (in kg CO2eq), FCR is fuel consumption rate (L fuel/equipment. h), Q is the quantity of equipment (number of equipment), D is the operation duration of each equipment (h), and EF is the emission factor (kg CO2eq/L fuel).
Based on the IPCC guidelines [20], the emission factor was found to be 2.669 kg CO2eq per liter of diesel fuel consumed. The use of this value will result in a general, non-region-specific LCI value; however, since Abu Dhabi lacks emission factors related to fuel consumption, its use in this work is credible and acceptable while acknowledging the presence of limited uncertainty in the input. Table 2 summarizes the collected data needed to quantify the environmental impact of these machinery. These fuel consumption values were obtained directly from the equipment manufacturer to reduce the uncertainty. Also, it should be noted that the environmental footprint associated with the trucks used to transport the CDW to the recycling plant, i.e., demolition and transportation, was not accounted for. This is because government regulations require that all demolished structures be transported to a dumpsite, which is in the vicinity of the recycling plant. This means that CDW will have to be transported to the area, whether to be recycled or disposed of. As a result, the transportation of CDW from the demolition site to the recycling plant will not contribute to the environmental impact of RCA production.
Table 2. Details about the used equipment in the recycling process.
Equipment | Brand and model | Quantity | Fuel consumption (L/h) |
Hydraulic excavator | Komatsu PC300 | 1 | 22.7 |
Wheel loader | Komatsu WA470 | 4 | 23.0 |
Wheel loader | Komatsu WA500 | 1 | 33.0 |
3. Results and Discussion
Analysis of the collected and verified data for the unit processes of each product was carried out to facilitate the calculation of the LCI dataset for RCA production in the city of Abu Dhabi. The operation of these heavy machinery were considered as the sole contributor to the environmental burden of the recycling process. Therefore, data related to their quantities, operating hours, fuel consumption, and environmental impact were collected. The environmental impact of each equipment was calculated utilizing Eq. 1. The results are summarized in Table 3. First, the total amount of fuel consumed by each equipment was calculated per shift depending on the brand and model, as the fuel consumption rates differ among them. Then, the obtained fuel consumption value was multiplied by the emission factor for diesel to obtain the emissions (in kg CO2eq) per shift. The emissions were then added to determine the total global warming potential associated with the use of these equipment. It was found to be 4730.5 kg CO2eq.
The recycling plant produces 7000 tons of RCA per 12-hour shift. Accordingly, the environmental impact of producing 1 ton of RCA is the ratio of the total global warming potential (4730.5 kg CO2eq) to the total production (7000 tons), yielding 0.676 kg CO2eq (6.67x10-4 kg CO2eq per kg of RCA). Compared to the environmental burden of typical NA production (5.2x10-3 CO 2eq per kg of NA [26]), that of RCA production is nearly eight times lesser. Also, the replacement of NA by RCA leads to an approximate 87% reduction in the environmental burden of aggregates. This shows that the use of RCA instead of NA is more sustainable strictly from a production standpoint. Nevertheless, this comparison between RCA and NA is associated with some uncertainty due to the adoption of a non-region-specific emission factor from the IPCC guidelines [20] and the use of an environmental burden of typical non-region-specific NA. Future work may reduce the uncertainty and enhance the accuracy by determining these values specifically for the city of Abu Dhabi. While RCA produced in Abu Dhabi can be recommended for use in various non-structural applications, including road base and sub-base, structural fill, trench bedding, hardstand and low dust asphalt products, and foundation products, their exclusive use in structural applications still requires further study.
Table 3. Fuel consumed by the equipment operated within the plant and the associated global warming potential (in kg CO2eq).
Equipment | Equipment brand and model | Total amount of diesel used (L/shift) | Global warming potential (kg CO2eq) |
Hydraulic excavator | Komatsu PC300 | 272.4 | 727.0 |
Wheel loader | Komatsu WA470 | 1104.0 | 2946.6 |
Wheel loader | Komatsu WA500 | 396.0 | 1056.9 |
4. Conclusions
Recycled concrete aggregates have been used as a sustainable replacement for natural aggregates in many non-structural applications. This substitution offers various environmental benefits in terms of reducing the consumption of natural resources and lessening the burden on landfills. While most research has focused on optimizing the performance of concrete products made with RCA to be comparable to NA-based counterparts, little to no effort was dedicated to studying the impact of the recycling process in the city of Abu Dhabi, United Arab Emirates. This work aimed to develop a novel, refined, and representative LCI dataset for the RCA production process in the city of Abu Dhabi following the methodology proposed by ISO 14040. The resulting LCI value of RCA production was found to be 0.676 kg CO2eq per ton of aggregates (or 6.67x10-4 kg CO 2eq/kg), which is eight times less than that associated with the production of natural aggregates. This represents a reduction of approximately 87%. It should be noted that the resulting LCI value was developed based on the boundaries set and explained in this study as well as the technology utilized in the recycling processes at the time this study was conducted. Nevertheless, this newly developed LCI value will help improve the accuracy and overall quality of life cycle assessment studies conducted in Abu Dhabi.
5. Acknowledgements
The authors would like to acknowledge Al Dhafra Recycling plant (ADRI) for their cooperation, support, and valuable input towards this study. The financial support of the United Arab Emirates University under grants number 31N409 and 31N398 is also appreciated.
References
[1] R. V. Silva, J. de Brito, and R. K. Dhir, “Use of recycled aggregates arising from construction and demolition waste in new construction applications,” Journal of Cleaner Production, vol. 236, p. 117629, 2019. View Article
[2] C. P. Ginga, J. M. C. Ongpeng, and M. K. M. Daly, “Circular Economy on Construction and Demolition Waste: A Literature Review on Material Recovery and Production,” Materials, vol. 13, no. 13, Art. no. 13, 2020. View Article
[3] A. Mistri, S. K. Bhattacharyya, N. Dhami, A. Mukherjee, and S. V. Barai, “A review on different treatment methods for enhancing the properties of recycled aggregates for sustainable construction materials,” Construction and Building Materials, vol. 233, p. 117894, 2020. View Article
[4] M. Amario, C. S. Rangel, M. Pepe, and R. D. Toledo Filho, “Optimization of normal and high strength recycled aggregate concrete mixtures by using packing model,” Cement and Concrete Composites, vol. 84, pp. 83–92, 2017. View Article
[5] C. Shi, Z. Wu, Z. Cao, T. C. Ling, and J. Zheng, “Performance of mortar prepared with recycled concrete aggregate enhanced by CO2 and pozzolan slurry,” Cement and Concrete Composites, vol. 86, pp. 130–138, 2018. View Article
[6] K. P. Verian, W. Ashraf, and Y. Cao, “Properties of recycled concrete aggregate and their influence in new concrete production,” Resources, Conservation and Recycling, vol. 133, pp. 30–49, 2018. View Article
[7] D. Rodríguez-Robles, J. García-González, A. Juan-Valdés, J. M. Morán-del Pozo, and M. I. Guerra-Romero, “Quality Assessment of Mixed and Ceramic Recycled Aggregates from Construction and Demolition Wastes in the Concrete Manufacture According to the Spanish Standard,” Materials, vol. 7, no. 8, pp. 5843–5857, 2014. View Article
[8] R. V. Silva, J. de Brito, and R. K. Dhir, “Properties and composition of recycled aggregates from construction and demolition waste suitable for concrete production,” Construction and Building Materials, vol. 65, pp. 201–217, 2014. View Article
[9] J. Yang, Q. Du, and Y. Bao, “Concrete with recycled concrete aggregate and crushed clay bricks,” Construction and Building Materials, vol. 25, no. 4, pp. 1935–1945, 2011. View Article
[10] A. Klang, P.-Å. Vikman, and H. Brattebø, “Sustainable management of demolition waste—an integrated model for the evaluation of environmental, economic and social aspects,” Resources, Conservation and Recycling, vol. 38, no. 4, pp. 317–334, 2003. View Article
[11] F. López Gayarre, C. López-Colina, M. A. Serrano, and A. López-Martínez, “Manufacture of concrete kerbs and floor blocks with recycled aggregate from C&DW,” Construction and Building Materials, vol. 40, pp. 1193–1199, 2013. View Article
[12] M. N. Soutsos, K. Tang, and S. G. Millard, “Use of recycled demolition aggregate in precast products, phase II: Concrete paving blocks,” Construction and Building Materials, vol. 25, no. 7, pp. 3131–3143, 2011. View Article
[13] Md. U. Hossain, C. S. Poon, I. M. C. Lo, and J. C. P. Cheng, “Comparative environmental evaluation of aggregate production from recycled waste materials and virgin sources by LCA,” Resources, Conservation and Recycling, vol. 109, pp. 67–77, 2016. View Article
[14] N. Kachouh, H. El-Hassan, and T. El Maaddawy “Influence of steel fibers on the flexural performance of concrete incorporating recycled concrete aggregates and dune sand,” J. Sust. Cem. Based Mater., pp. 1–28, 2020. View Article
[15] N. Kachouh, H. El-Hassan, and T. El-Maaddawy, “Effect of steel fibers on the performance of concrete made with recycled concrete aggregates and dune sand,” Construction and Building Materials, vol. 213, pp. 348–359, 2019. View Article
[16] P. Zhu, Y. Hao, H. Liu, X. Wang, and L. Gu, “Durability evaluation of recycled aggregate concrete in a complex environment,” Journal of Cleaner Production, vol. 273, p. 122569, 2020. View Article
[17] S. Ismail and M. Ramli, “Engineering properties of treated recycled concrete aggregate (RCA) for structural applications,” Construction and Building Materials, vol. 44, pp. 464–476, 2013. View Article
[18] V. Revilla-Cuesta, M. Skaf, F. Faleschini, J. M. Manso, and V. Ortega-López, “Self-compacting concrete manufactured with recycled concrete aggregate: An overview,” Journal of Cleaner Production, vol. 262, p. 121362, 2020. View Article
[19] C. M. Mah, T. Fujiwara, and C. S. Ho, “Life cycle assessment and life cycle costing toward eco-efficiency concrete waste management in Malaysia,” Journal of Cleaner Production, vol. 172, pp. 3415–3427, 2018. View Article
[20] IPCC, “IPCC Guidelines for National Greenhouse Gas Inventories (2006). The Intergovernmental Panel on Climate Change.” Jun. 2019, Accessed: Sep. 07, 2019. [Online]. Available: View Article
[21] ISO 14040, “Environmental management - Life cycle assessment - Principles and framework.” International Organization for Standardization, 2006, Accessed: Jul. 20, 2019. [Online]. Available: View Article
[22] M. Alzard, M. A. Maraqa, R. Chowdhury, M. Sherif, T. I. Mauga, F. B. D. Albuquerque, and K. Aljunadi, “RoadCO2: A web-based tool for estimation of greenhouse gas emissions of road projects,” presented at the 2nd Advances in Science and Engineering Technology multi-conferences (ASET’19), Dubai - United Arab Emirates, Mar. 2019. View Article
[23] Y. Perk, “An aerial view of Al Dhafra Recycling plant.” Google Maps, Oct. 2019, [Online]. Available: View Article
[24] M. M. Aman, K. H. Solangi, M. S. Hossain, A. Badarudin, G. B. Jasmon, H. Mokhlis, A. H. A. Bakar, and S. N. Kazi, “A review of Safety, Health and Environmental (SHE) issues of solar energy system,” Renewable and Sustainable Energy Reviews, vol. 41, pp. 1190–1204, 2015. View Article
[25] Komatsu, “Komatsu Specifications and Application Handbook Edition 31.” Apr. 2013, Accessed: Sep. 07, 2019. [Online]. Available: View Article
[26] CarbonSolutions, “Inventory of Carbon & Energy (ICE) Summary.” Jan. 2011, Accessed: Jul. 27, 2019. [Online]. Available: View Article